THE BEEZLEE BLOG
Corner Jigs made with Shaper Origin
Well, it’s the holiday season again. I enjoy trying to make at least a couple gifts each year if I have time. This year I have plans to make my kids a couple things and I need some corner jigs for the project. I shopped around a bit but I’m really not a fan of the plastic ones from Rockler and I sure don’t want to spend $300 (!!!) on the metal ones that Woodpeckers offers from time to time as a OneTime Tool.
So, I quickly designed a template in Adobe Illustrator and made separate files for each jig ranging from 1/2” to 2” radius. Of course, I needed a place to store them so I also designed a french cleat storage rack to keep them organized and out of the way.
There are a few reasons I used the Festool Dominoes as the stops.
It was easy :-)
They’re sturdy because they are solid wood
They can be adjusted for different material thicknesses
I can easily replace them if needed
Make a set for yourself
Here is the complete set of jigs and french cleat wall rack:
If you have a Shaper Origin, below are the steps for making your own set of corner jigs.
You may use either the file linked above or the individual files below.
If using the complete file above, you’ll need a piece of 3/4” plywood at least 27.5”W x 17”H. Or each jig can be cut from a 6” x 6” piece of ply.
After placing the image on your material, use an engraving bit to engrave all of the numbers.
Now use the 1/4” bit to make three passes around all of the parts.
Cut depth = 1/4”, Offset = .03”
Cut Depth = 1/2”, Offset = .03”
Final Cut - Cut Depth = 3/4”, Offset = 0” (take it slow for a clean cut when going around the corner that will be used for guide bearing)
Make sure to cut out the Domino mortises and handle BEFORE cutting around the outside of each jig. Once you cut the outside of the jig you won’t be able to cut the internal mortises or handle.
(Opt) Use a fine tip Sharpie to color in the radius measurement
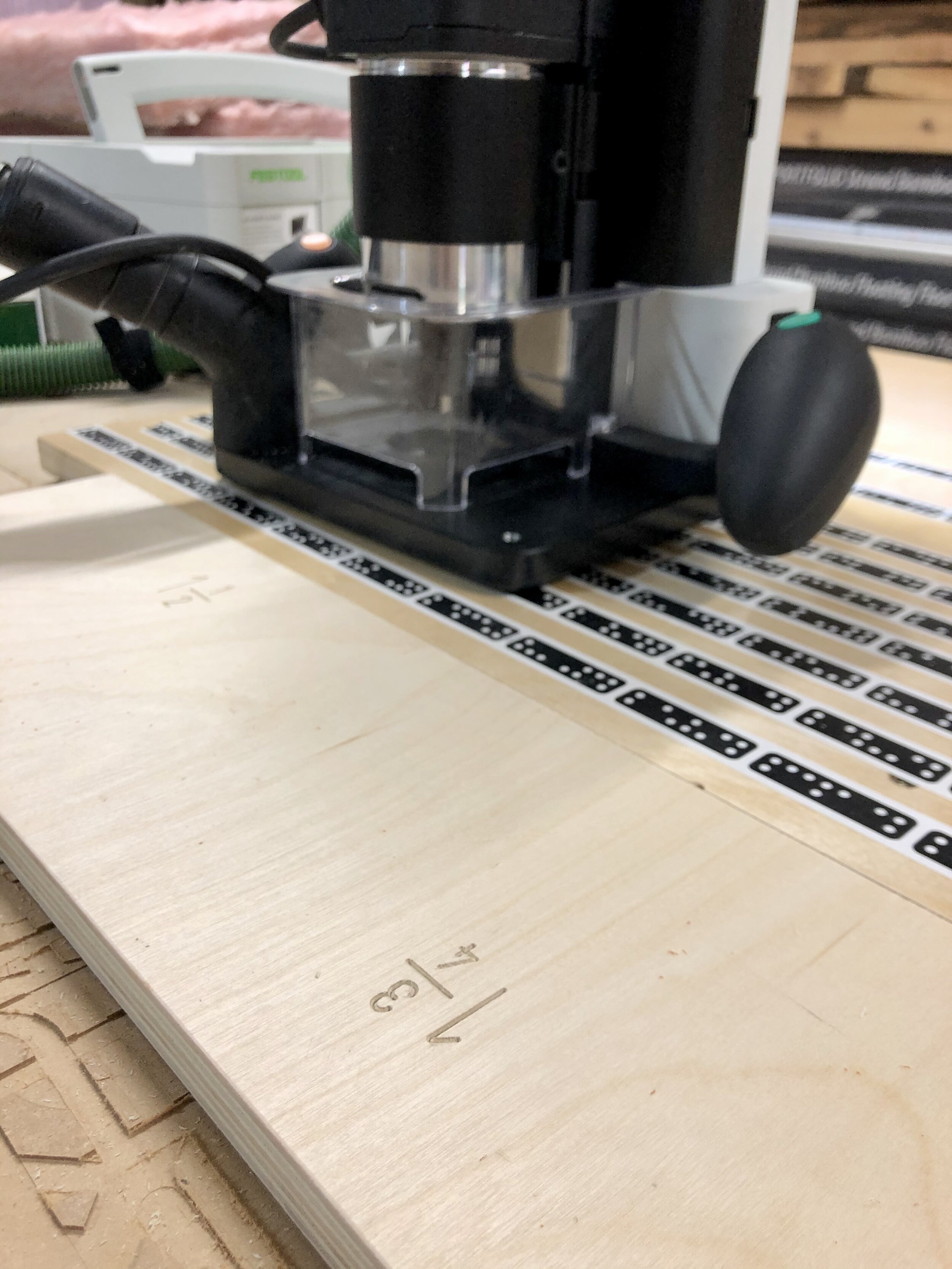
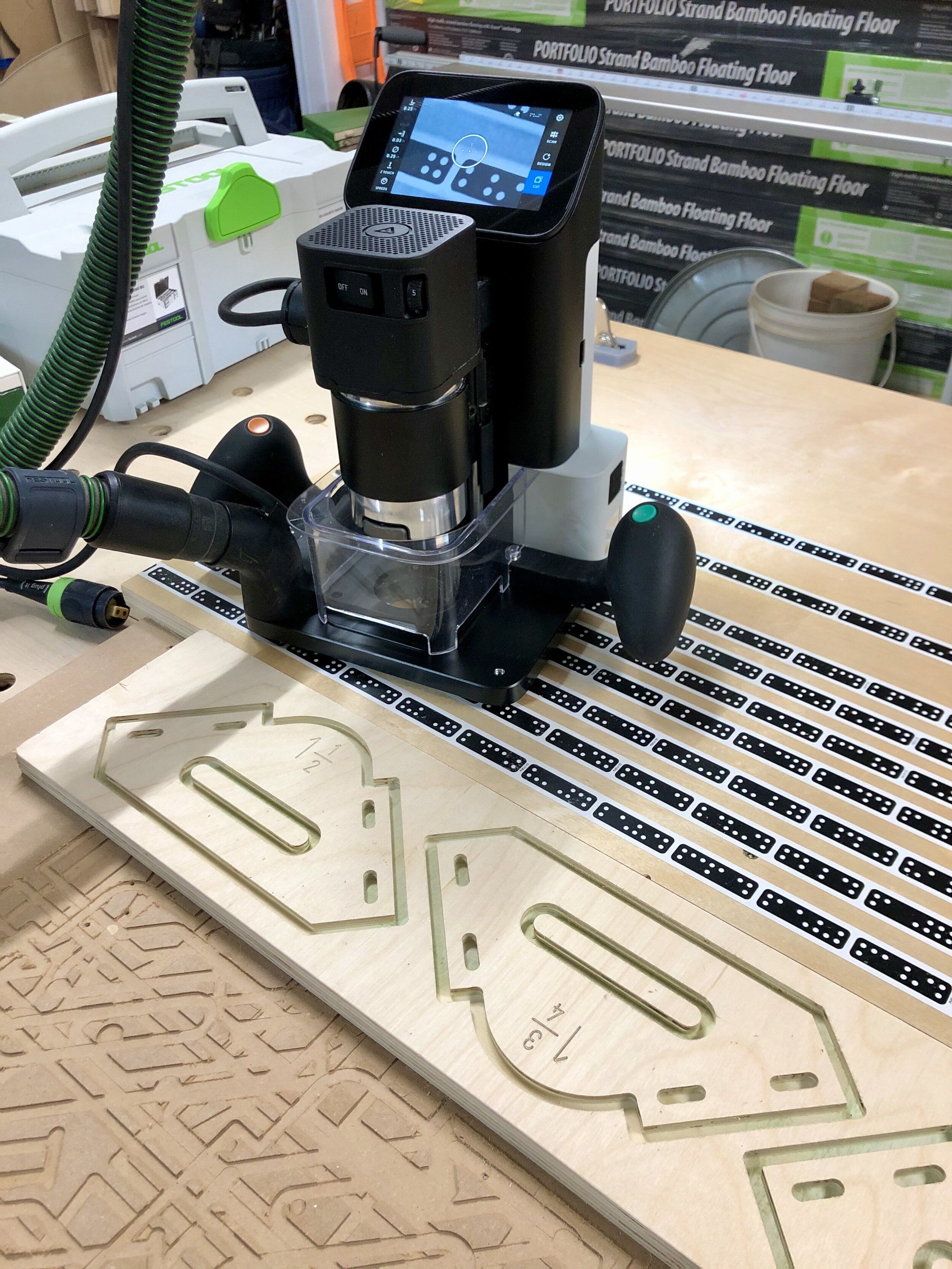
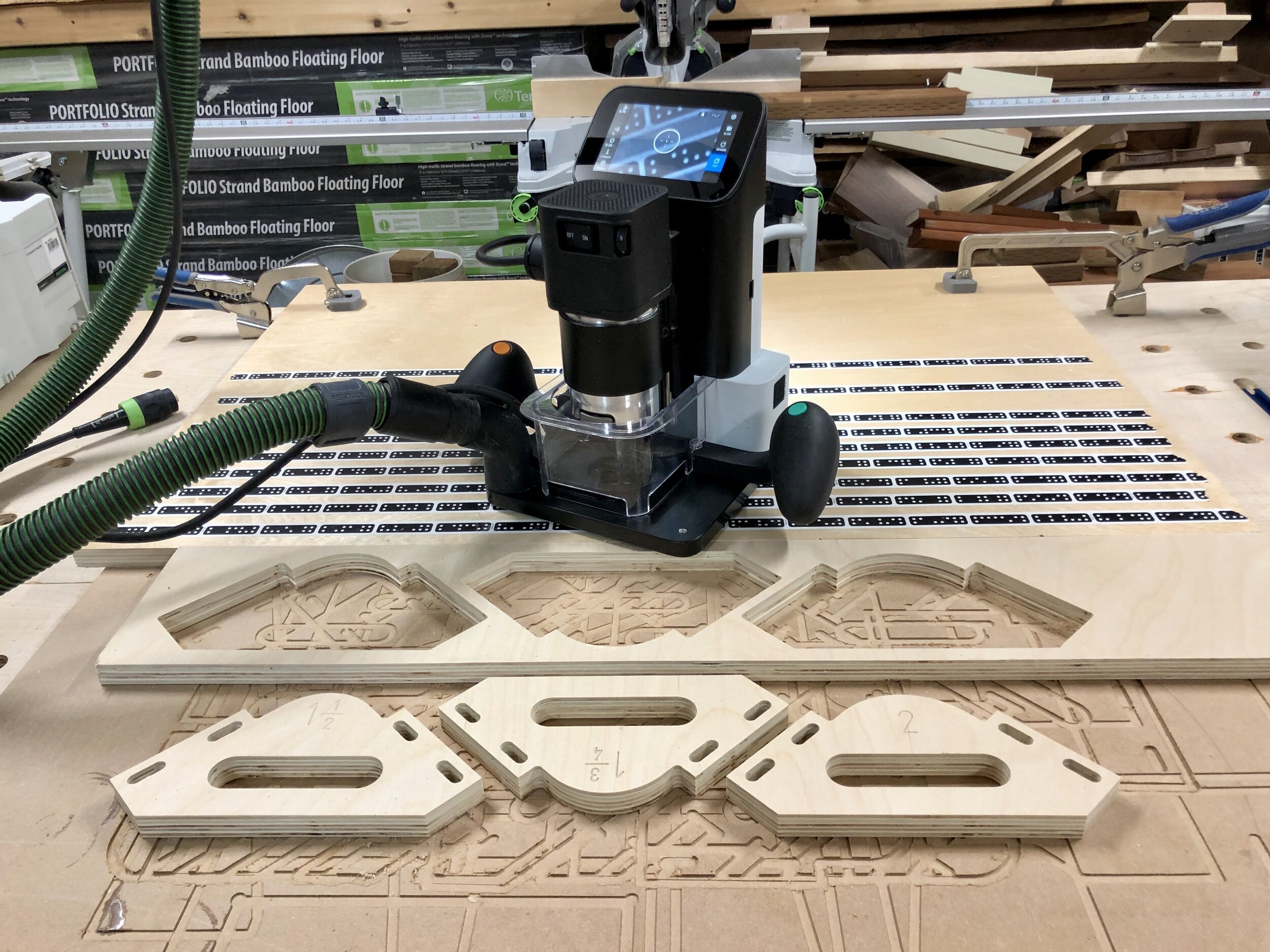
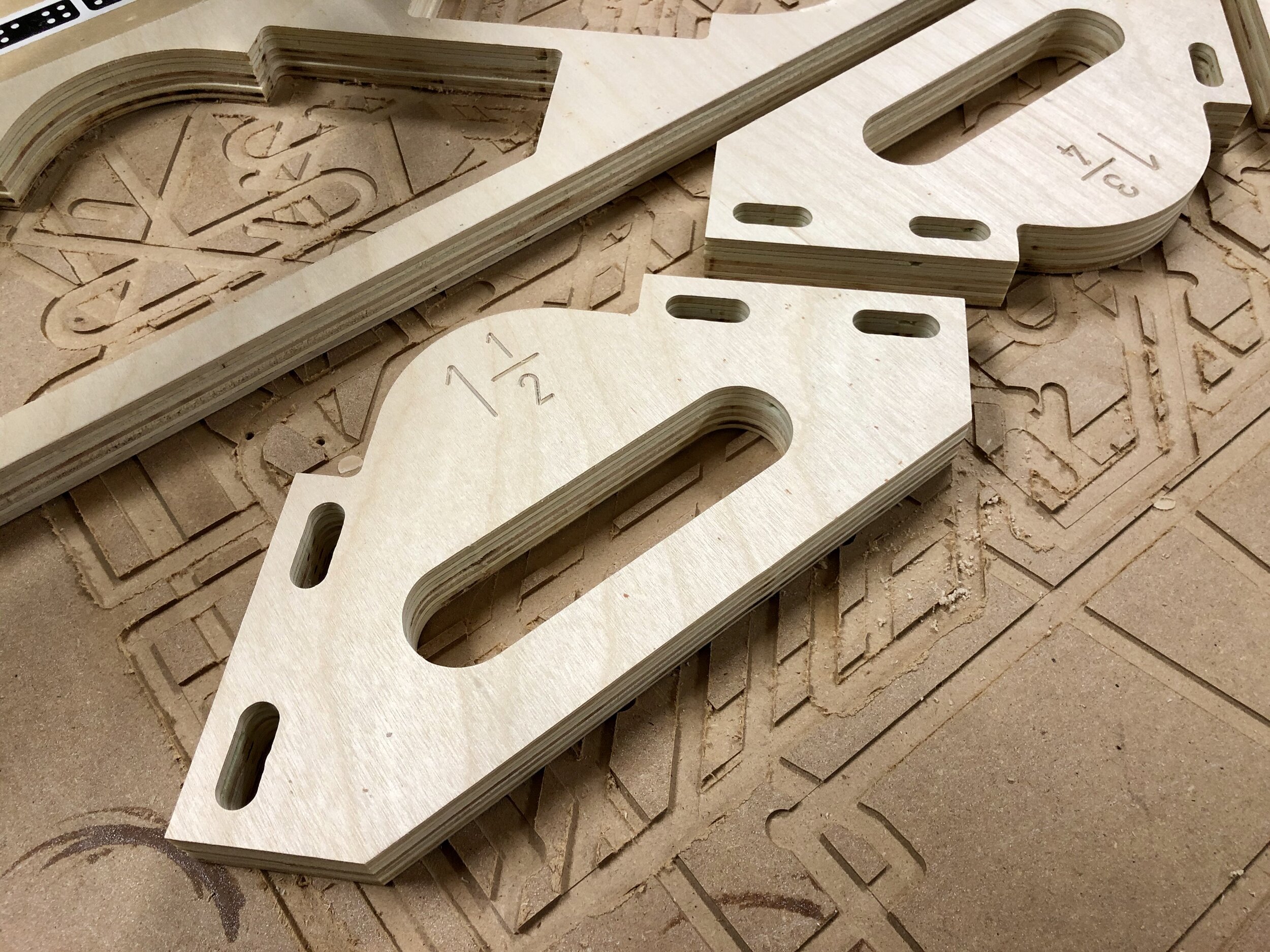
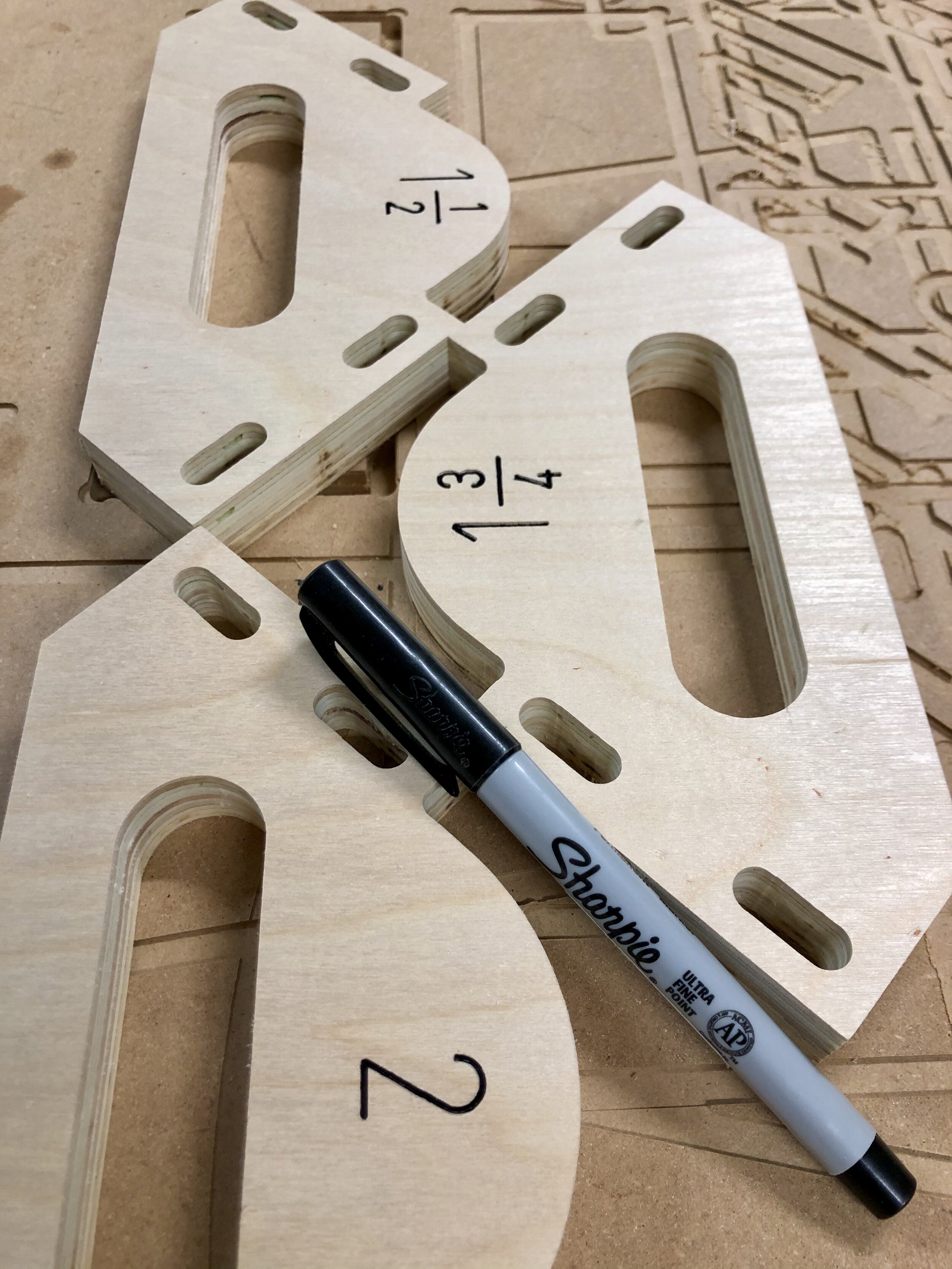
7. (Opt) Sand off about 5mm of the length of each 8mm x 50mm Domino. (The reason will be made clear in the next couple of steps.)
8. Lay the jig on a flat work surface; insert the Dominoes and tap them down so they are flat with the underside of the jig.
9. Now put the jig on a piece of 3/4” plywood and tap the Dominoes down to the work surface. If you’re sanding 5mm off of the Dominoes in Step 7, you’ll now have the correct length for 3/4” material on one side and 1/2” material on the other WITHOUT having to adjust the Dominoes. ;-) You could glue them in place but since the mortises will be tight it’s not necessary. Plus you can adjust the height of them later if needed.
10. I glued and nailed the rack pieces to the side of the rack divider.
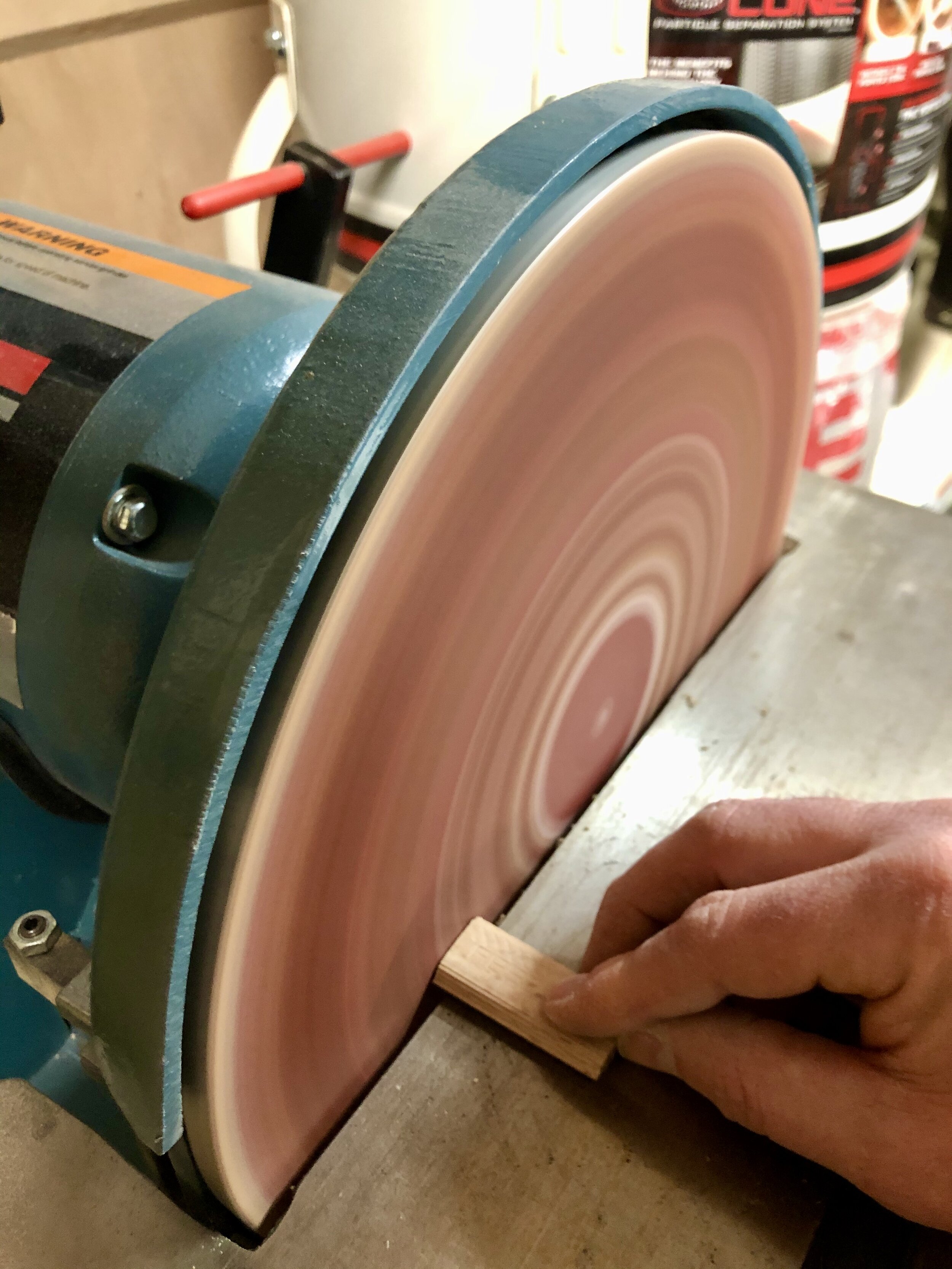
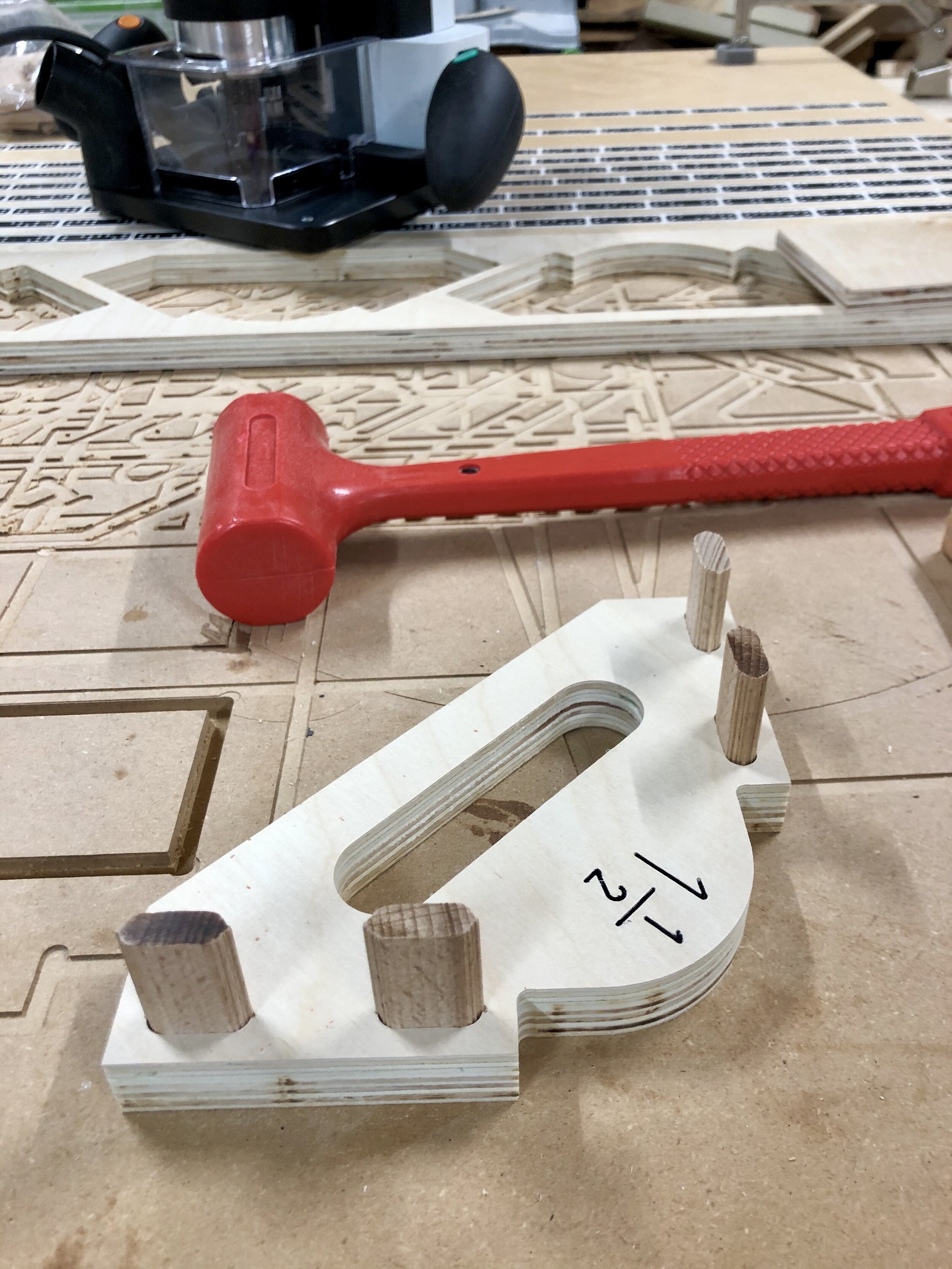
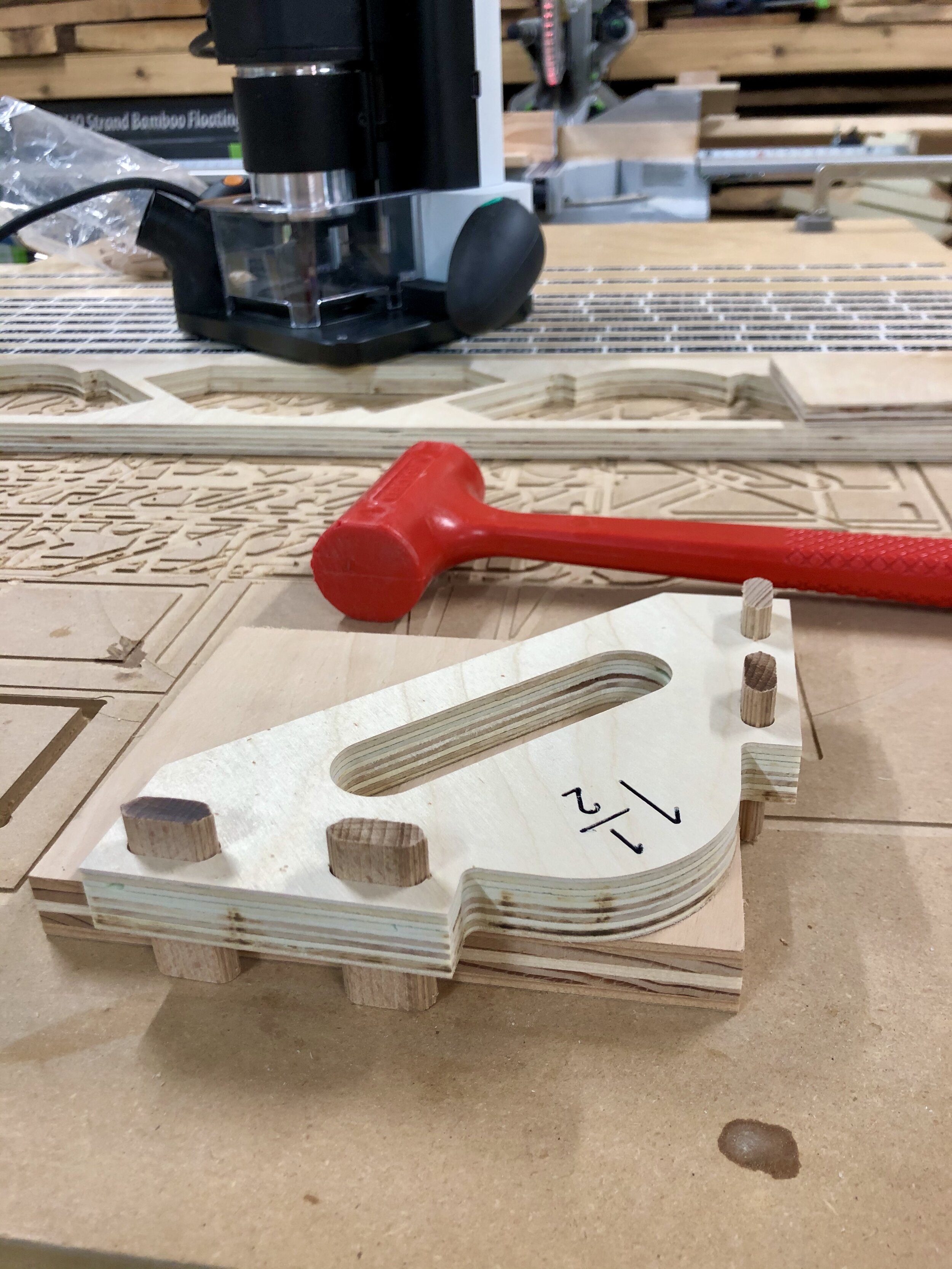

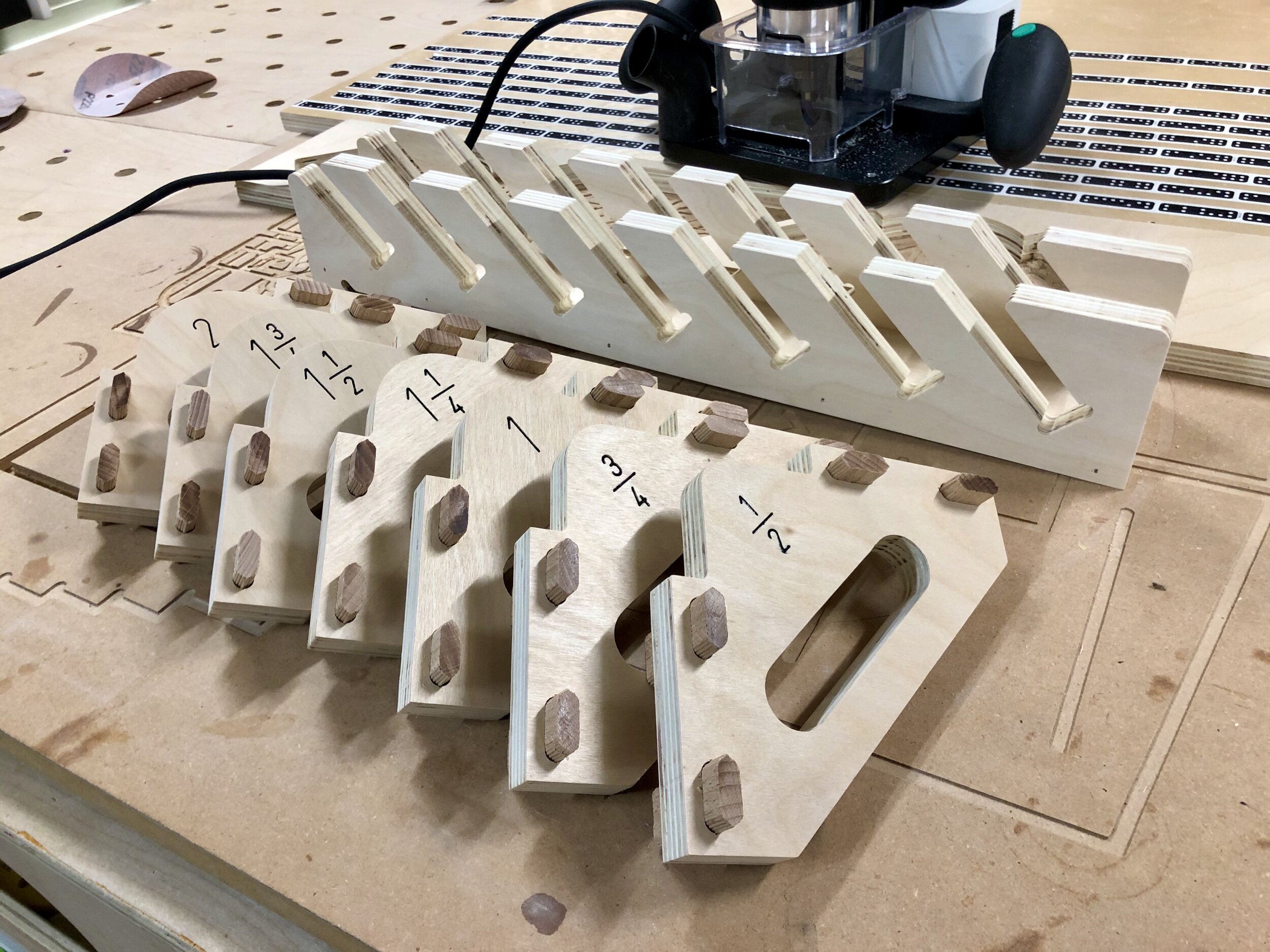
To use them just put the jig over the material, adjust the height of the router guide bit so the guide bearing is riding against the jig and hold the jig tight against the corner of the work piece.
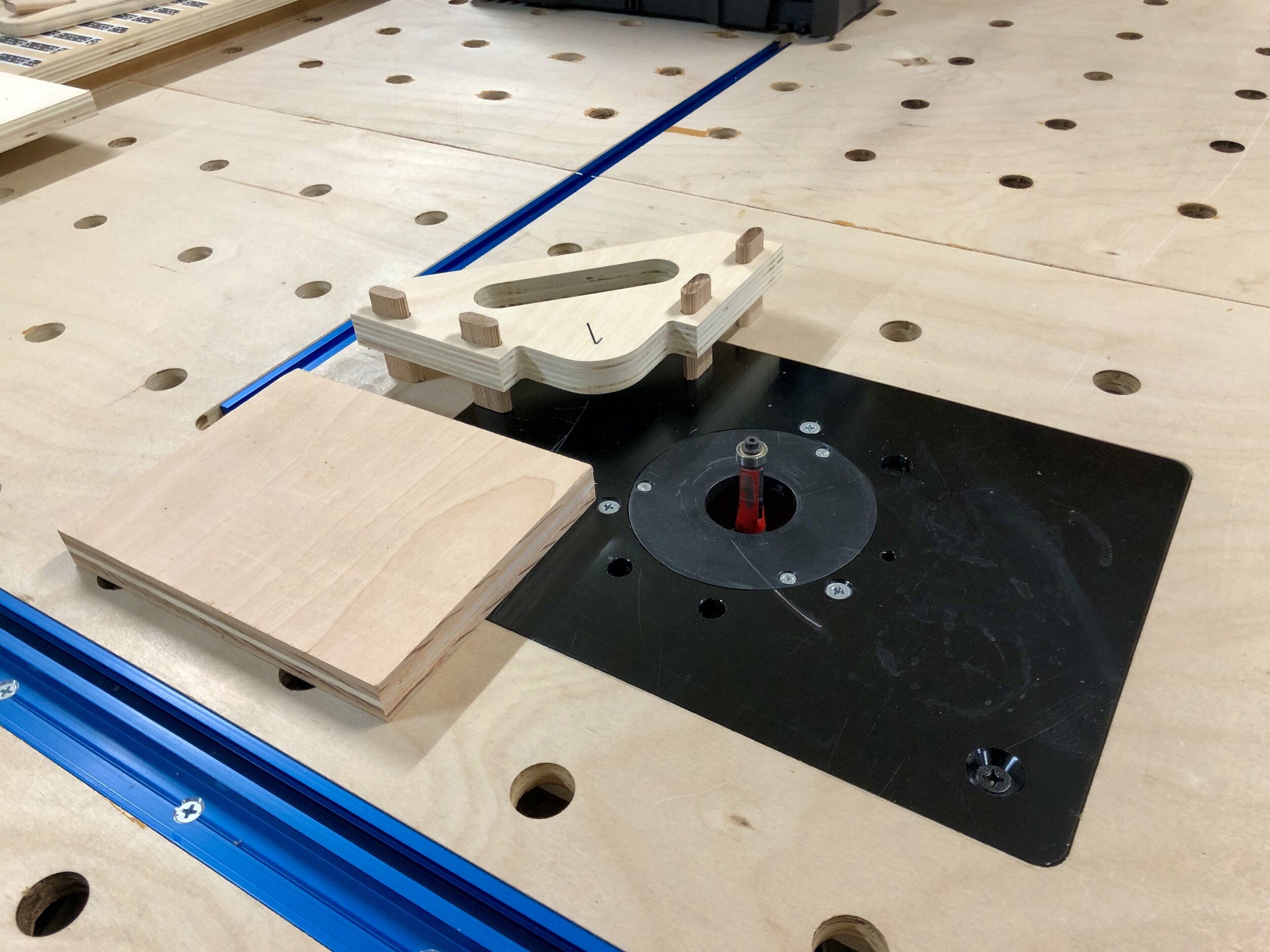
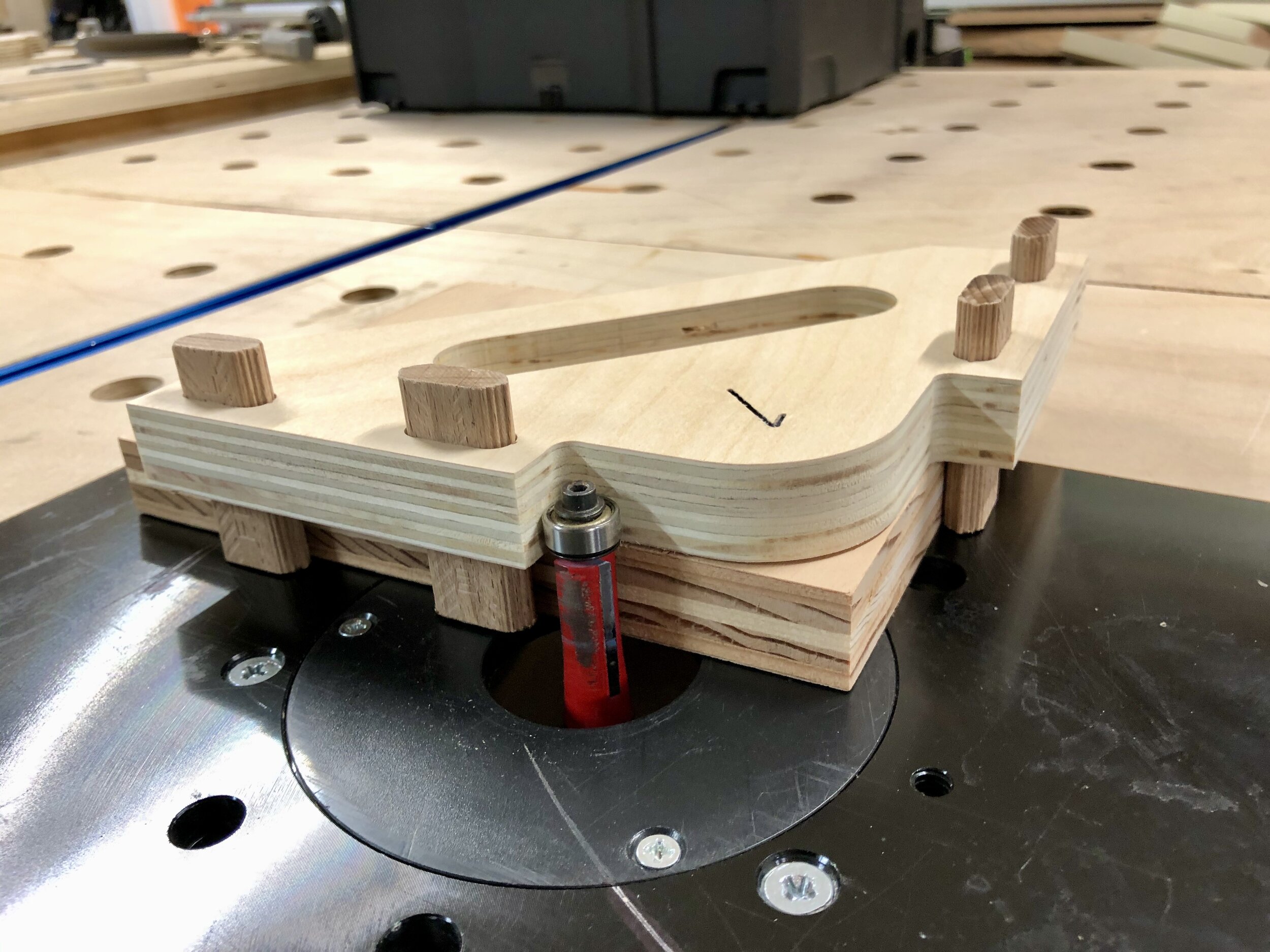
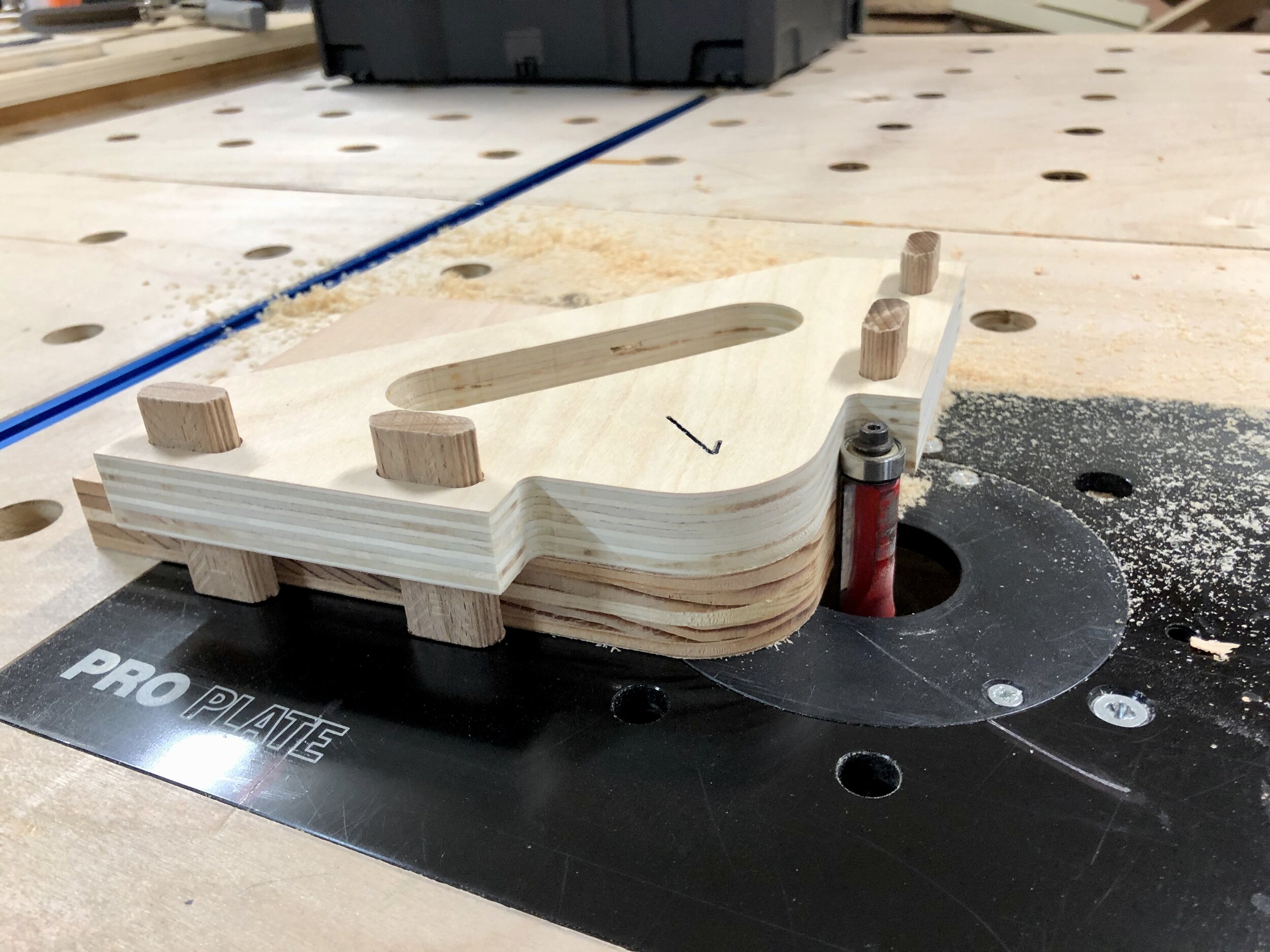
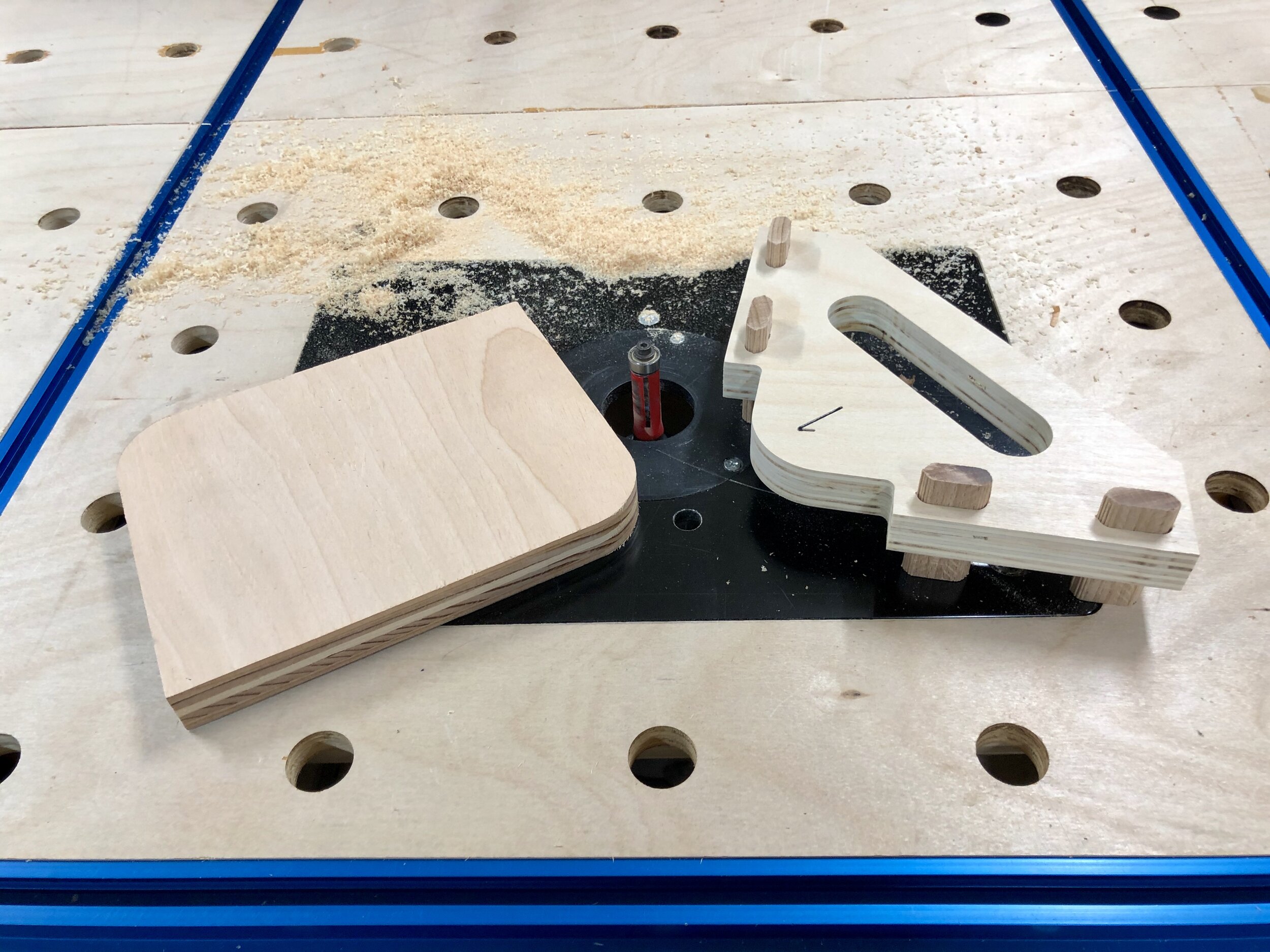
I’m pretty happy with how they turned out. I may add a couple of strips of thin rubber to the underside to help from it slipping but I can do that later.
Individual .svg files:
Corner Jig 1/4”
Corner Jig 1/2”
Corner Jig 3/4”
Corner Jig 1”
Corner Jig 1-1/4"
Corner Jig 1-1/2”
Corner Jig 1-3/4”
Corner Jig 2”
Rack
Please let me know if you have any comments or would like me to create another size jig.
As always, I hope this helps.
Cheers,
Lee
Tools and Materials used
Horizontal Support for Shaper Origin "Ultimate" Vertical Workstation
I know it’s been a while since my last post but time flies when you’re having fun (or working on a lot of different projects).
Anyway, I’ve been thinking about making some Xmas presents and I was inspired by something I saw from “Mike the Maker” on Instagram. My friends and I are into the Game of Thrones show and I thought it was pretty clever to make a doorstop with the word “HODOR” engraved on it. I could absolutely use the Shaper Origin to do the engraving but I was trying to figure out how to engrave something on a wedge shaped piece of wood.
Since the width would fit in the opening of the “Ultimate” Vertical Workstation (UVW) I made I just needed to figure out a way to hold it so the surface of the wedge was level with the top surface of the UVW.
My first attempt was using the vertical support to set the angle and then a block of wood to support the wedge. It didn’t work very well because it was difficult to clamp the thick block, which is when the Horizontal Support was born!
I built a three versions before settling on this one. v1 had parallel sides which limited the angles side to side that I could use it at. v2 had angled sides but was tall and wide. This stuck out a bit too far when mounting it on the side when not in use (you’ll see later) and the slots for the clamping knobs were not distributed at the same width as t-tracks are vertically. I’ll also show you why this is important in a minute. So here is v3…
Here is the SVG that I used…
Cutting and Assembly Steps
1. Cut the mortises for the Dominos in the top using the Shaper Origin. Because the top is quite small it was difficult to cut them out with the DF500 after the top was cut out so I researched the exact size of the holes made at the various settings and added tight mortises on the outsides and a medium mortise for the middle. (Use a 1/8” bit, Inside Cut, 2 passes at 7mm and 15mm deep, 0” offset) [please excuse the holes in the scrap piece of plywood I used shown in the pictures]
2. Cut out the pockets for the supports. These are 18mm wide but check the thickness of your material and adjust with offset accordingly (Use 1/4” bit, 1/4” deep, Pocket Cut then Inside Cut at 0” offset)
3. Cut the slots for clamping knobs. (Use 1/4” bit, Outside Cut, 0” offset, 3 passes [1/4”, 1/2”, 3/4” deep])
4. Cut out the bottom. I start with cutting out lower pieces to full depth because it doesn’t destroy the marker tape higher on the work surface. Those people that have used the Origin will know what I’m talking about. :-)
5. Cut out top
6. Cut out supports
7. Use the Festool Domino DF500 to mortise the three dominos in the bottom piece. Use the indexing pins to measure the side mortises. Make a mark at the center (150mm from either side) for the center mortise. Feel free to use tight or medium mortises for alignment
8. Glue mortises and channels for supports, assemble and then clamp to right angles to ensure that the top surface will be flush with the top of the UVW when tightened to the t-tracks.
9. OPTIONAL - If you’ve already built the UVW then you’ll need to drill holes in the side to mount the Horizontal Support when not in use. (I have also updated the .svg file on the UVW to include this mounting holes.)
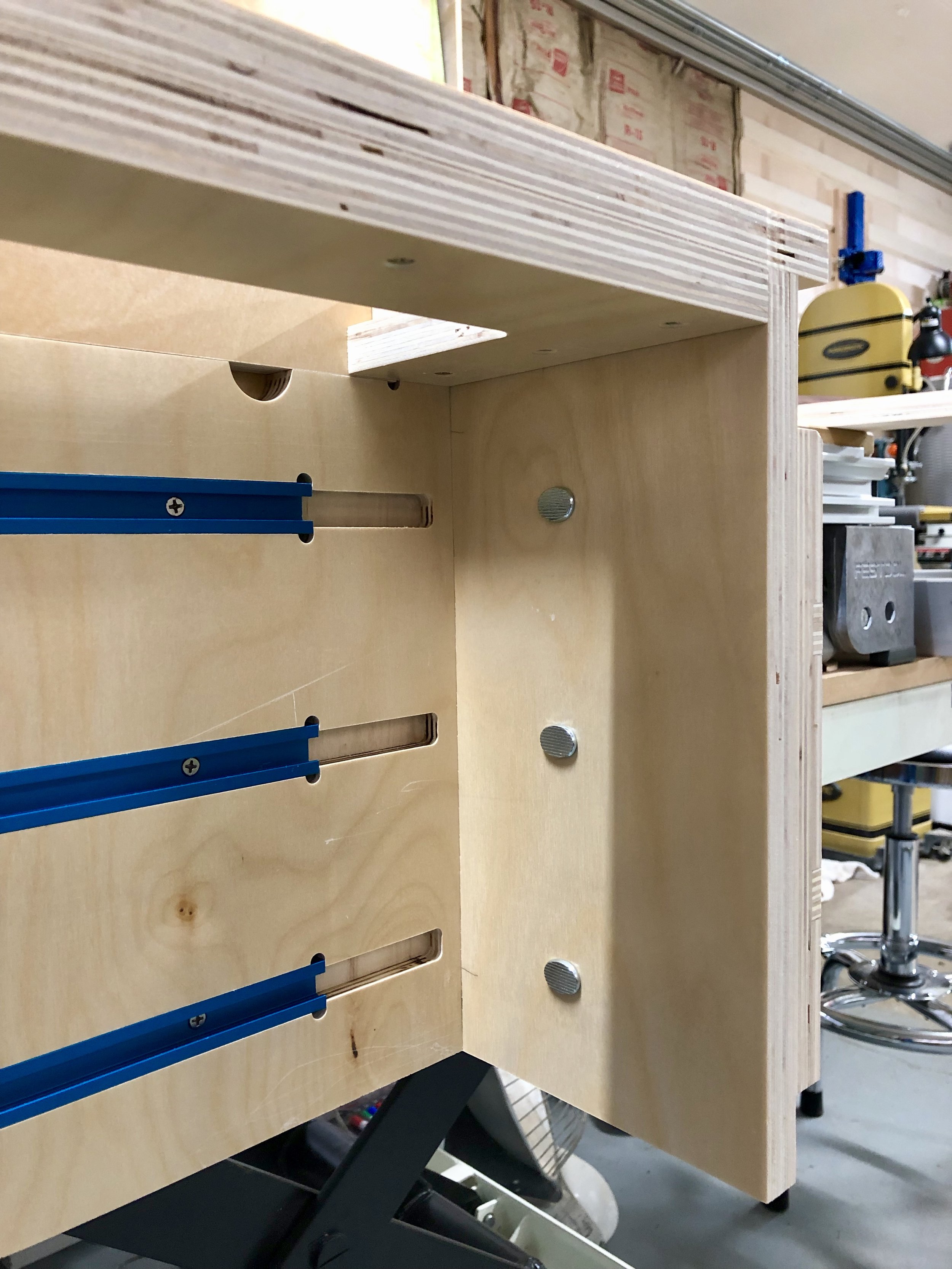
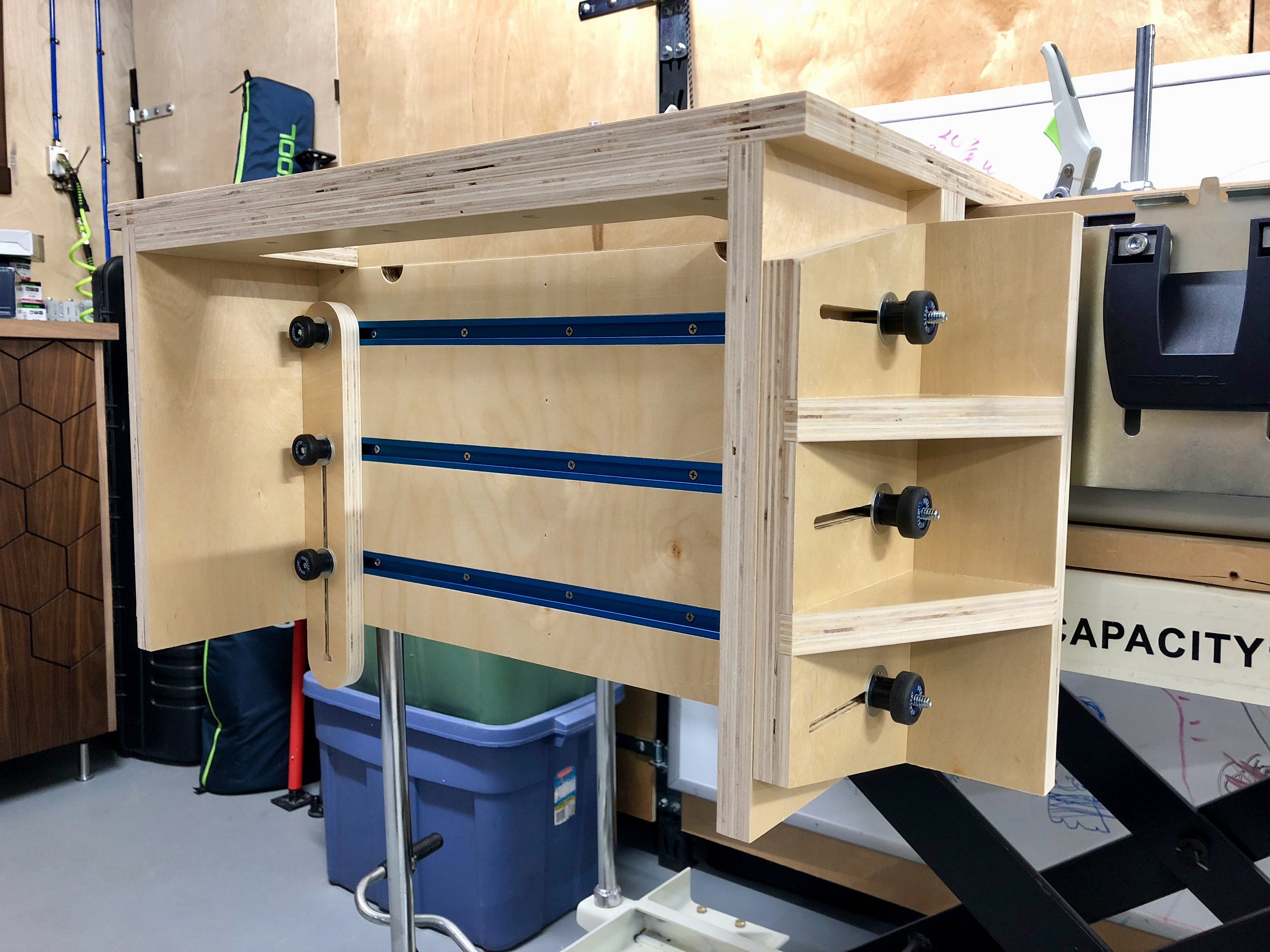
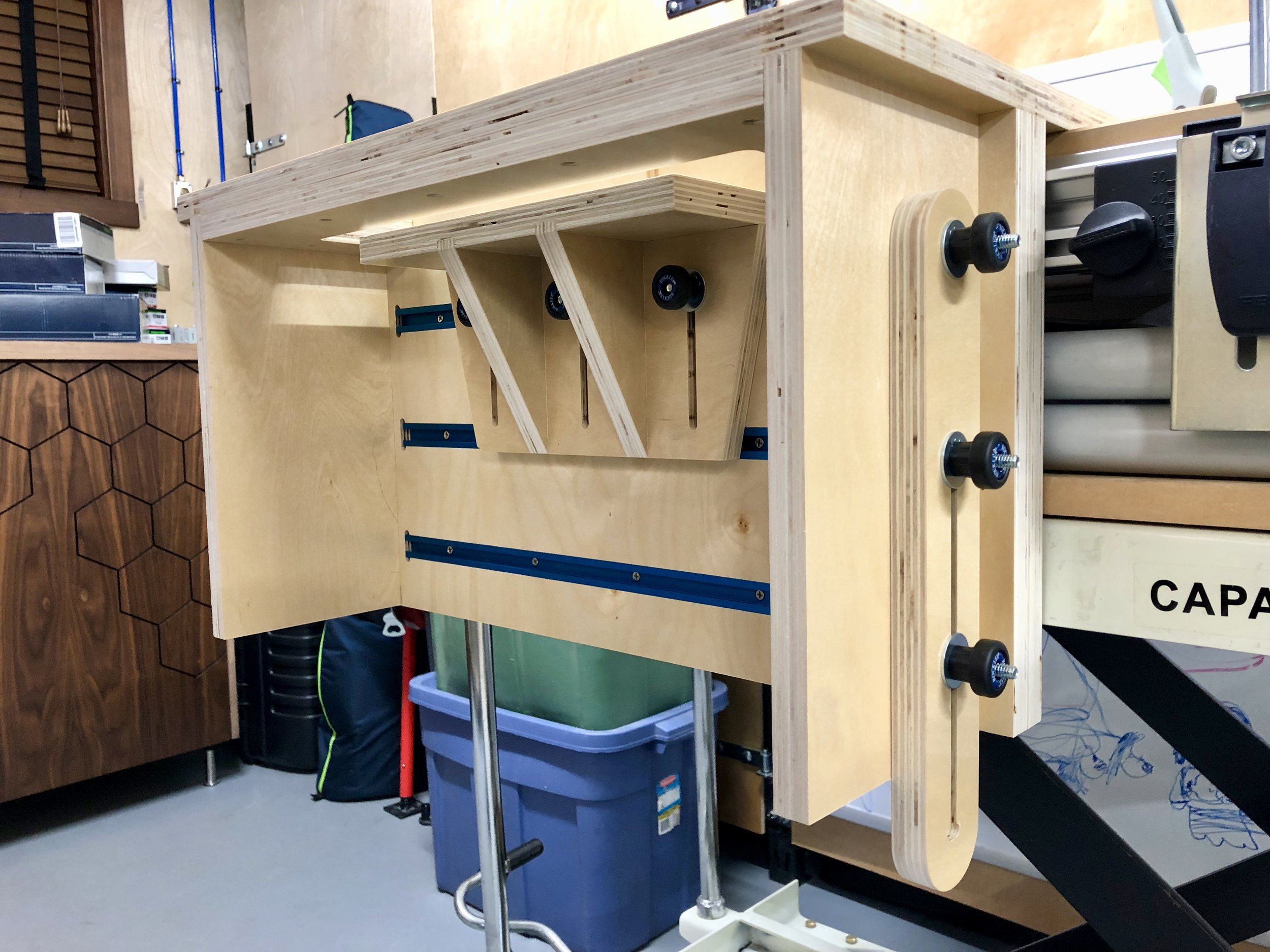
This is also a place for an extra set of t-bolts so both the vertical and horizontal supports can be used at the same time if needed.
Using the Horizontal Support (HS)
Hold the HS below the T-track, position the t-bolts above the slots, slide the HS over the bolts and add the washers and clamping knobs.
Mount the work piece to the HS with double-sided tape.
Clamp a flat board on to the top of the UVW
Push the work piece up to the underside of the flat board
Tighten the clamping knobs and remove the flat board from the top of the UVW
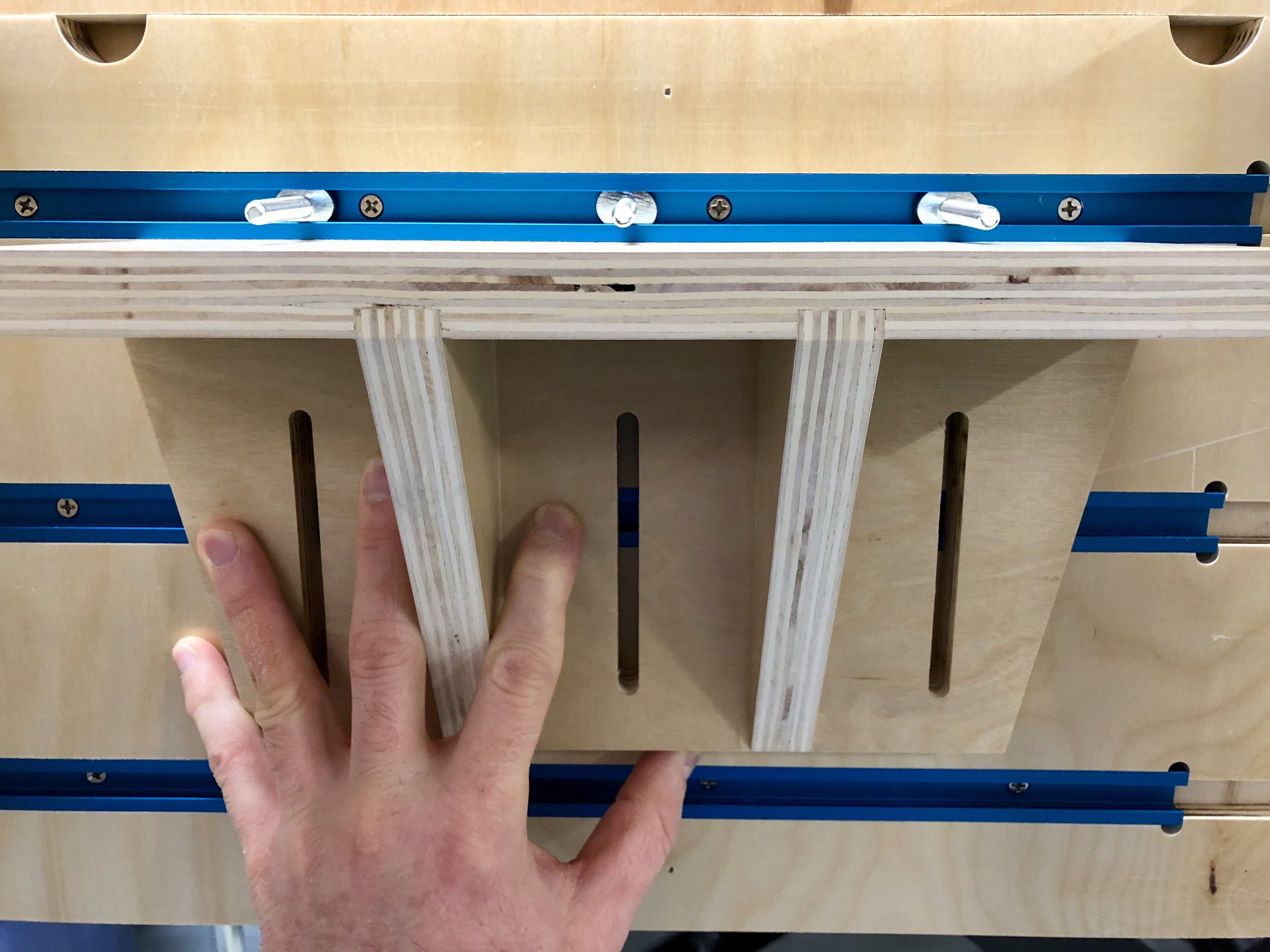
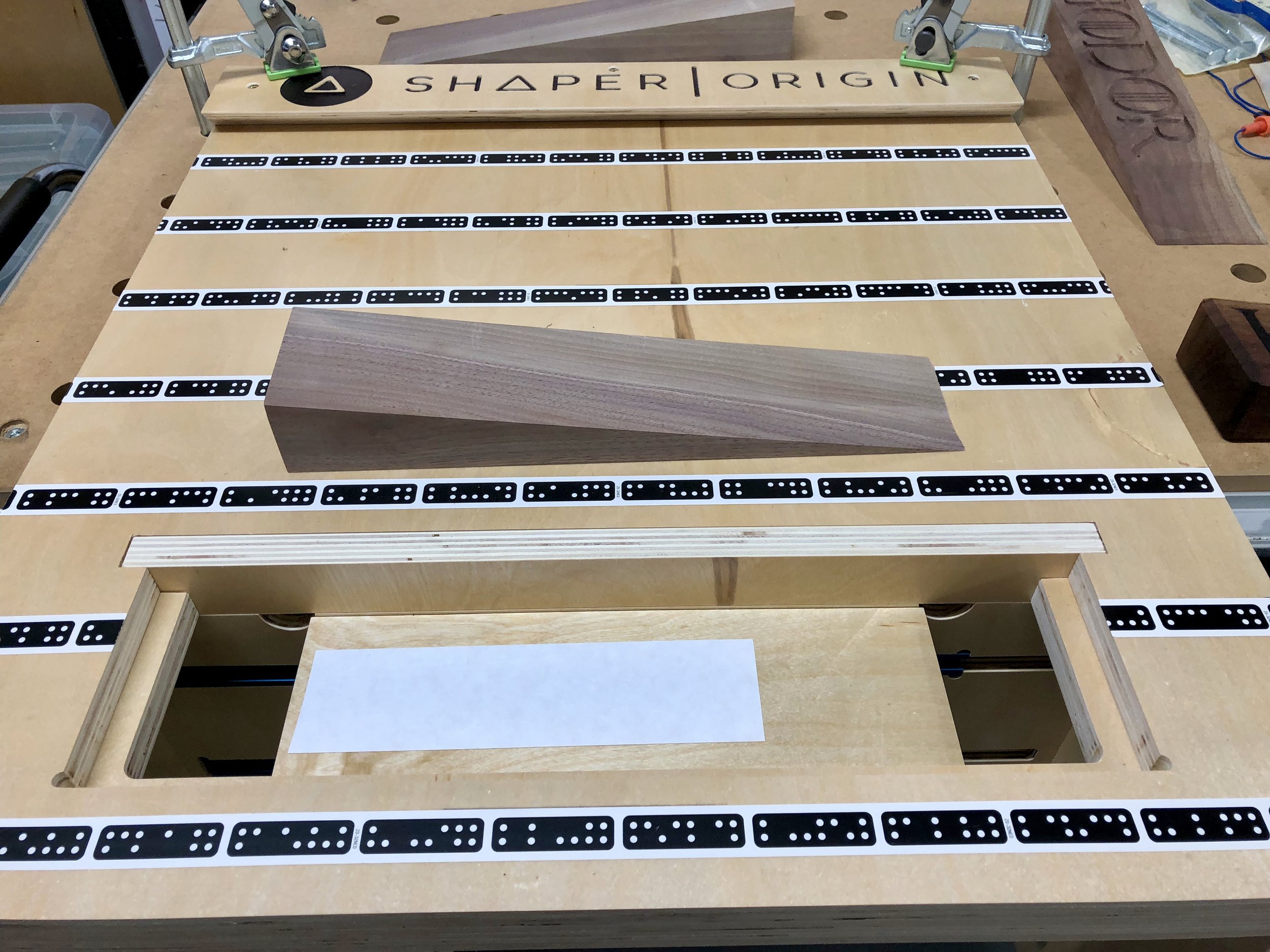
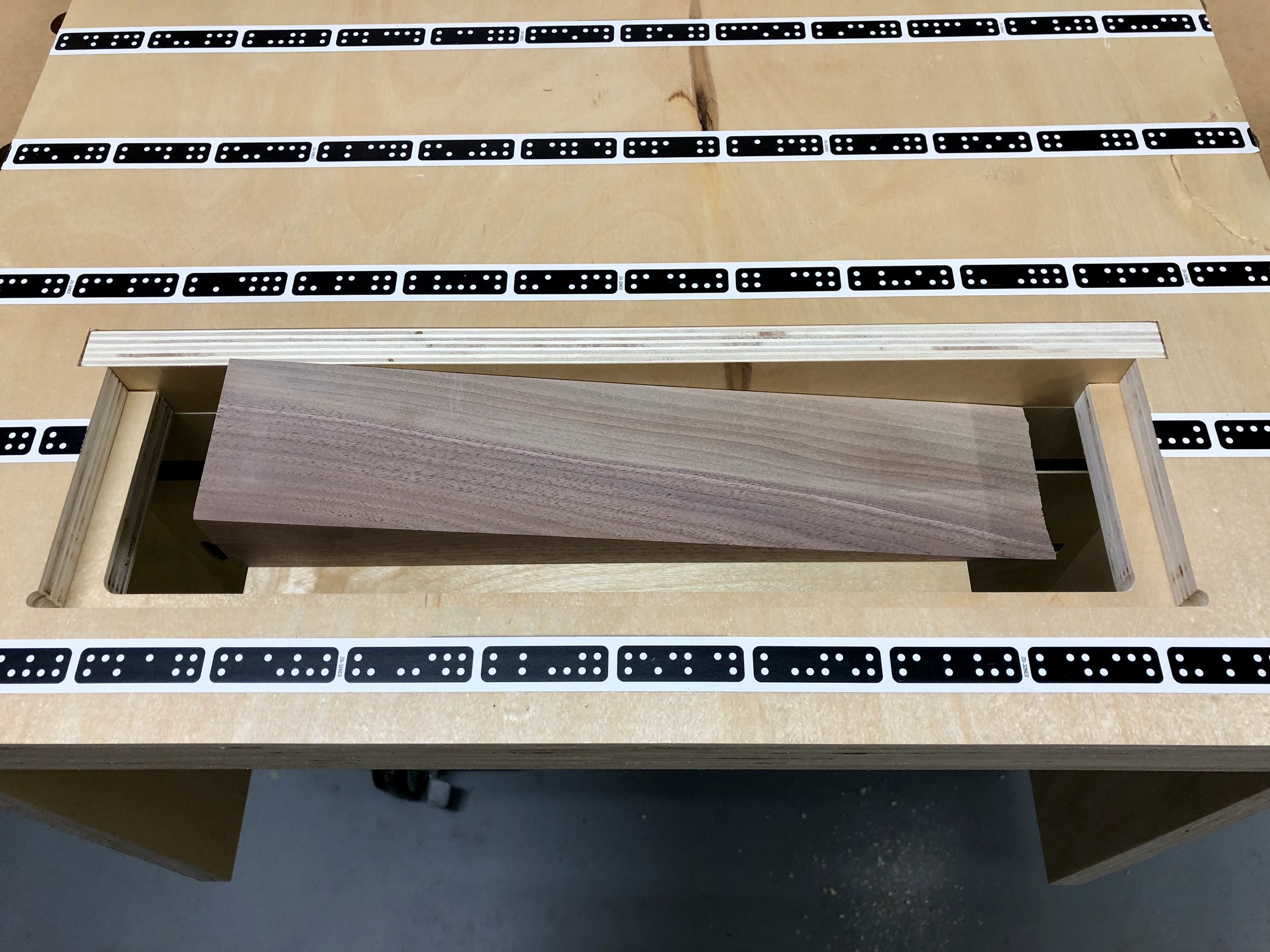
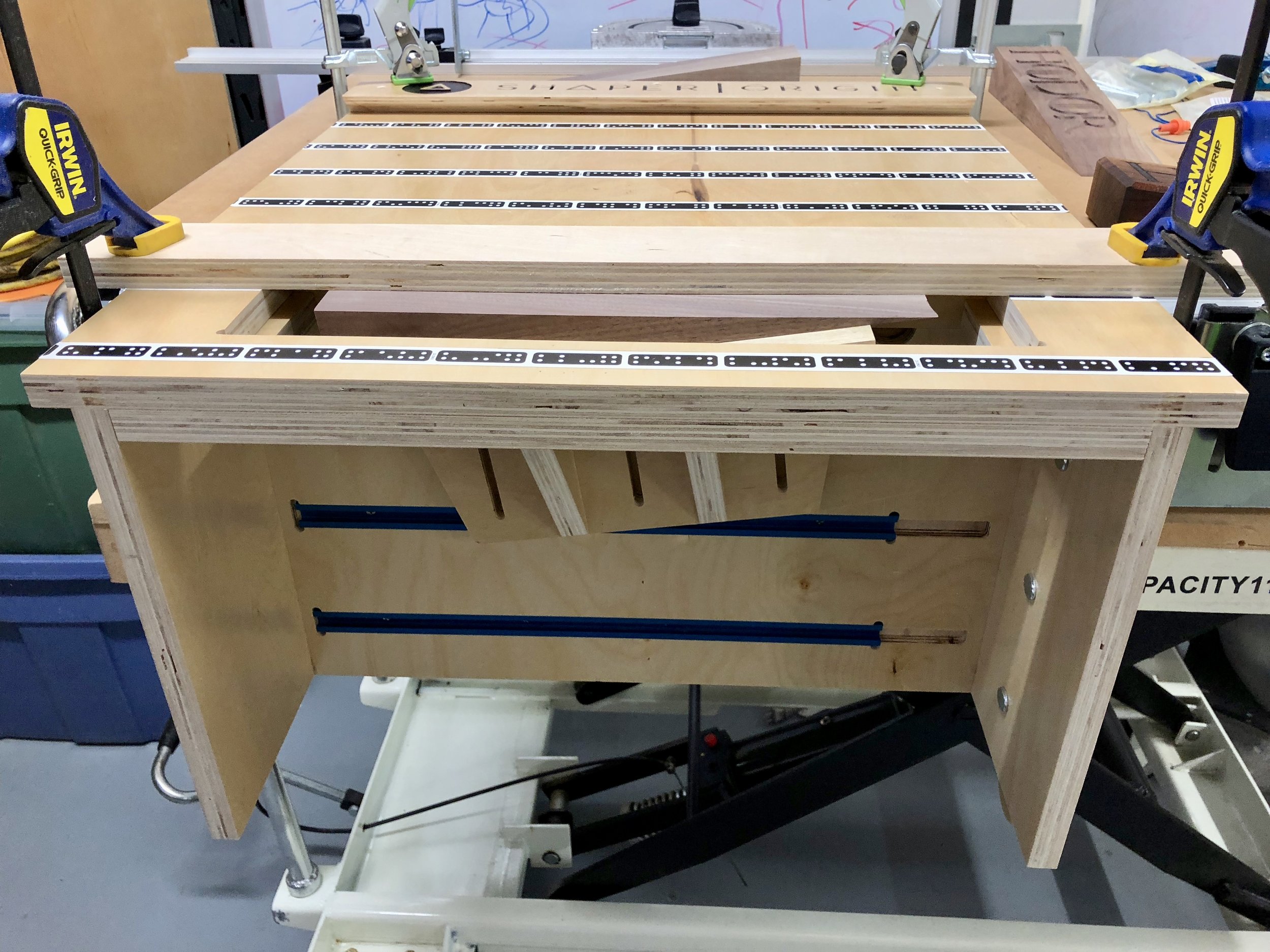
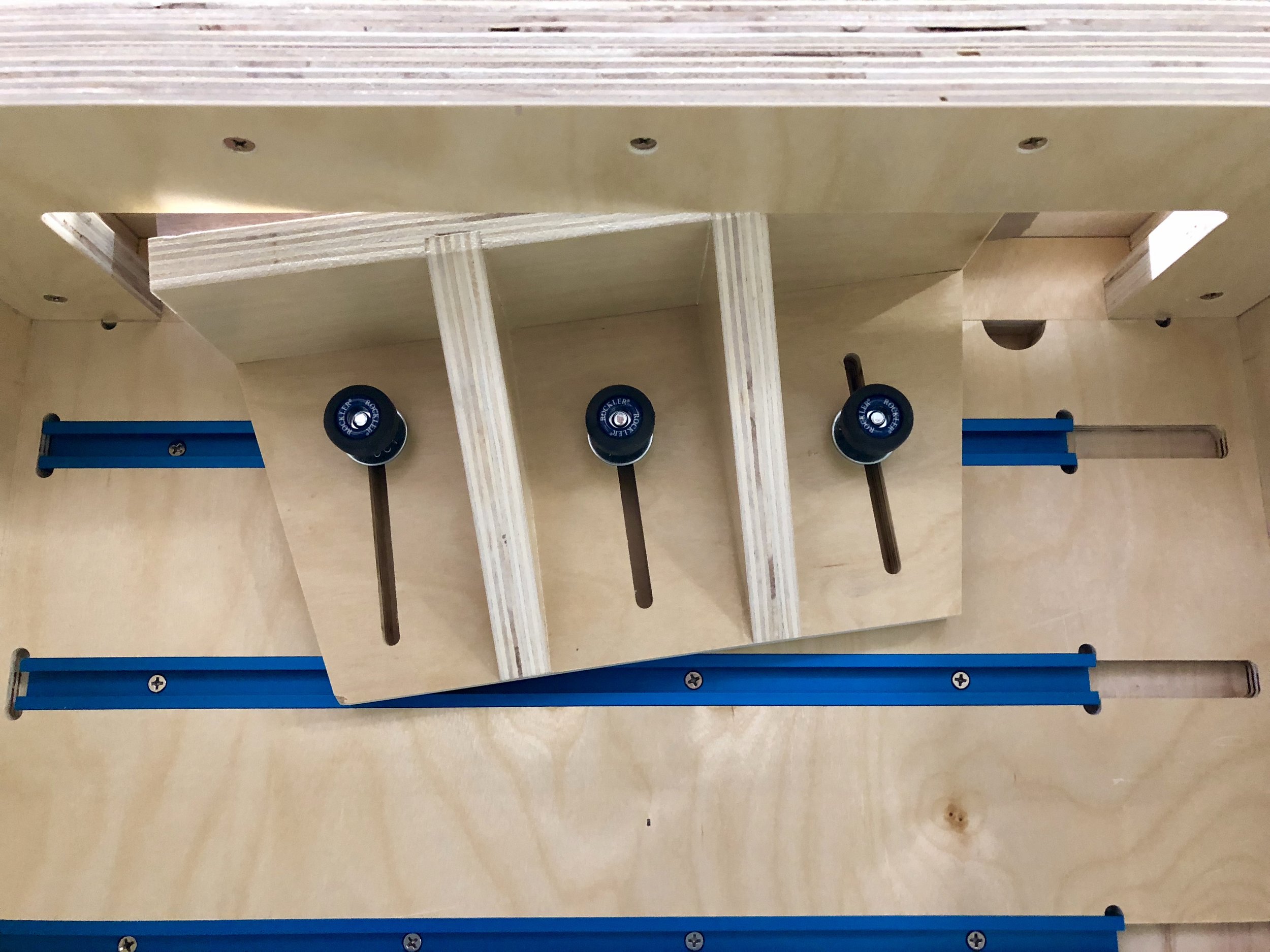
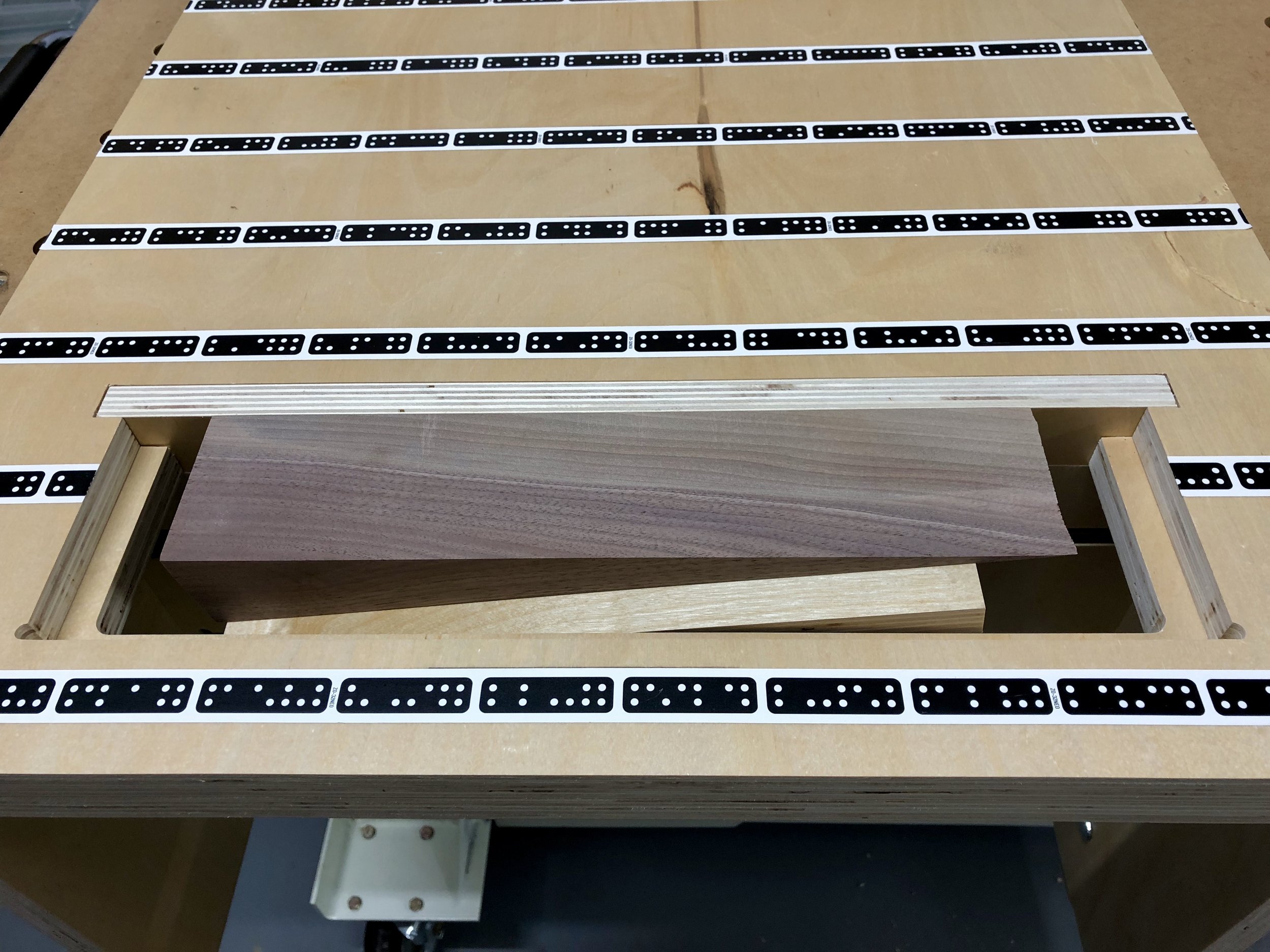
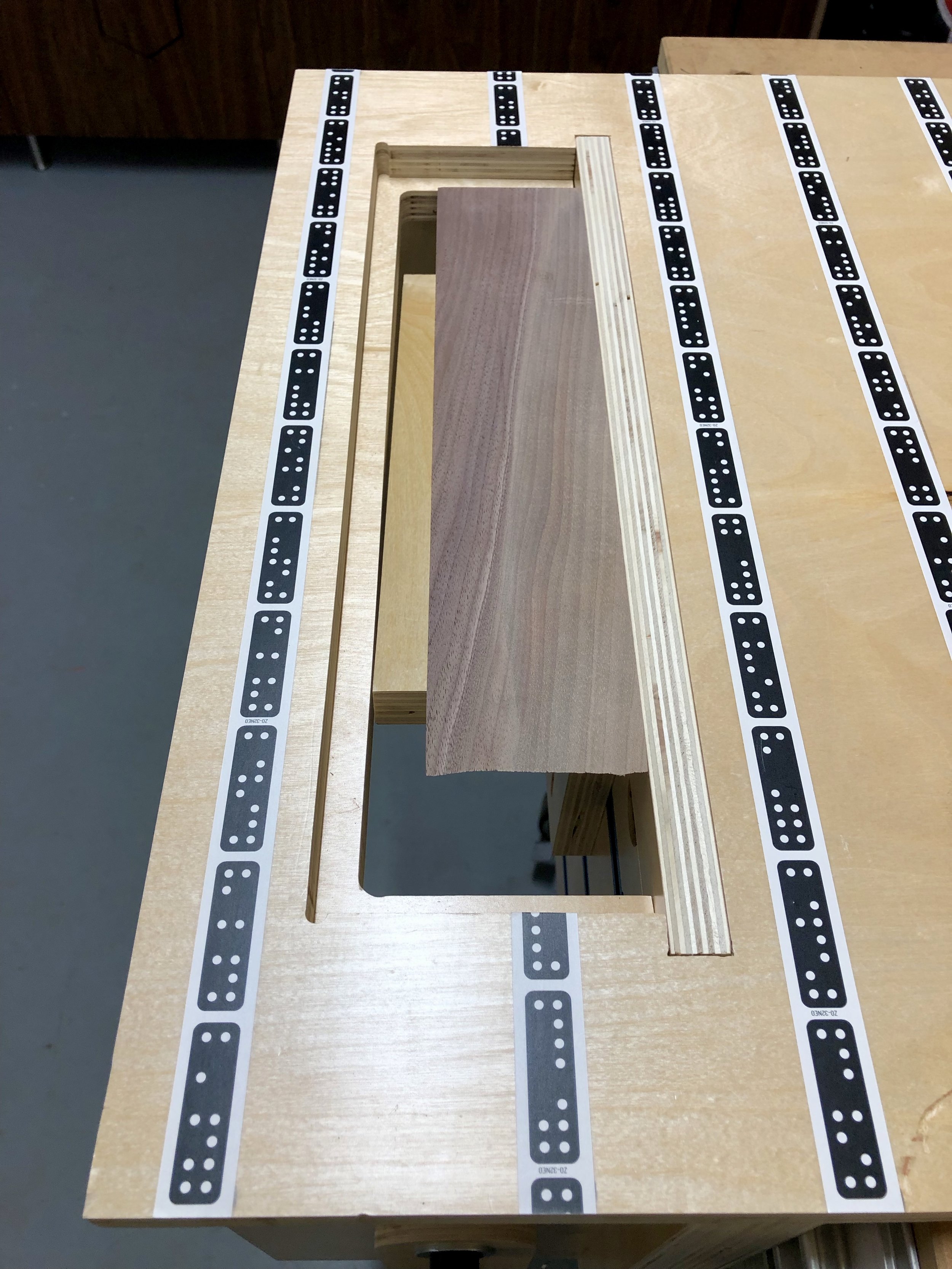
Now the work piece is level with the UVW top. You should be able to set the Z-axis on either the surface of the UVW or the work piece.
When you’re finished using the HS it stows away nicely on the side and remains there when hanging the UVW back on the french cleat wall.
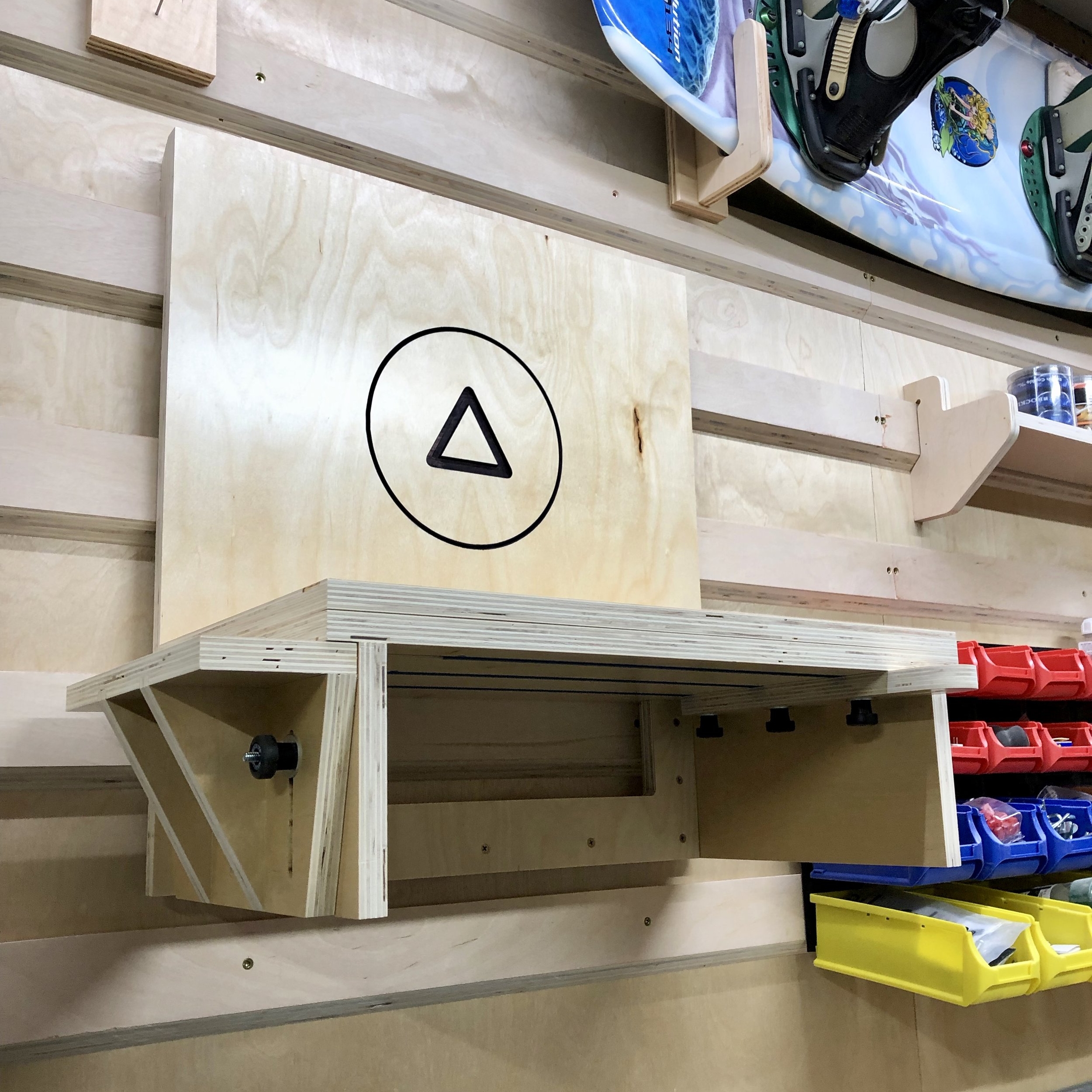

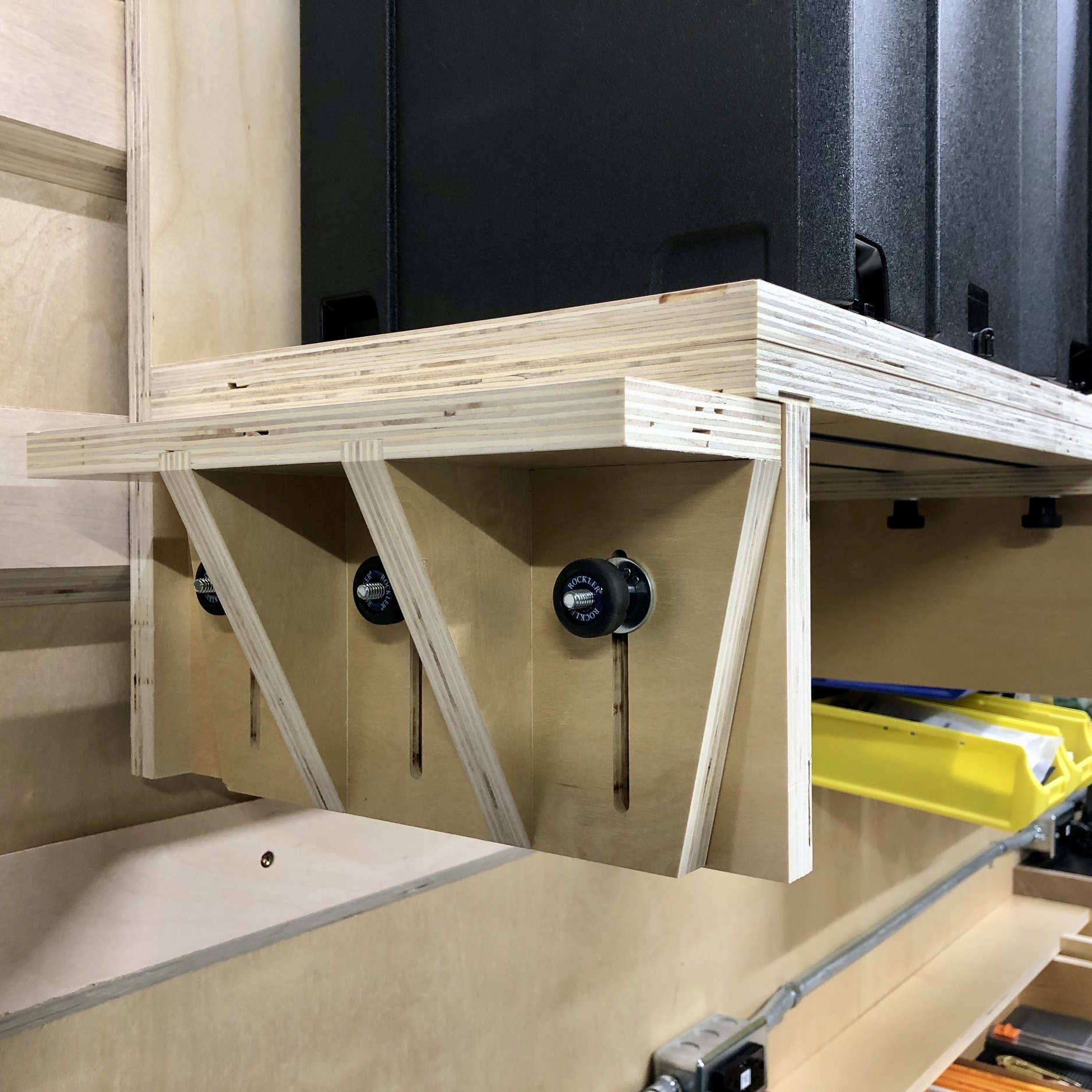
Here are some pics of the HODOR doorstop being completed…
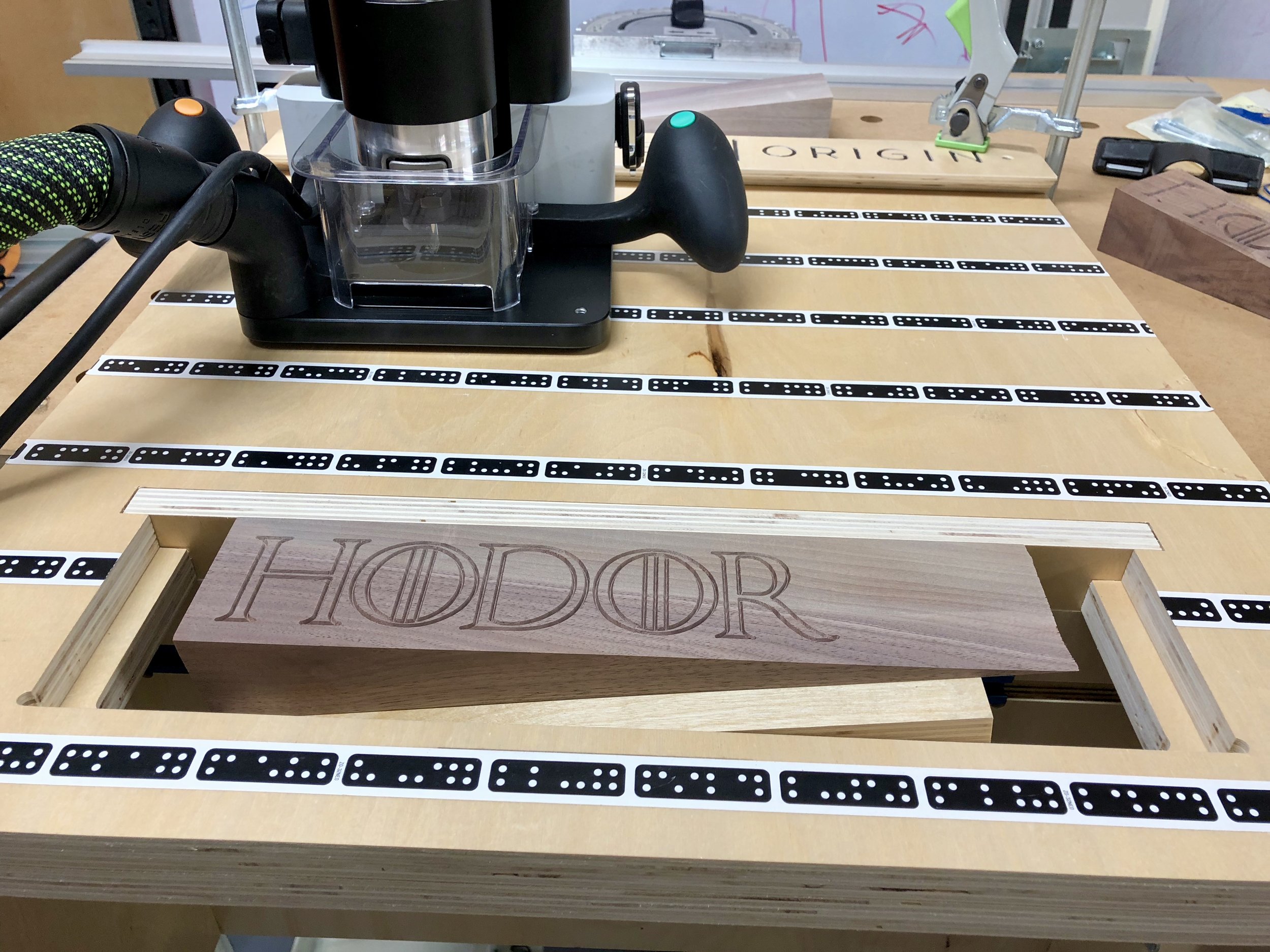
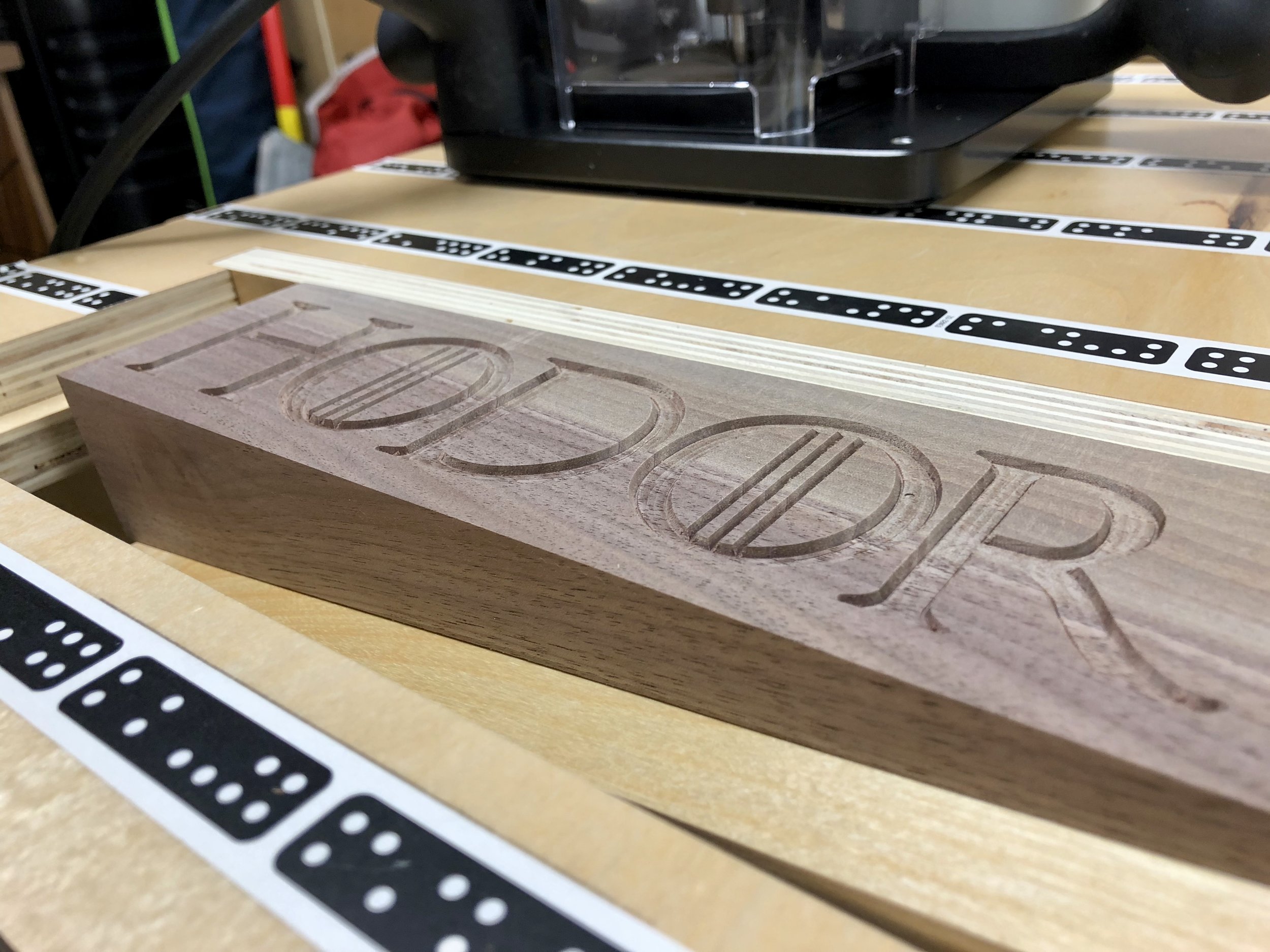
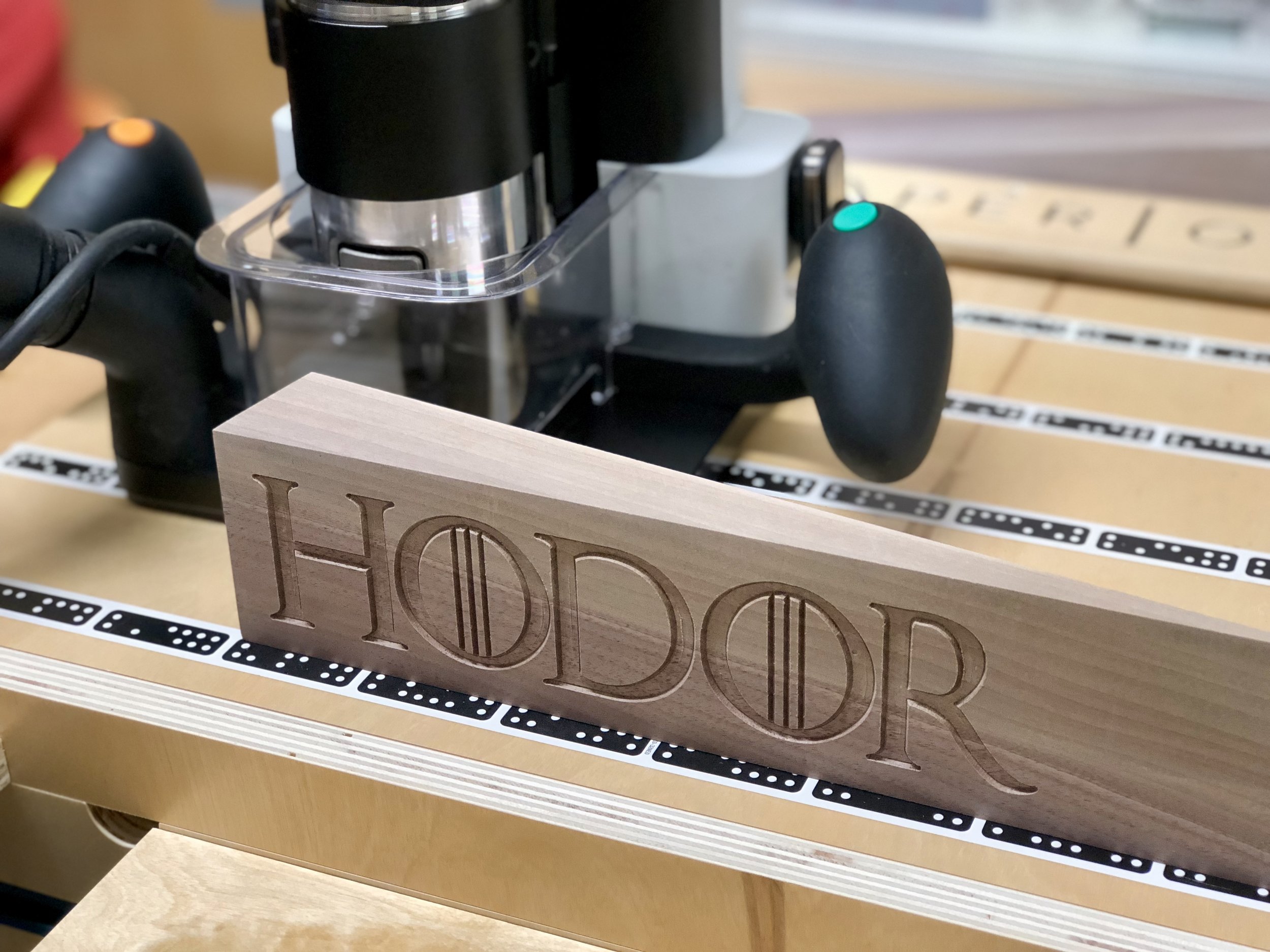
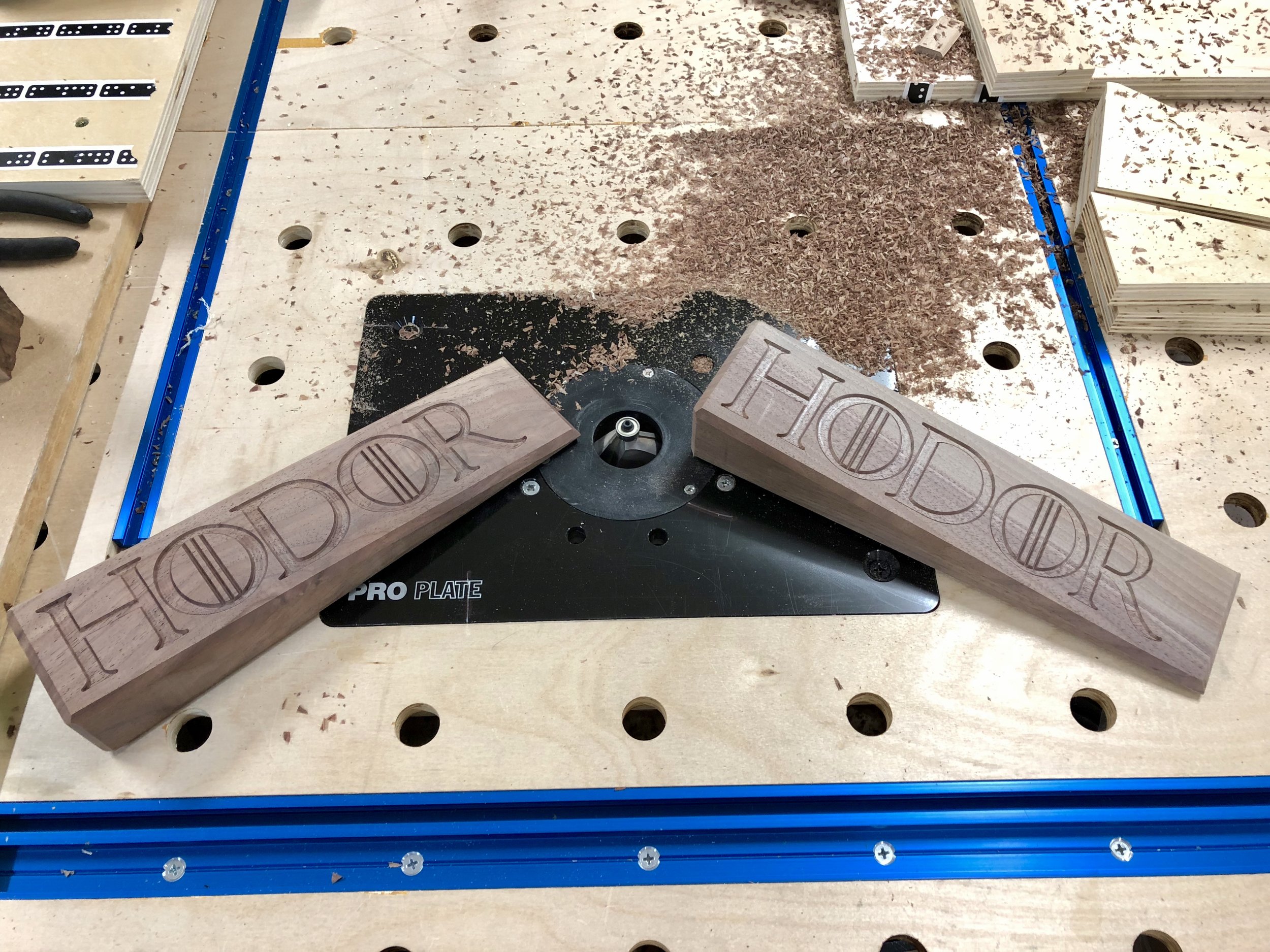
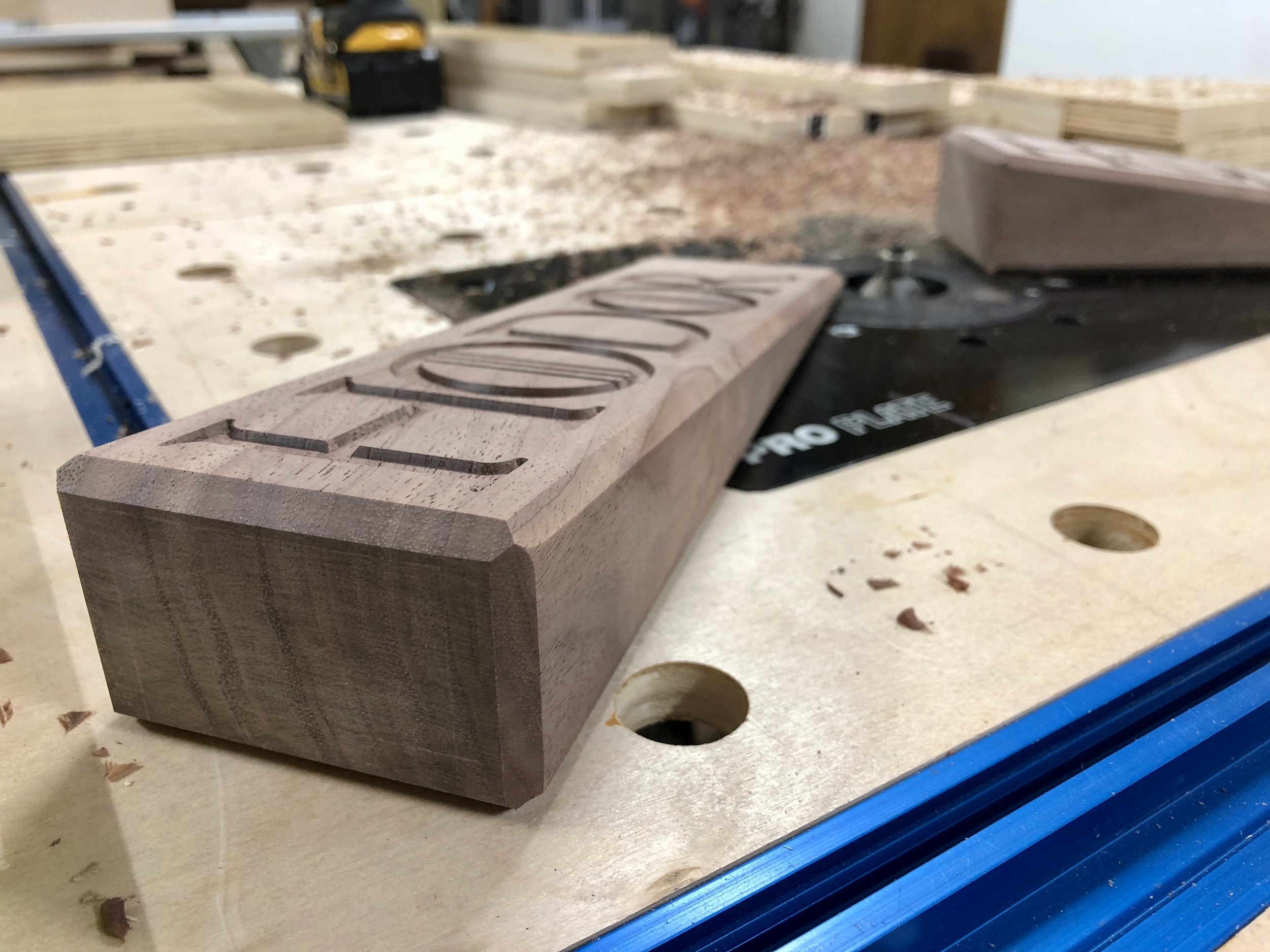
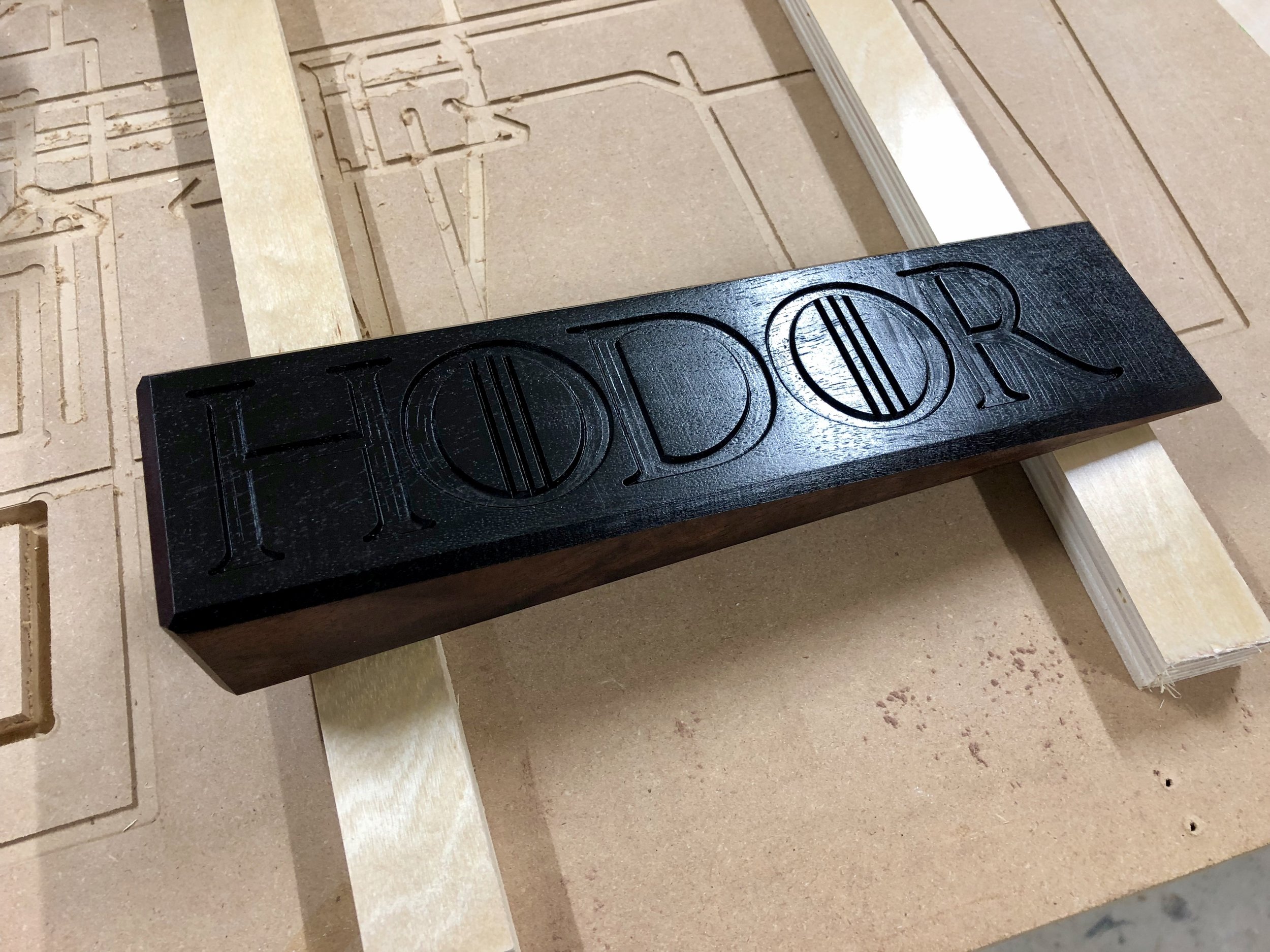
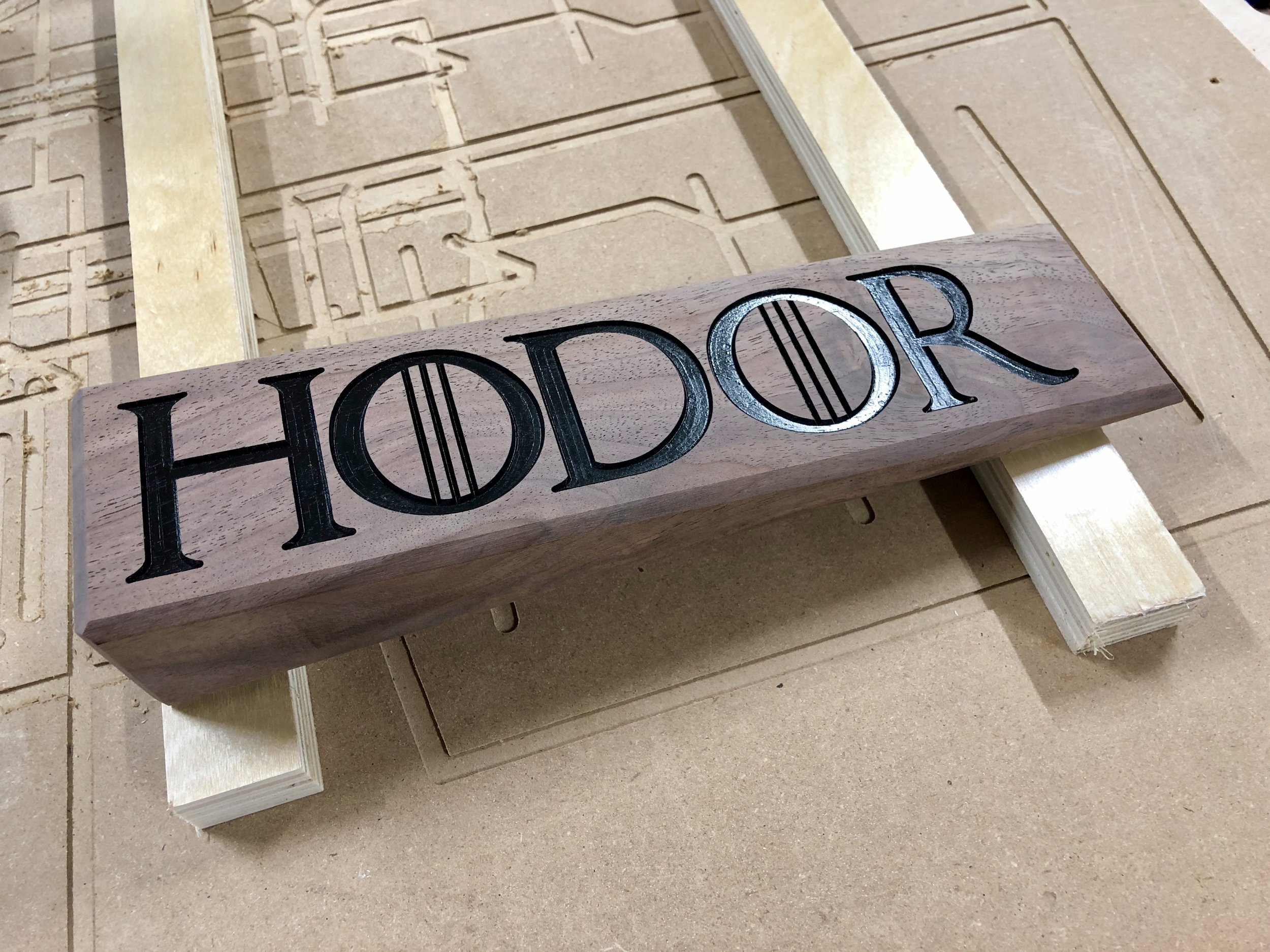
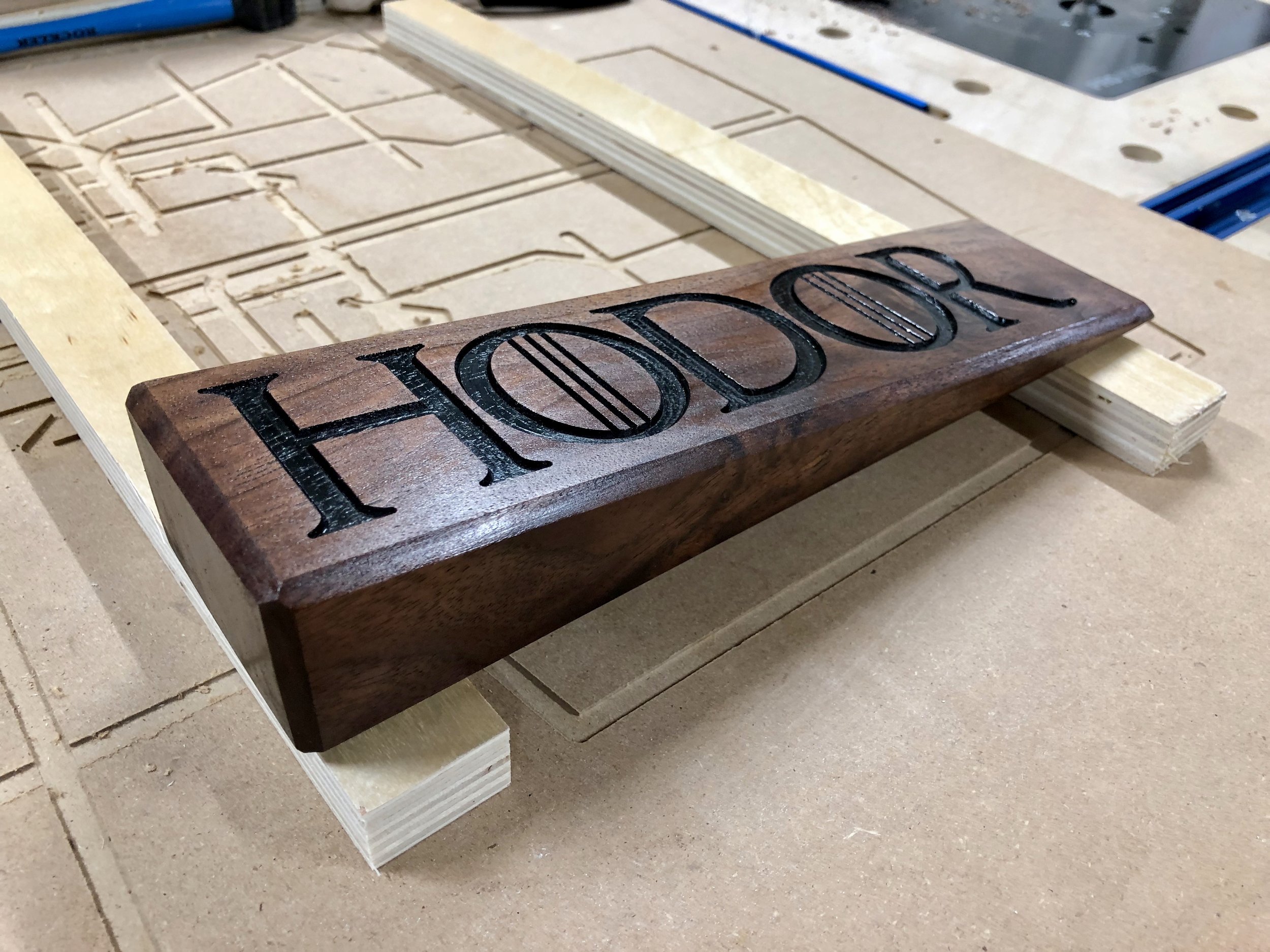
Other Uses
Using different thickness of material
I’ve always found it difficult to get another board with Shaper Tape on it at the same plane as the work piece when using different thickness of materials (even 3/4” plywood has slightly different thicknesses based on the type and source of the material). The HS supports ANY thickness of material that fits within the opening (121mm H x 406mm W, with optional Support for Filler Pieces removed). Simply adjust the height so the two surfaces are level and you’re golden. You can even mount a sacrificial piece of MDF on top of the HS before mounting the work piece so you don’t have to cut into the HS.
Use it as a Vertical Support
I have set the width of the slots to match the distance between the t-tracks so you can mount the HS vertically. This gives you a much larger support as well as something that you can clamp to.
I’m sure all of you can figure out even more uses. Post in the Comments if you do.
Anyway, I hope this is helpful for making your next project or Xmas gift.
Cheers!
Lee
Tools and Materials used
"Ultimate" Vertical Workstation for Shaper Origin
For those who have read my "Turning a Wood Mallet..." post last week, I used the Shaper Origin to engrave our logo into the end of the mallet. I did this by using the Origin to cut out a precise hole in MDF that could hold the mallet snugly and flush with the top surface. This worked great for a one-off but if I want to make more (hint, hint, keep an eye out in the Store sometime soon) it might be a bit difficult and time consuming to keep using that method since every mallet would be a slightly different diameter.
Which brings me to the project this post is about. I've been eyeing one of the Shaper projects on ShaperHub for a while now and the Vertical Workstation would be perfect for doing this sort of end-grain engraving work. I just needed to "tweak" a few measurements to make it work for this particular application.
Ideally it would have been great to simply open up Fusion360, make a 3D model of exactly what I wanted and then export the .svg files to cut the parts out. All the tolerances would have been tight and everything would have fit together snugly. However, I'm still ramping up on Fusion360 and finishing up an online training course so I didn't feel confident in doing that. So I decided to go the "quick" route by editing the .svg file Shaper provided with Adobe Illustrator. Unfortunately, things didn't go to plan.
Tabs in the Top
Tabs on the first build
Shaper did say on the second page of their instructions that the 3/4" material thickness the project files were designed for was .73in (18.542mm). I did a test cut of one of the tab holes and my pre-finished birch ply (17.85mm) was pretty loose so I "offset" the cuts to compensate. Needless to say it was a botched job. Things were super tight in some places and sticking out in others. Which then made me evaluate the design a bit. Since the top of the workstation, where the Origin slides around, needs to be completely flat and smooth, I didn't understand why you would want tabs from other pieces sticking through it. I did try to block plane and hand chisel the tabs flat but since I was using pre-finished ply, it basically ruined the finish. (I was using pre-finished ply because I had a leftover sheet from some cabinets I made)
Long, Straight Cuts
So the next thing I began to question was the method for cutting the long, straight edges of some of the panels. No offense, and I'm sure Shaper would agree that the Origin is not the tool of choice for a perfectly long straight cut. Of course it would be the Festool track saw! However, now I'm faced with a new problem: how to use Origin for the pocketing and curved cuts and then use the track saw for the straight cuts while still keeping everything precisely aligned. I decided to use the Origin first, make all of the pocket and curve cuts then use it to make 1/8" deep by 1" long cuts at the beginning and end of each straight cut that I would use as a reference with the track saw. I'll say it worked but the jury is still out on whether I'll do it that way again. I think next time I'll try cutting all of the straight pieces out, create a unique .svg file for each part and then use the grid functionality on the Origin to align the file to the edge of the work piece.
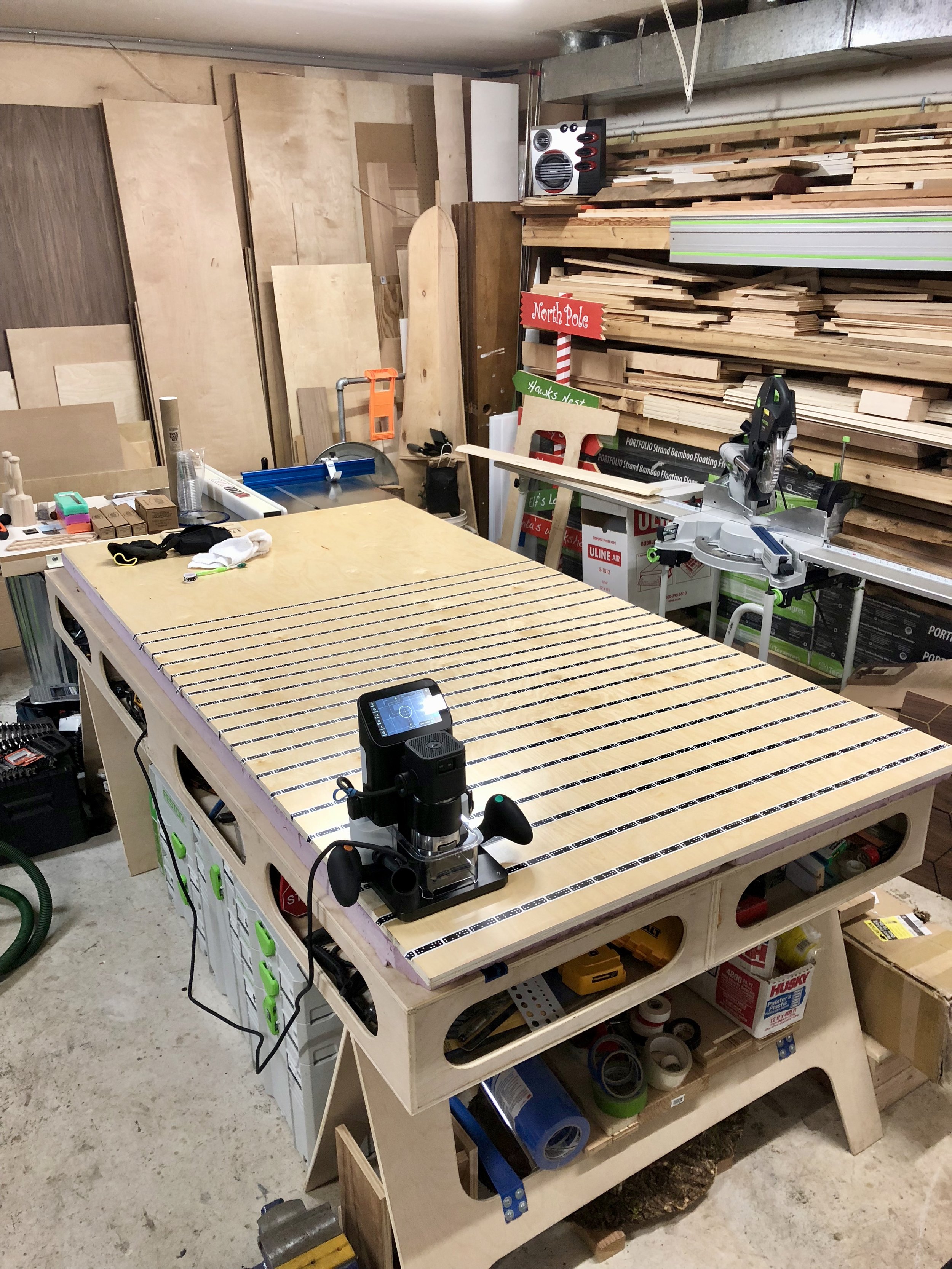
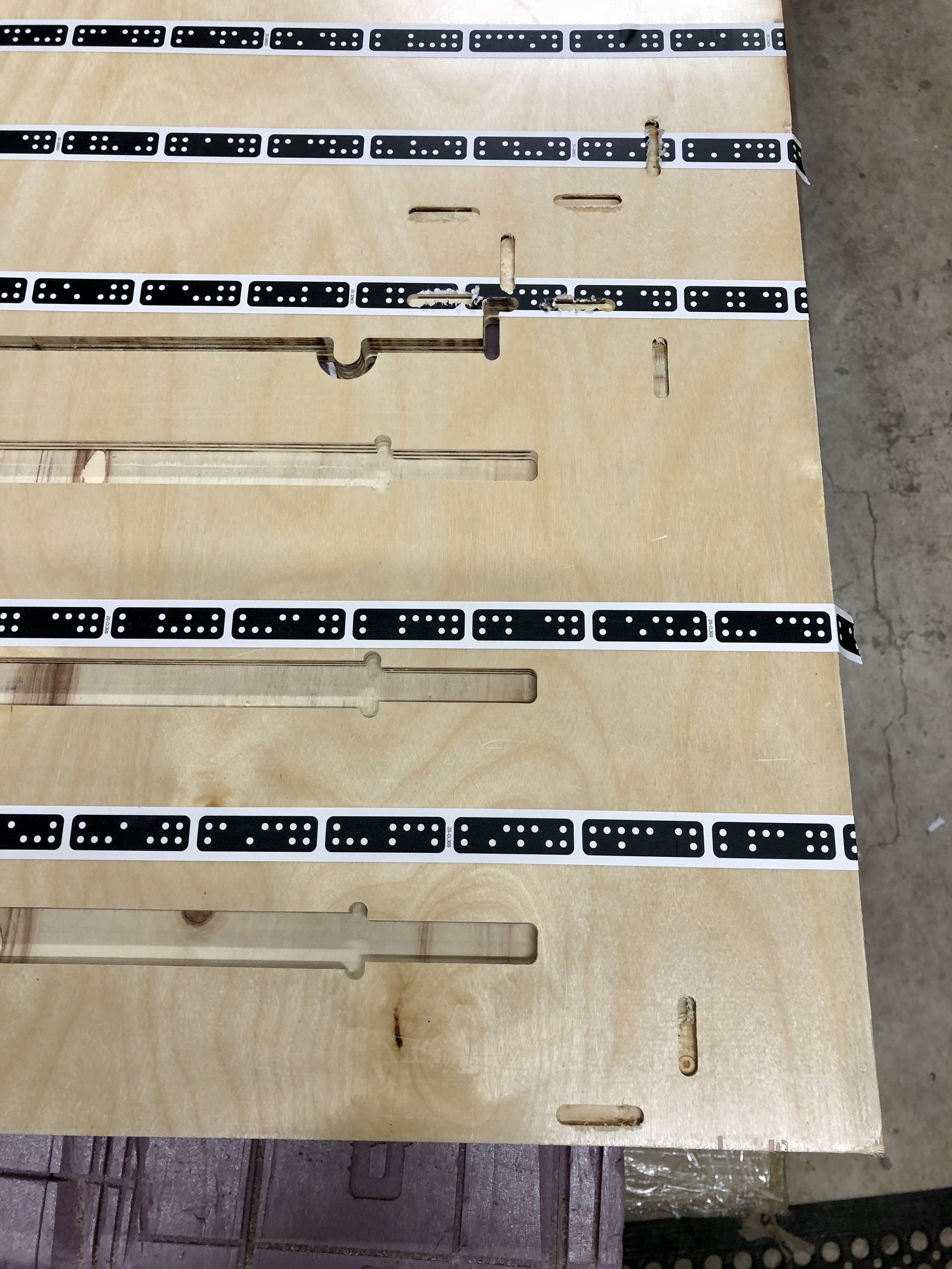
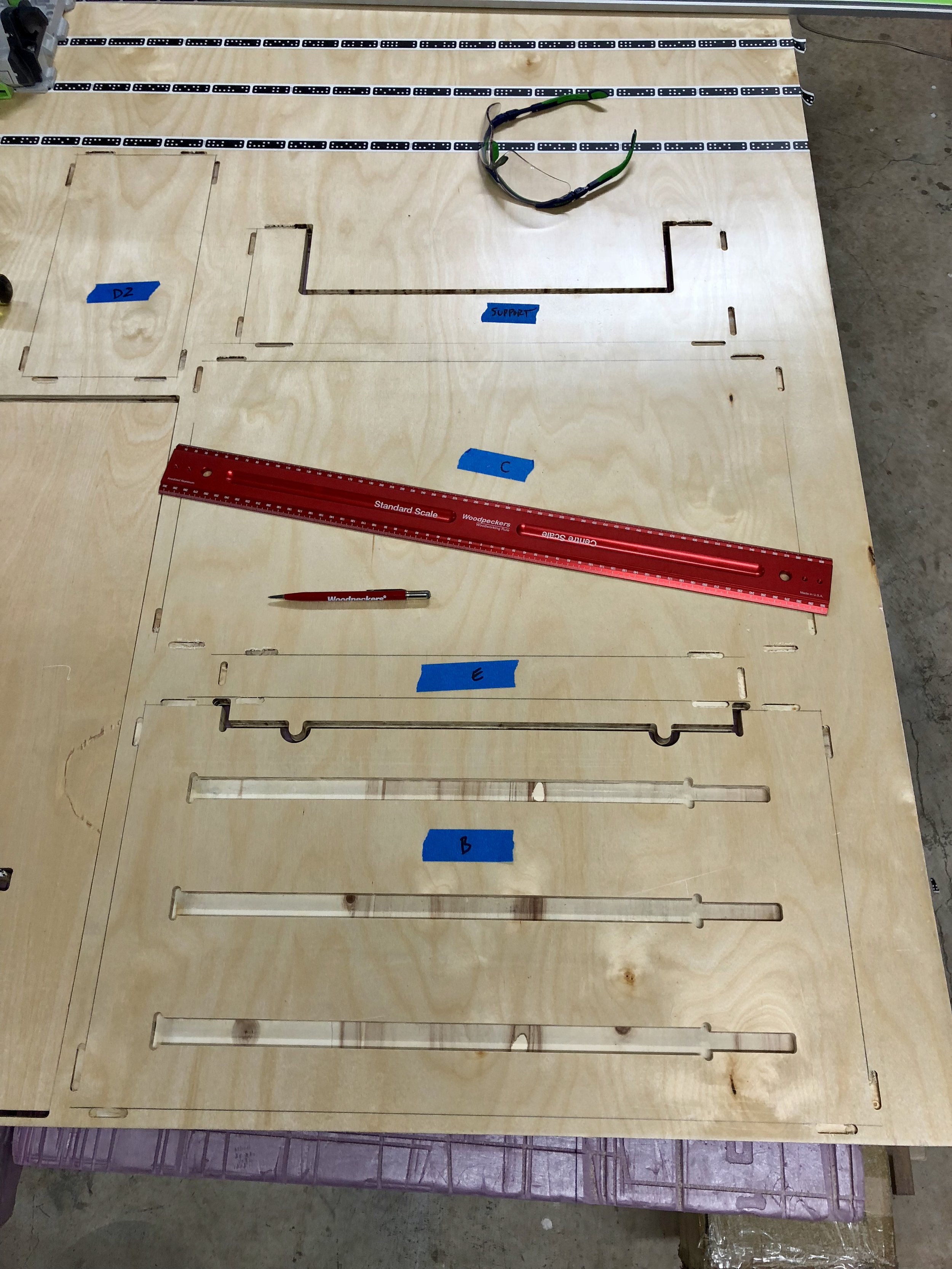
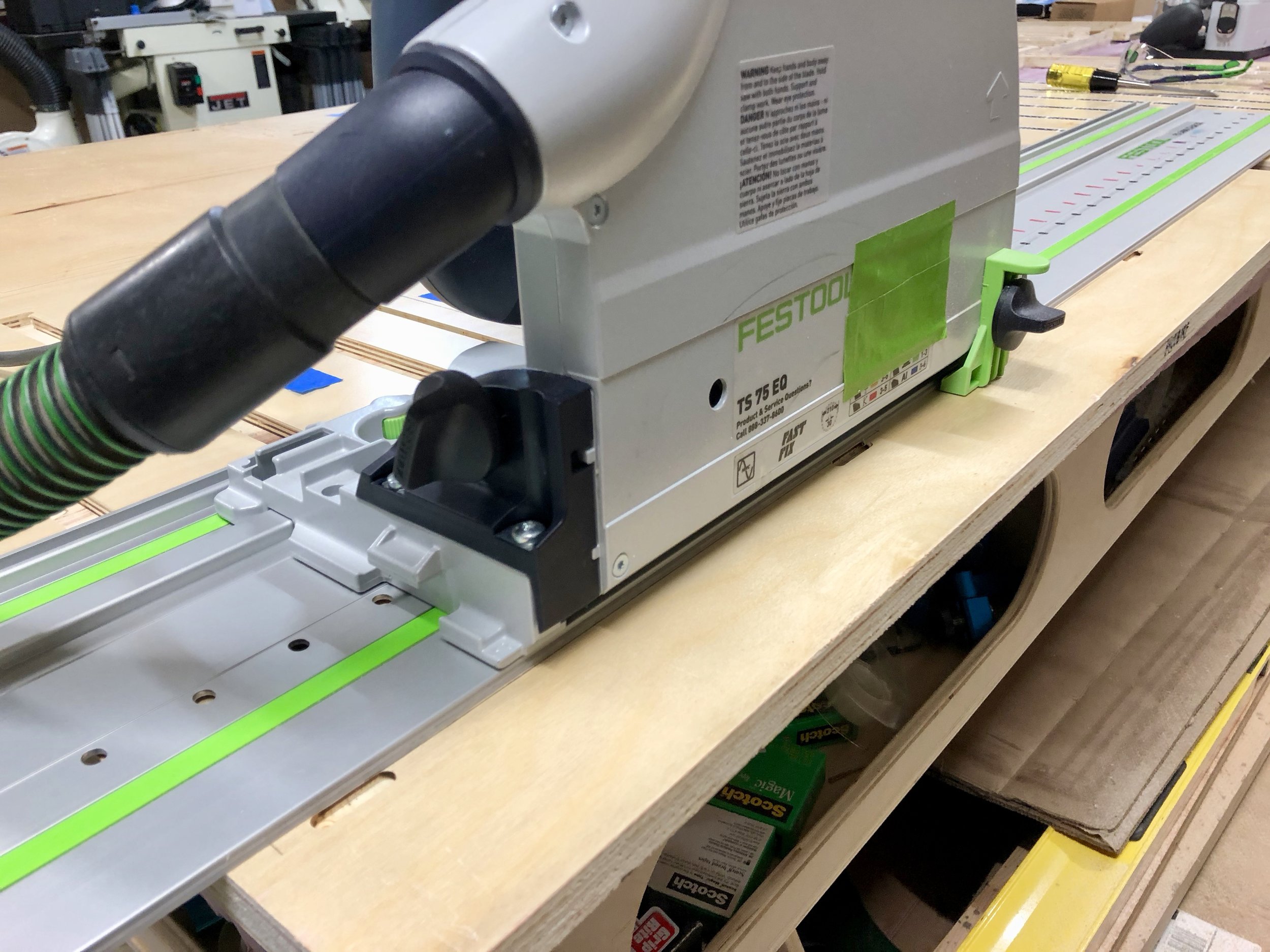
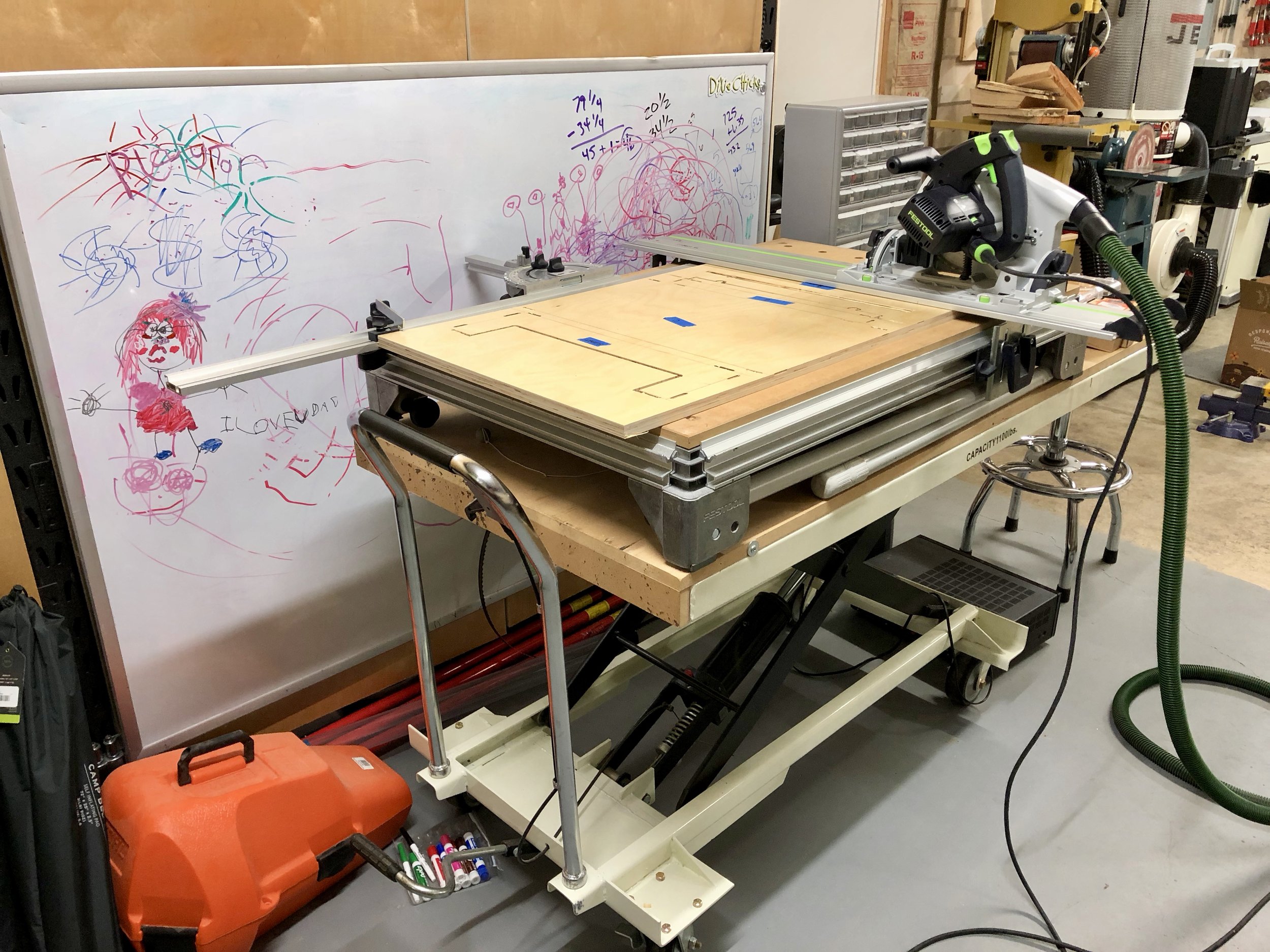
Tabs or Dominoes
Well since I'm not using tabs through the top piece and I'm going to use the track saw to make the straight cuts I might as well use Dominoes for joining the pieces together. It made the most sense and completely eliminated the issues with making a bunch of small modifications to the .svg file to compensate for the different thickness of material. Don't get me wrong, I still want to perfect the process of using tabs. I love the idea of having the parts just lock together right after being cut. But for now this was the better option.
Two for One
When I was playing around with the dimensions so that I could engrave on the mallets, I realized that I could also increase the depth of the top and the height of the vertical support piece (where the t-tracks are) so that I could use it as a shelf as well! Two functions in one project, bonus! I always wondered where I was going to keep the workstation when I wasn't using it so this solved that problem. It was also structurally perfect to be used as a shelf. All I needed to do was add a french cleat at the top. It doesn't interfere with the Origin or the marker tape either because of the increased depth of the top.
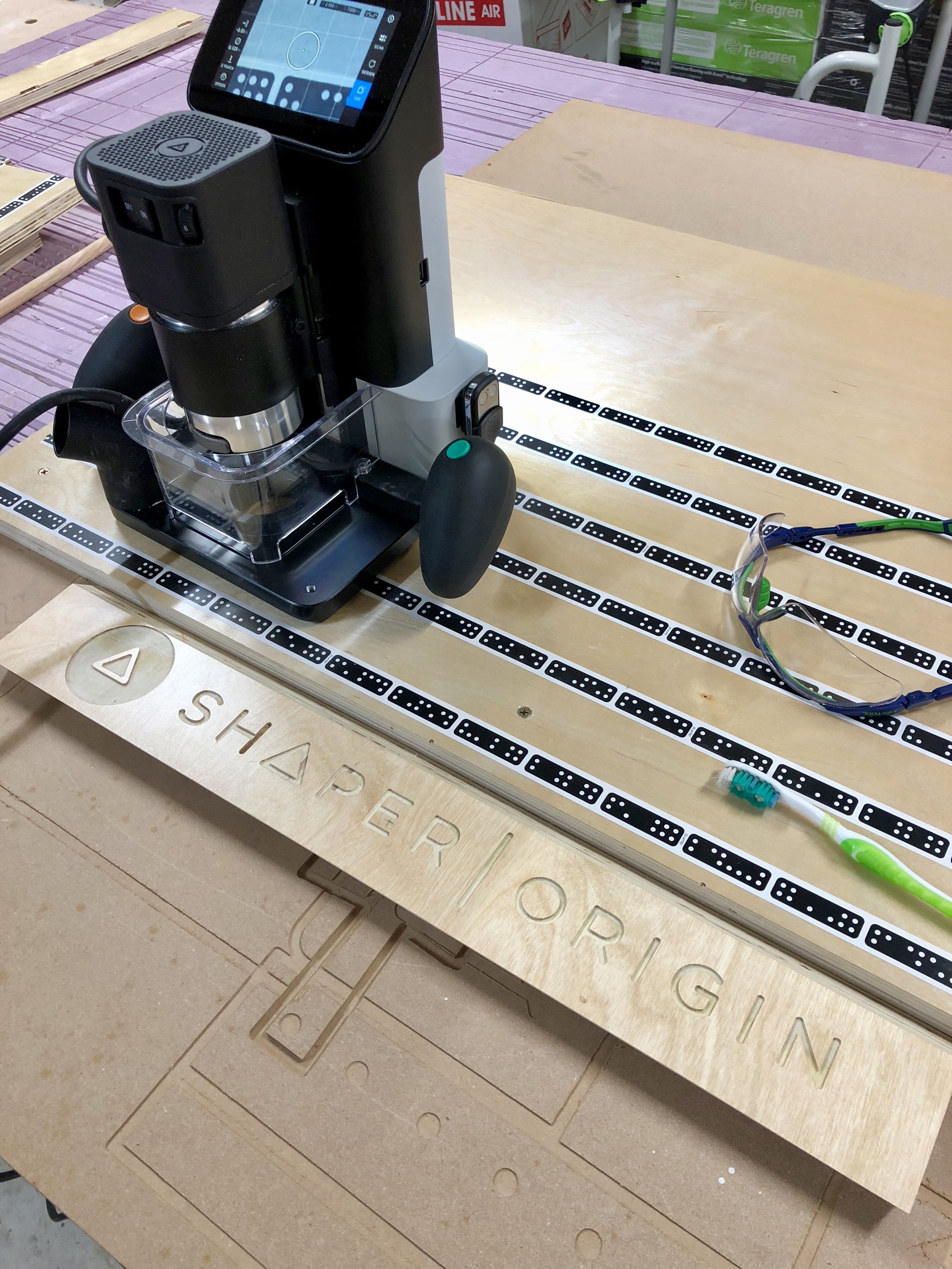
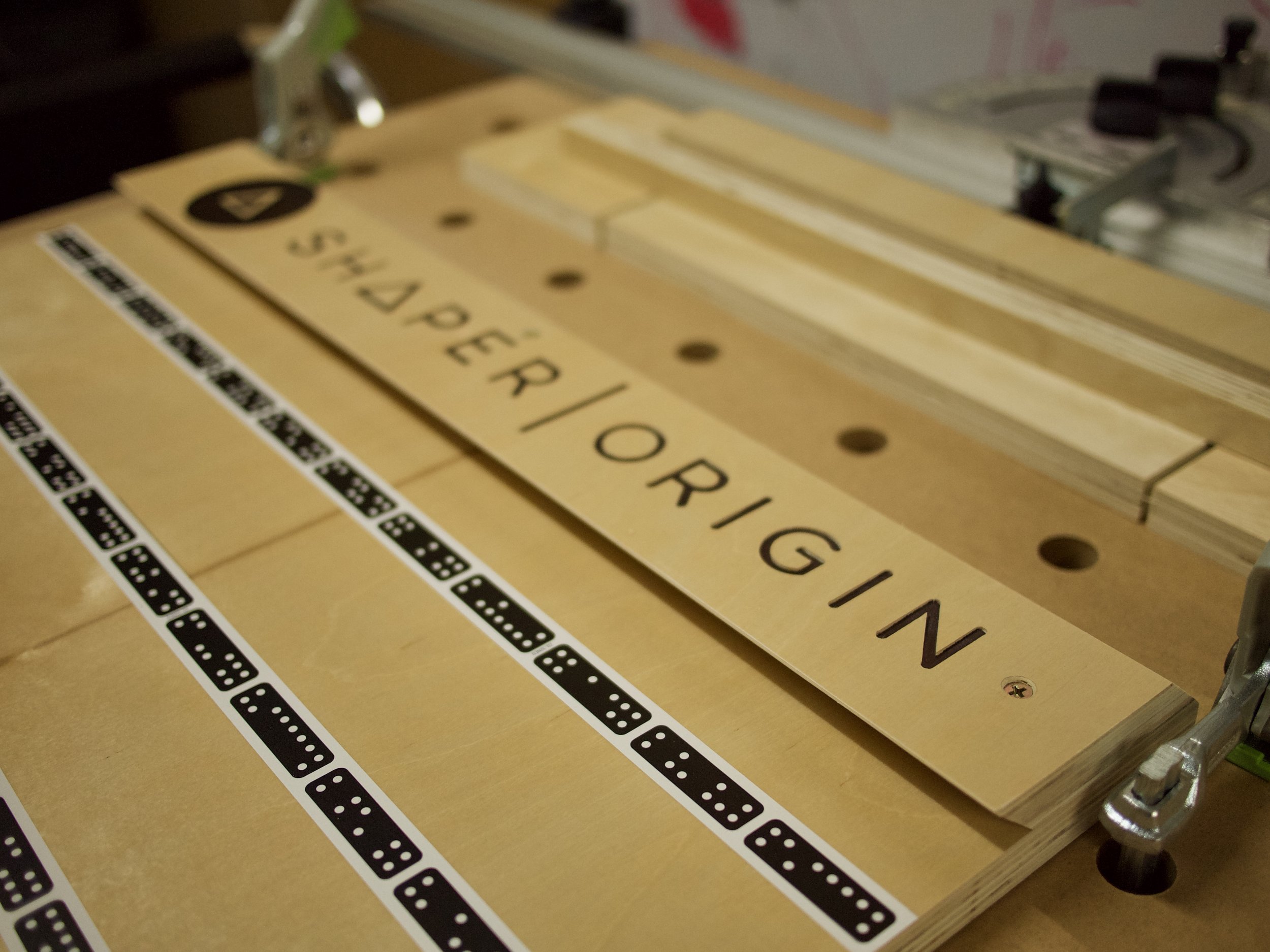
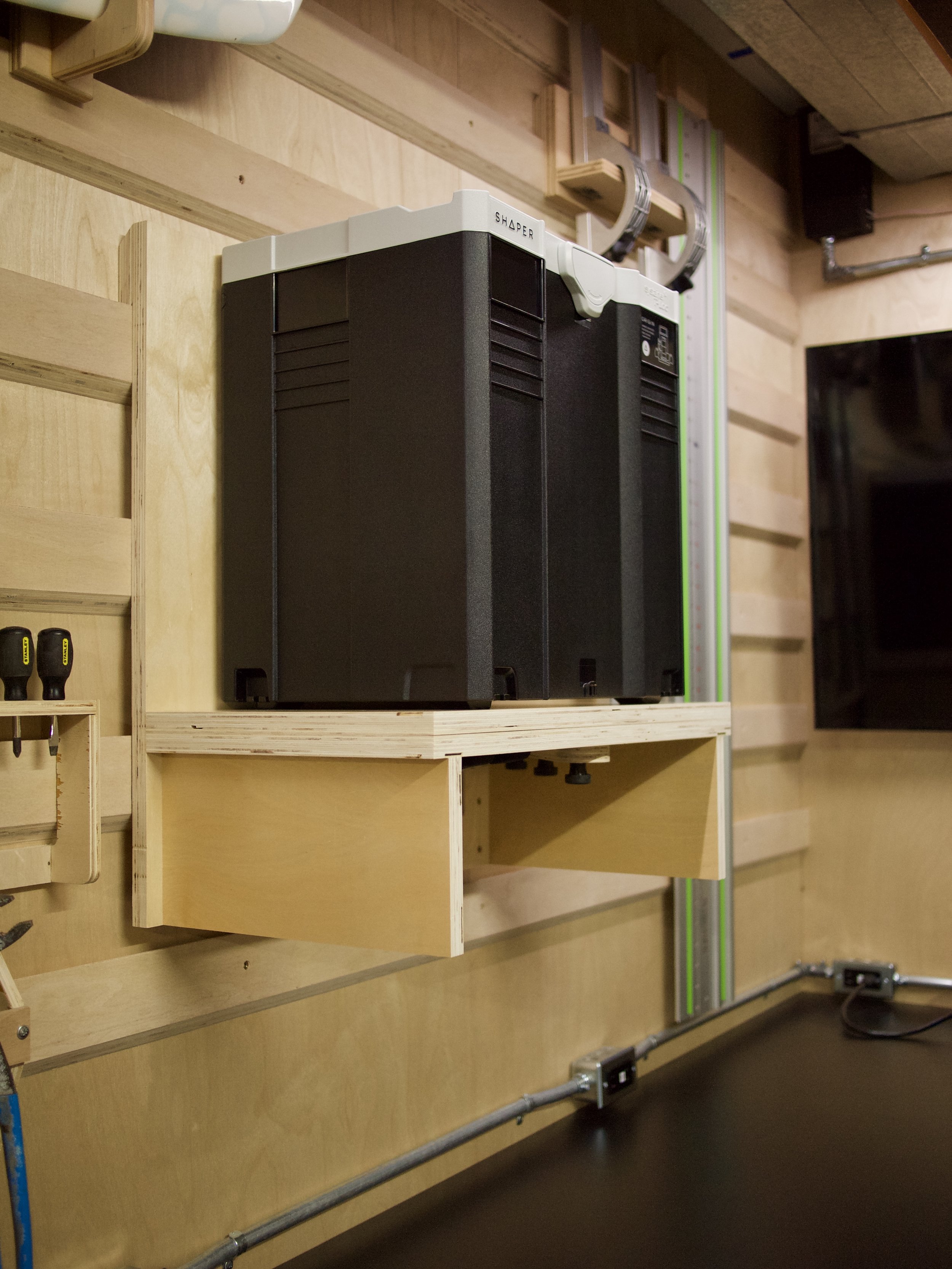
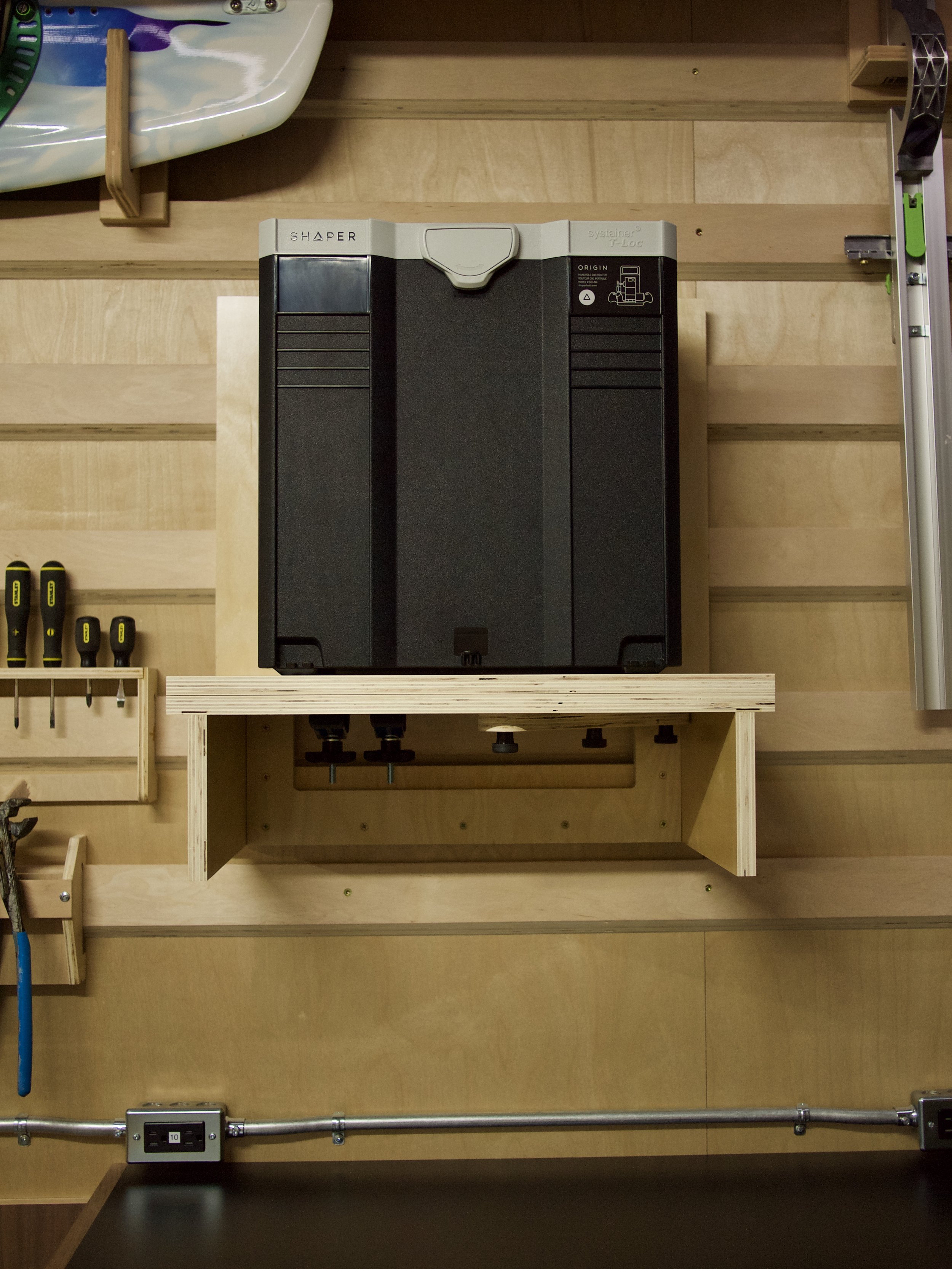
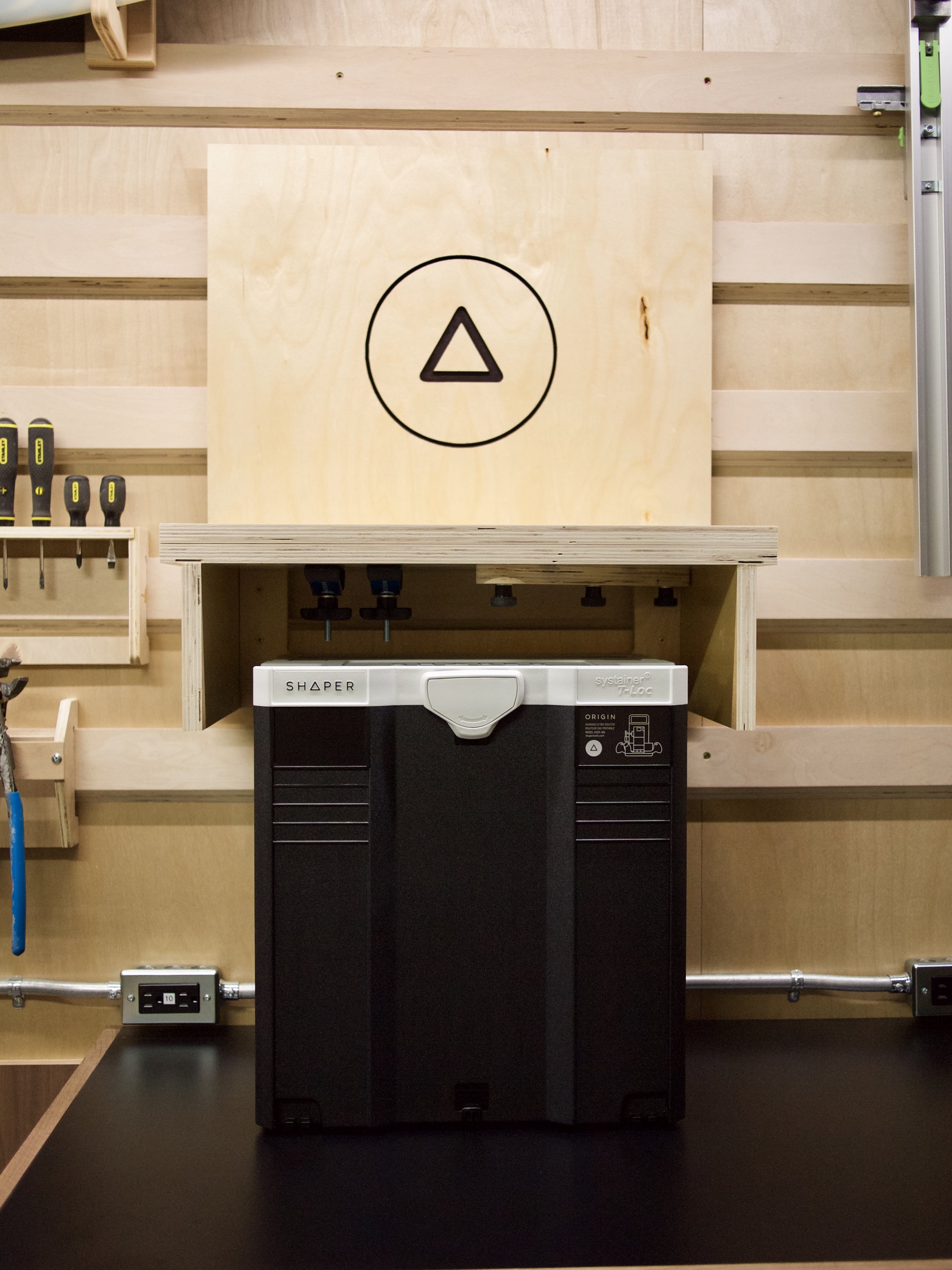
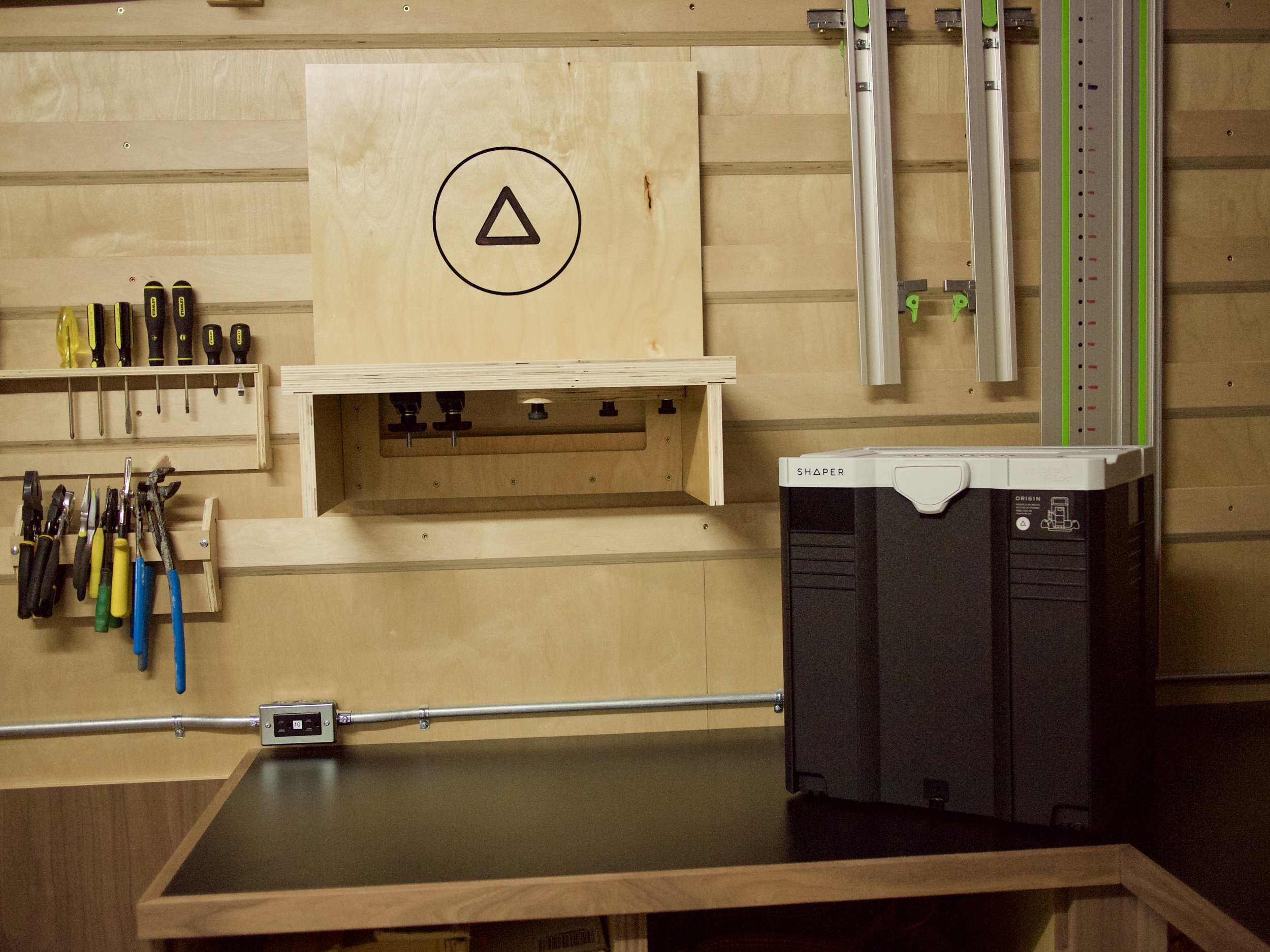
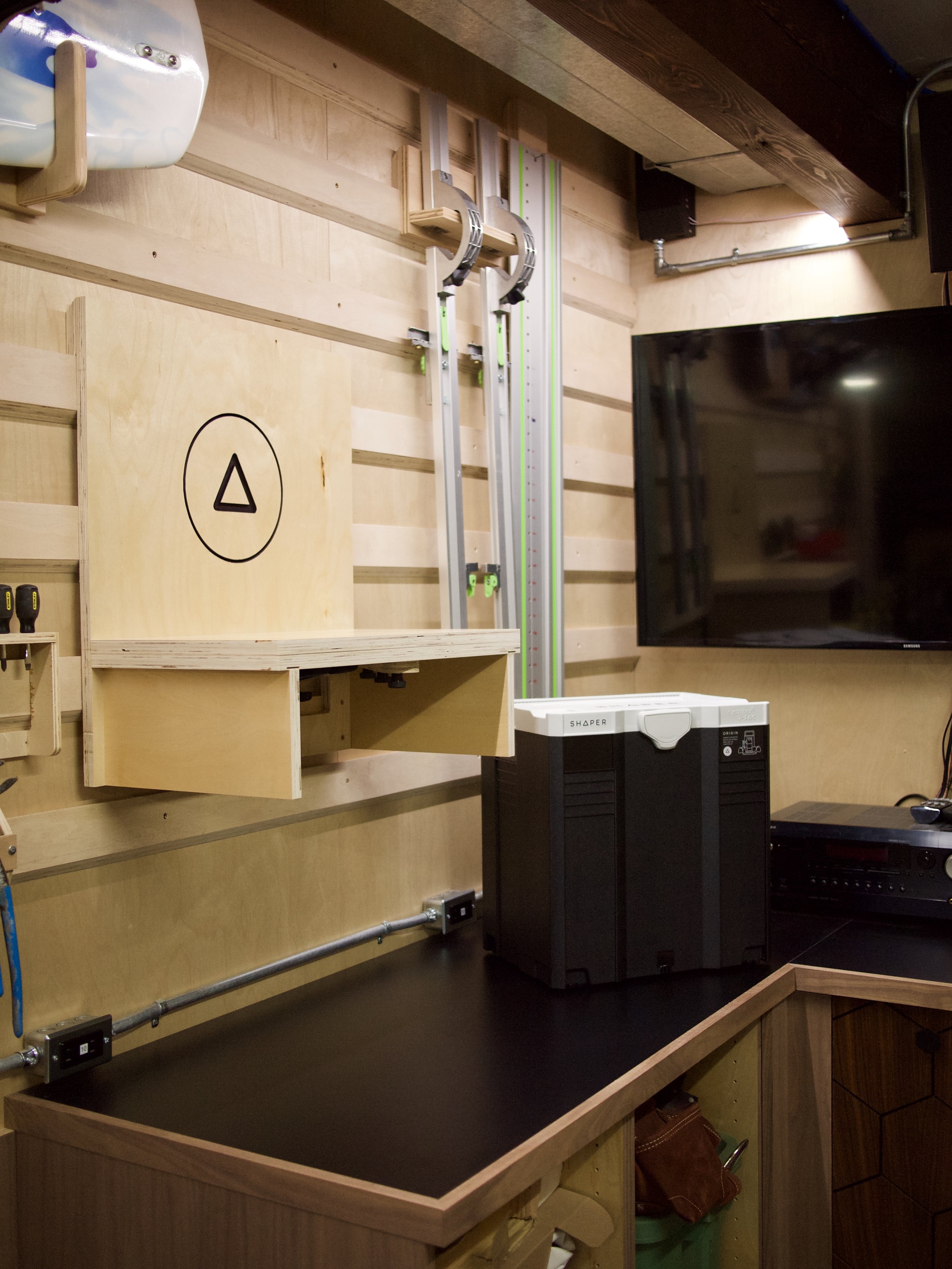
Mind the Gap
Another good thing that came from the first build is that I noticed that the Origin was unsupported in certain positions because of the size of the opening. I decided to add a 1/2" support underneath the opening so that I could use various filler pieces for additional support. I'm also thinking that I might add bolts or something to the outside of each side to store the filler pieces when they are not being used.
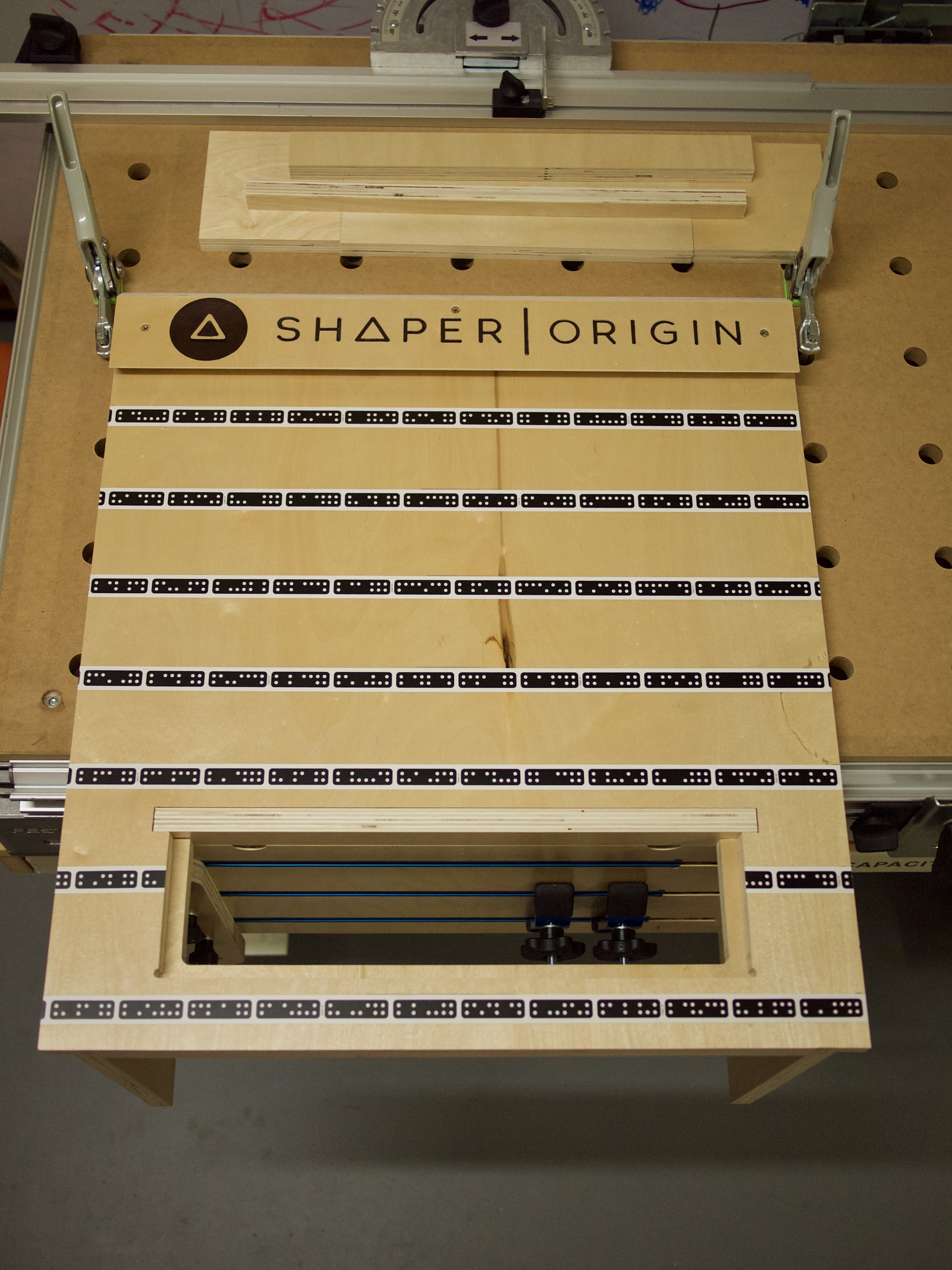
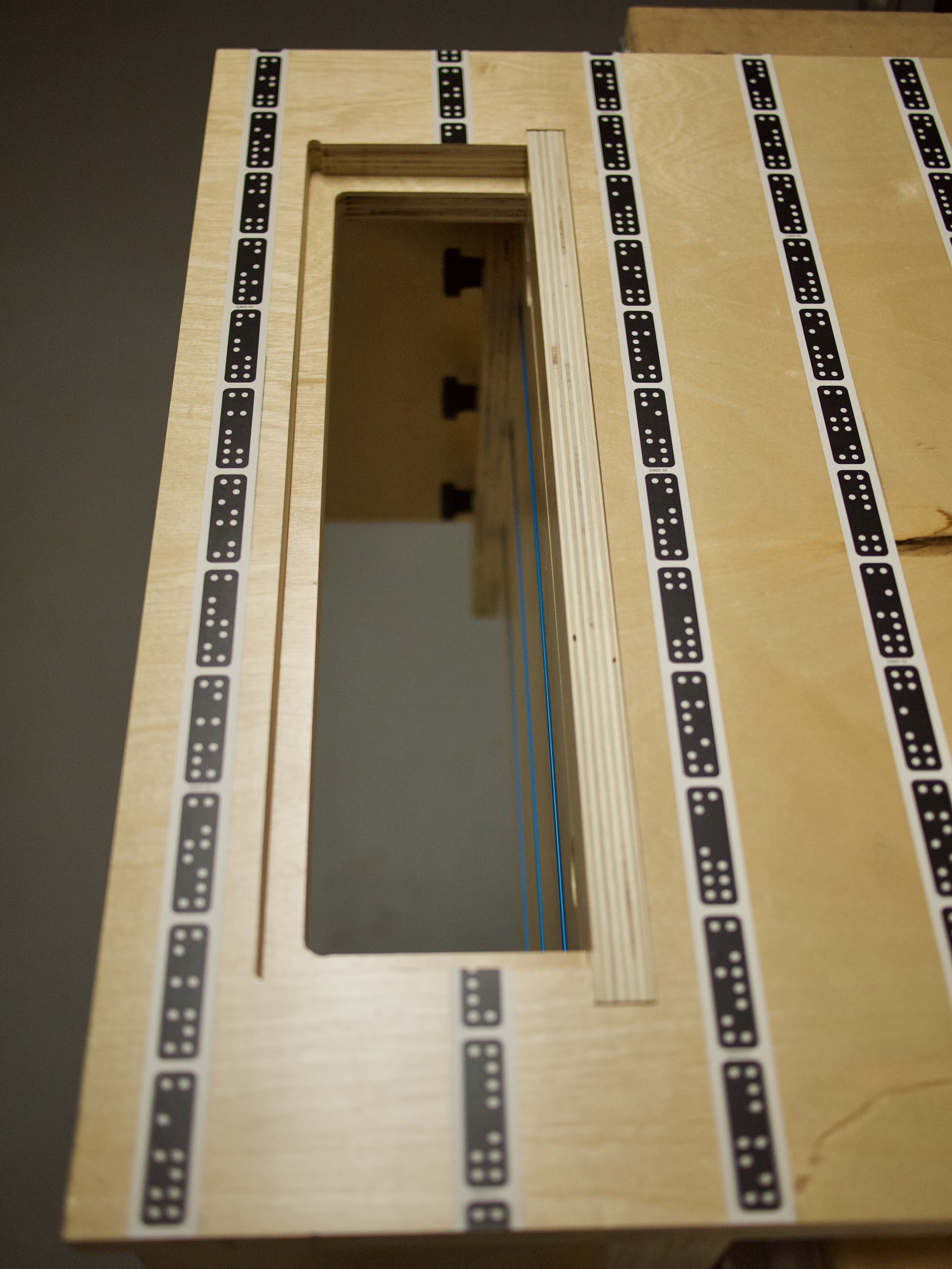
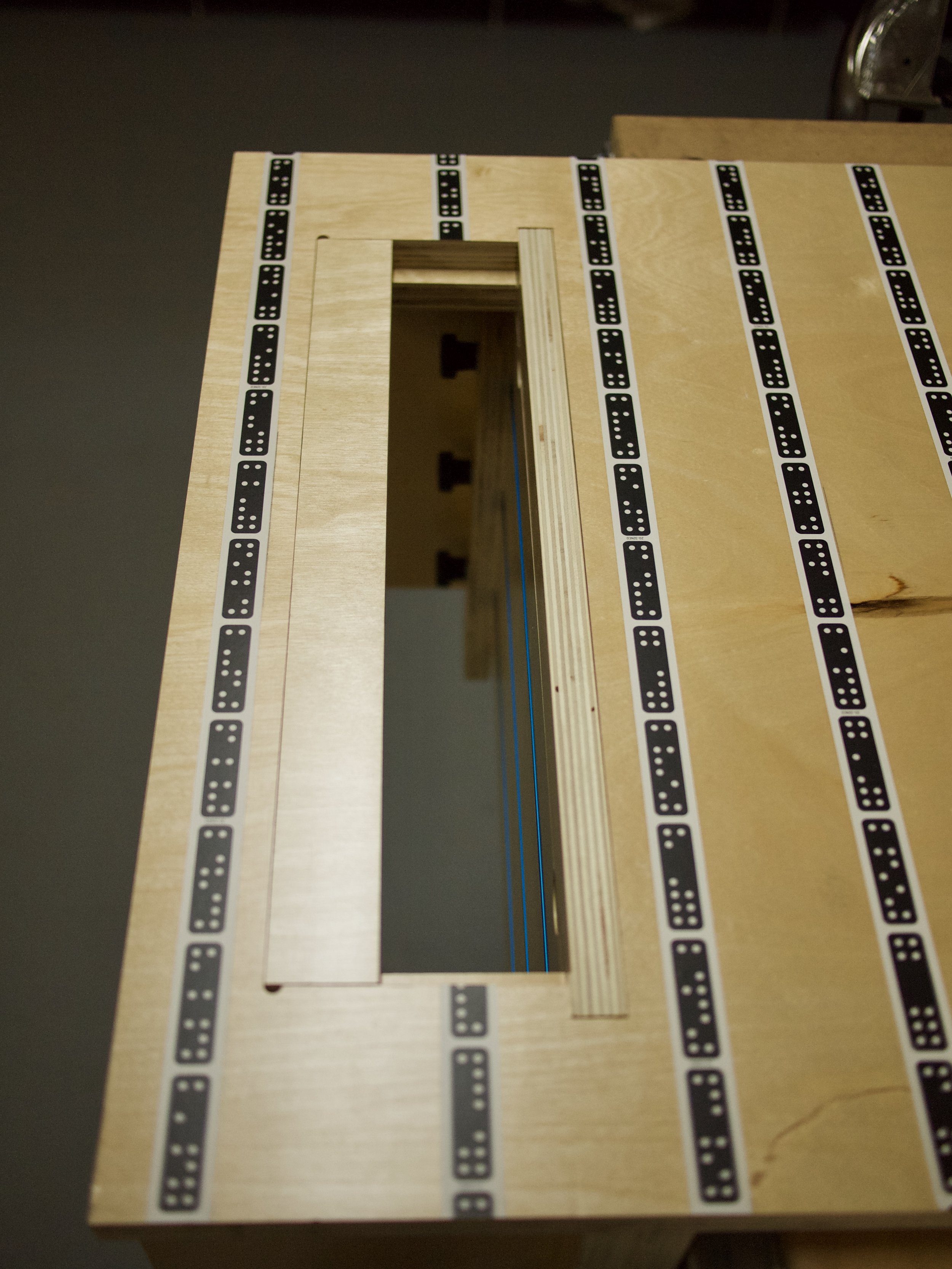

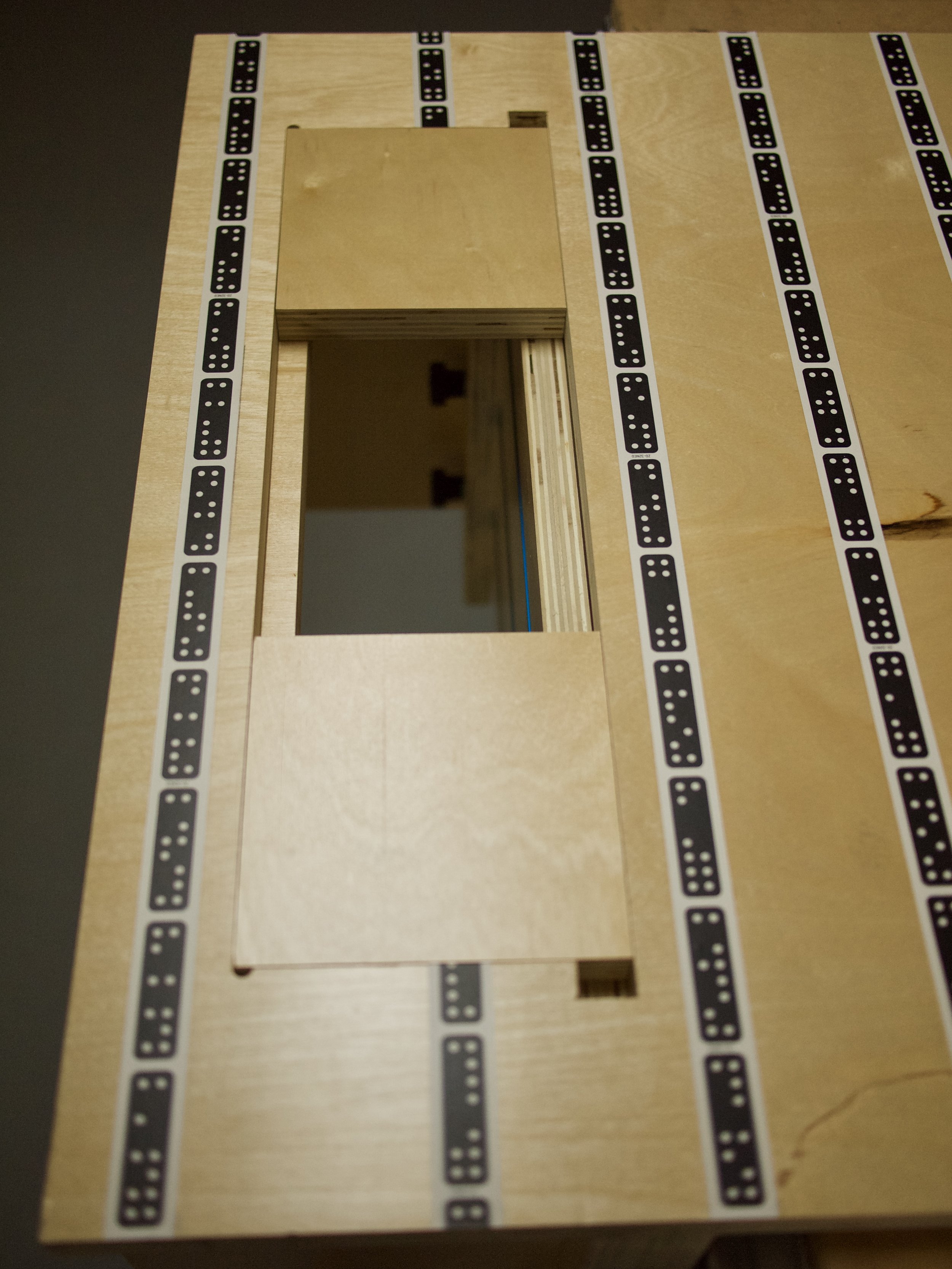
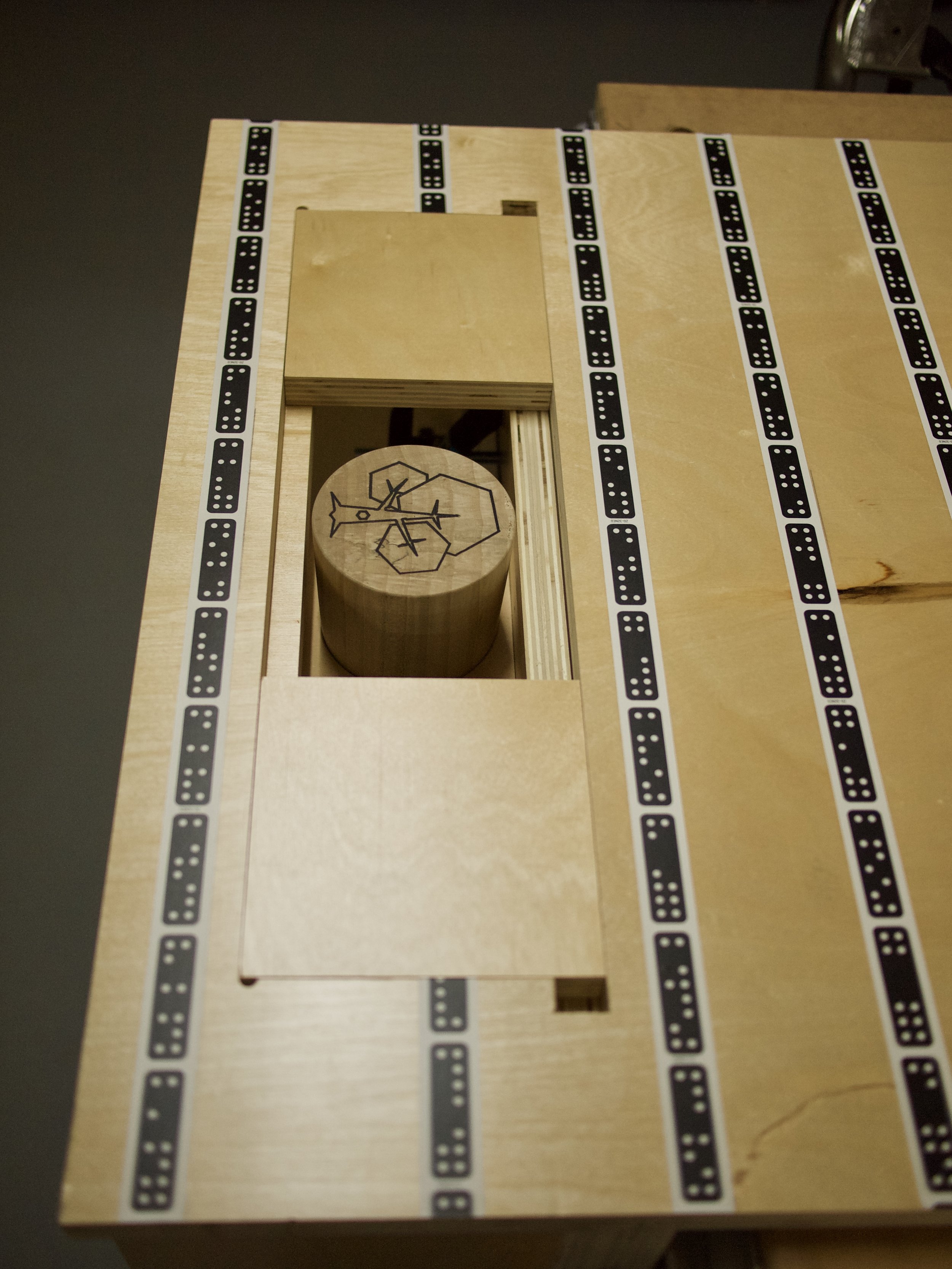
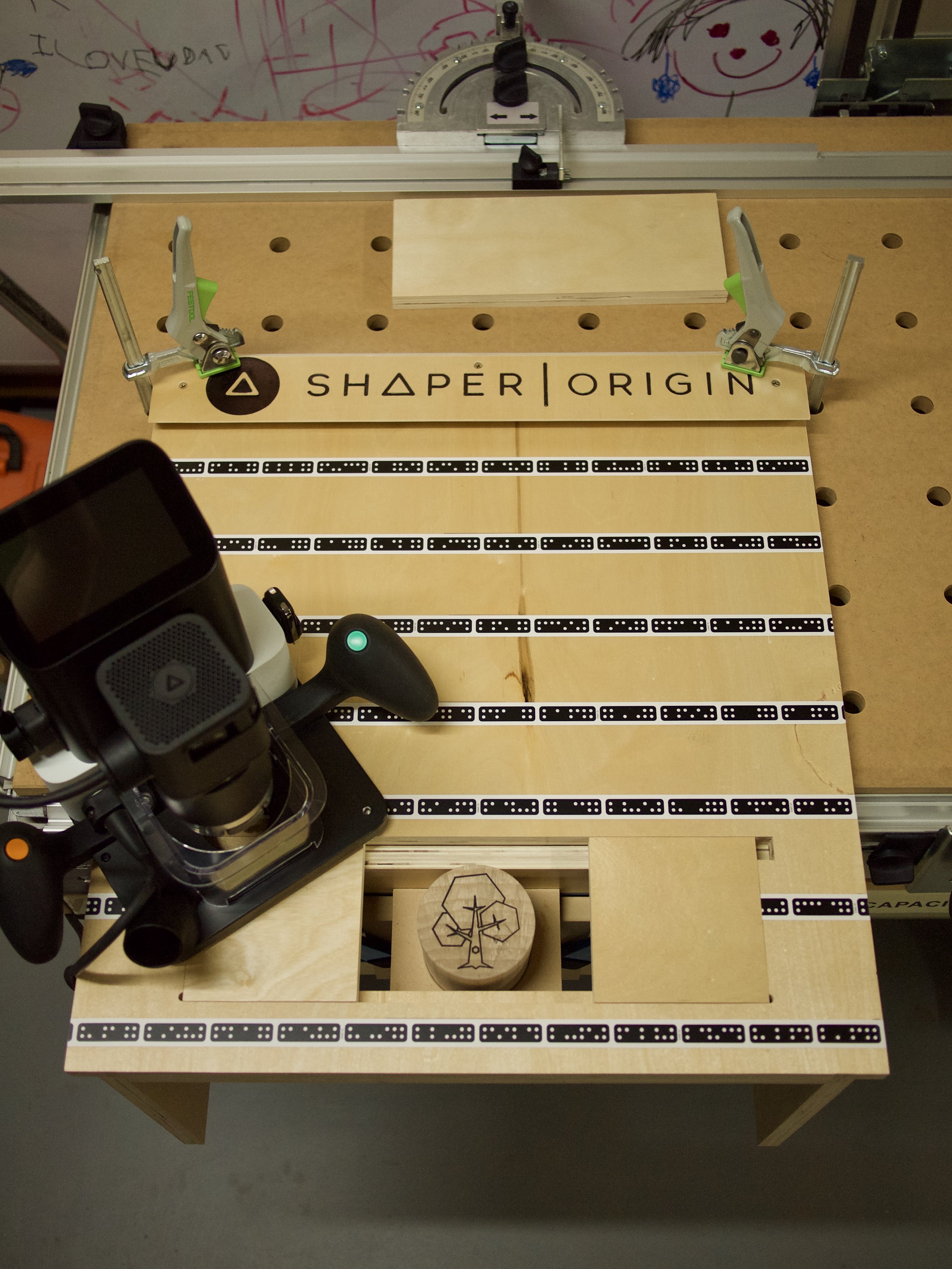
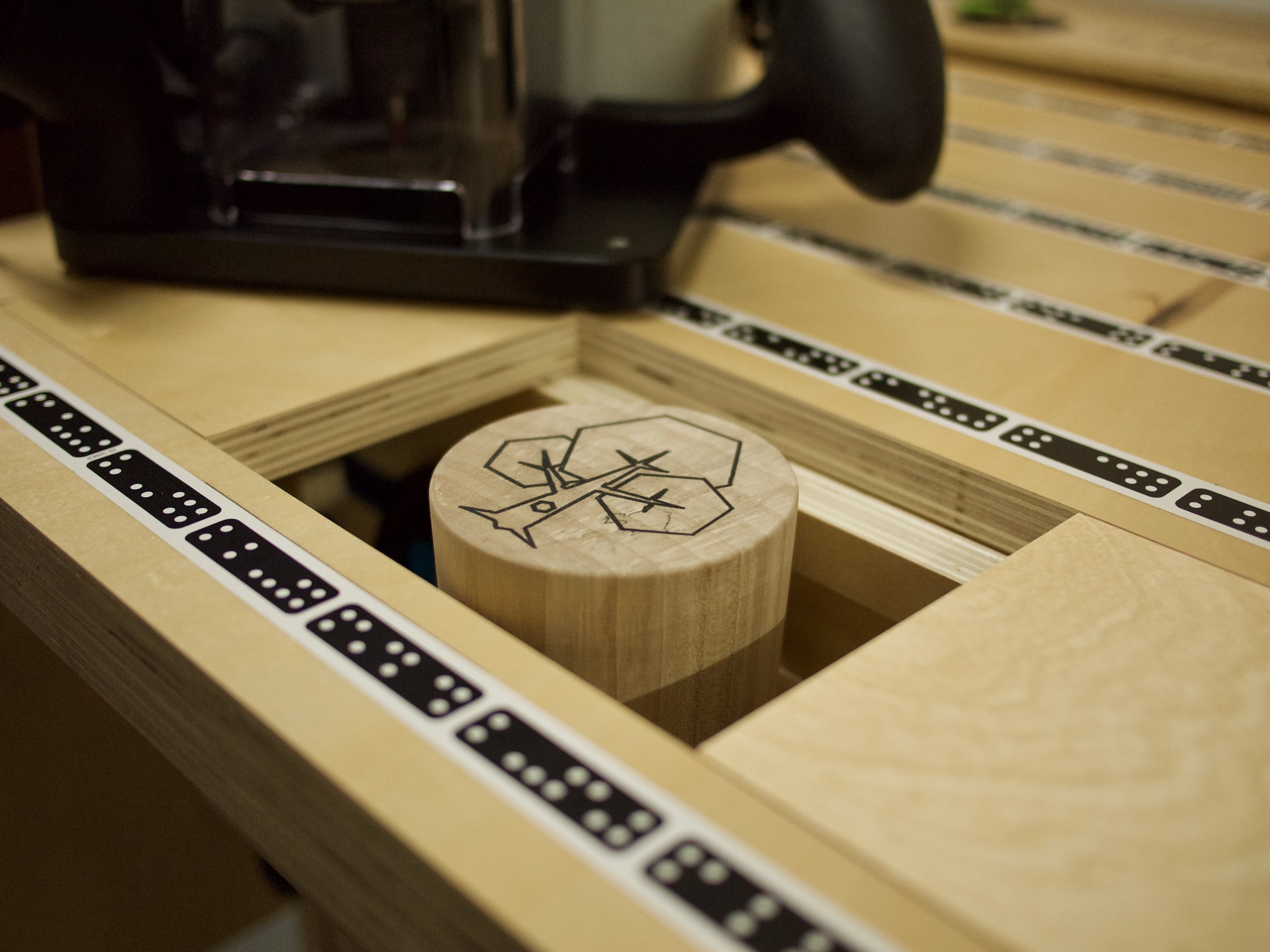
T-tracks and Support Stops
I was adding some height to the piece where the t-tracks were so I had room to add a third track PLUS the Rockler 48'' Universal T-Track with Hold-Down Clamps gave me exactly the length of track I needed to get 3 x 16" pieces!
Again, I was looking at the first build and was considering adding a third hole for the dowel used in the original Shaper design but then I realized that because I was using a bit longer t-track I could simple use that for the vertical support. This came out better than I thought because it opened the door to using the support in not only multiple locations horizontally but at various angles as well. I did finally use Fusion360 to figure out where the knob would be on the third track at 45 degrees and put a notch in the support piece to easily reproduce that angle. I'm sure I'll make another support with multiple notches for commonly used angles in both directions.
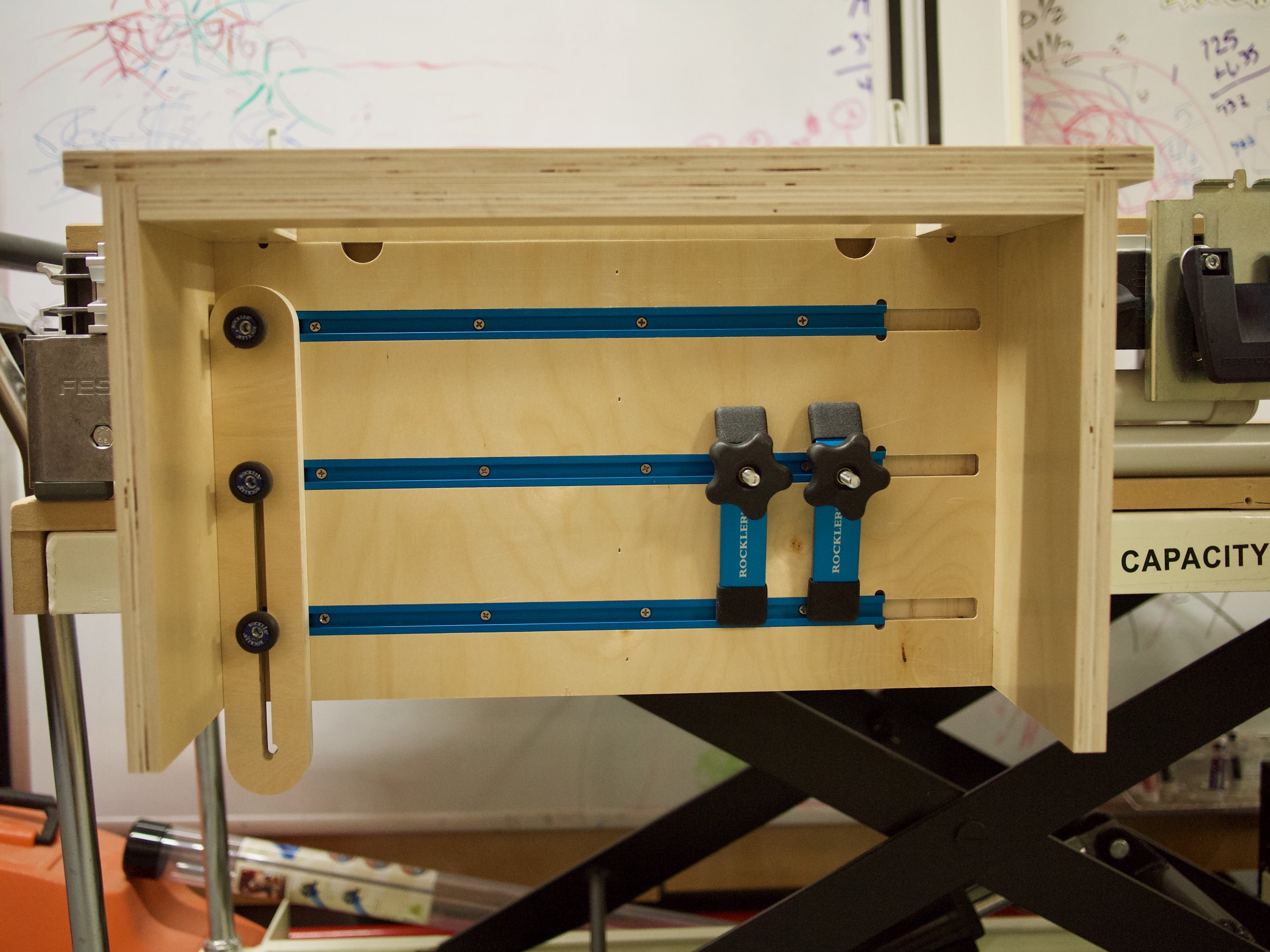
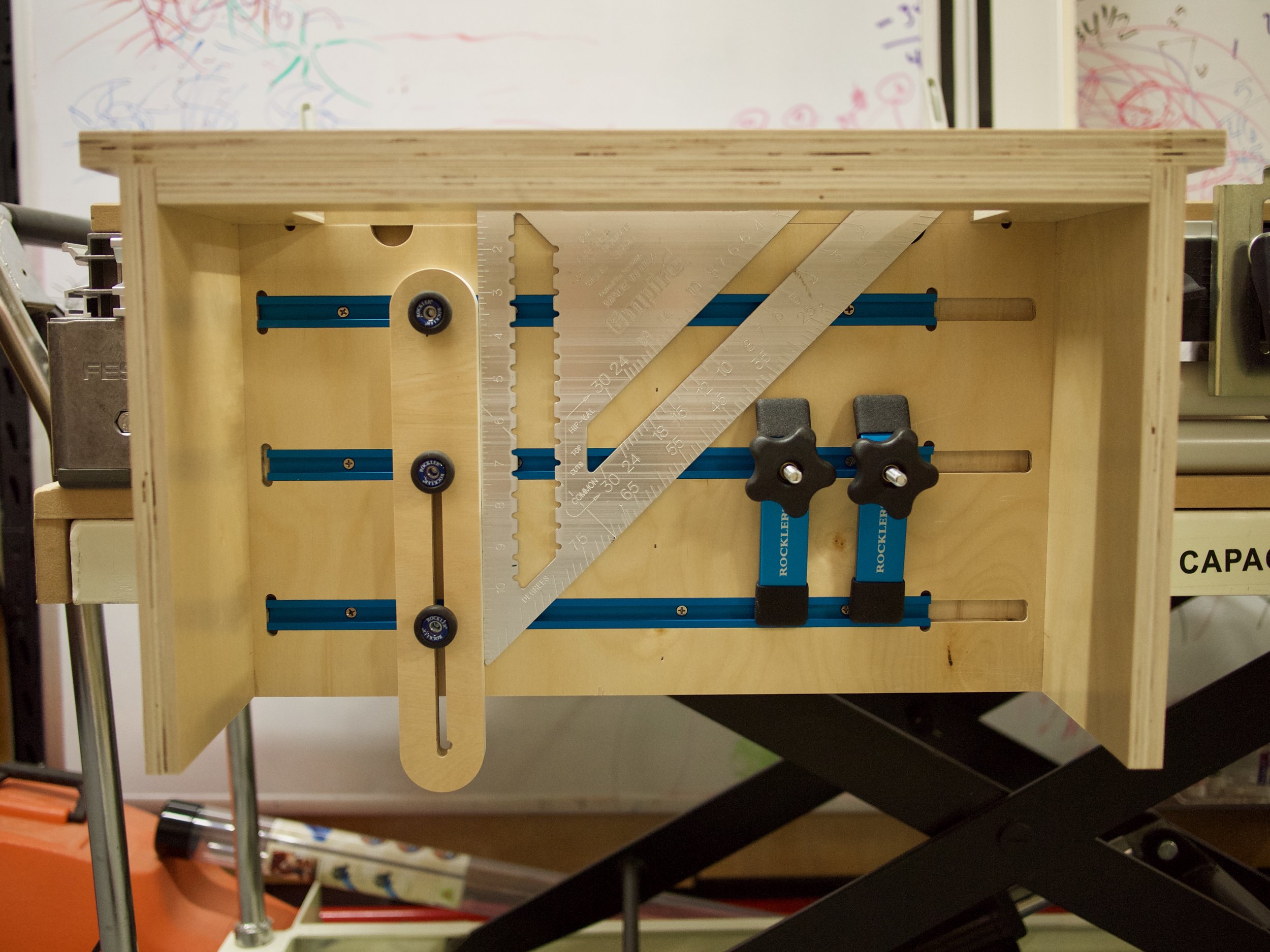
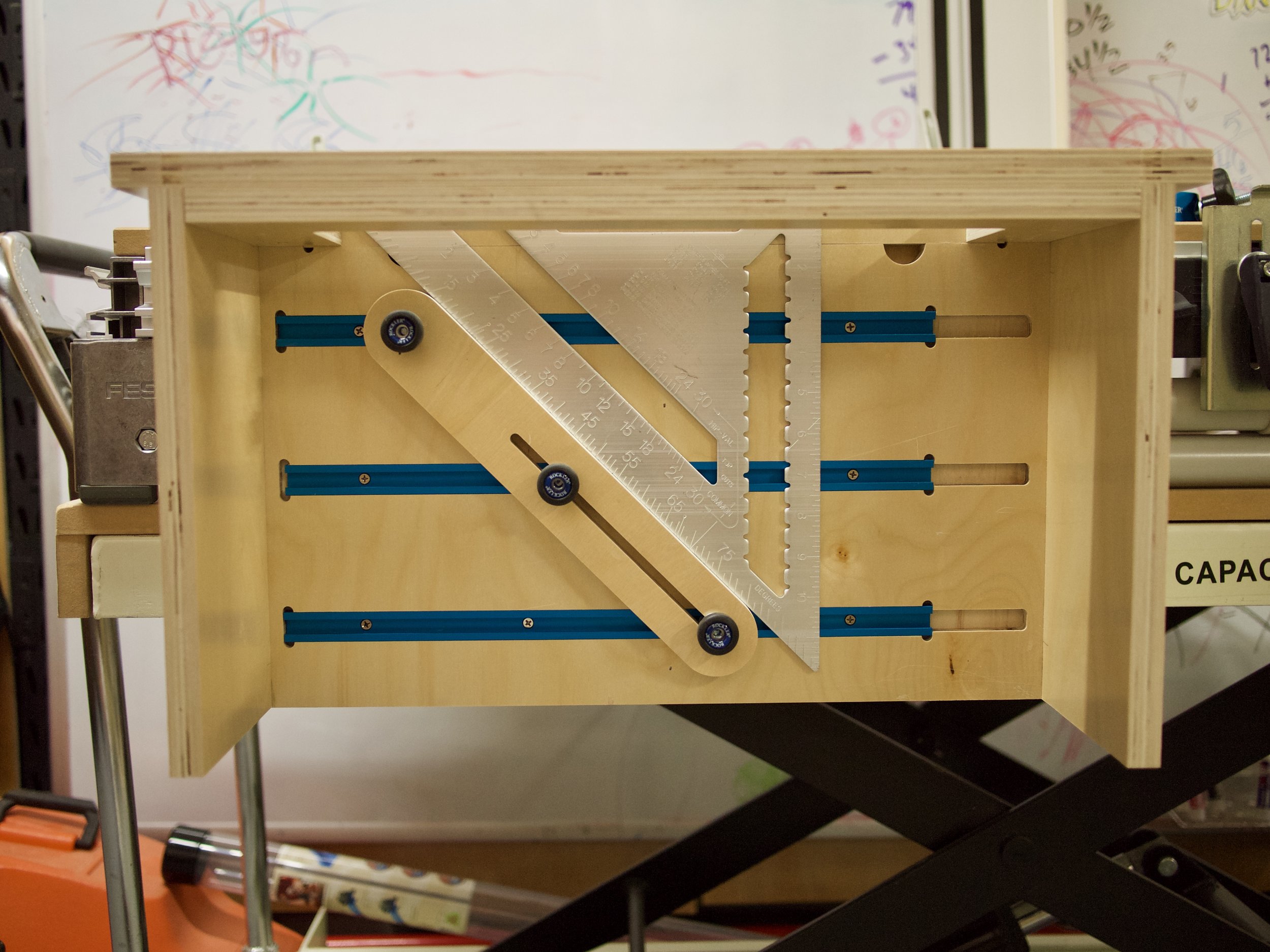
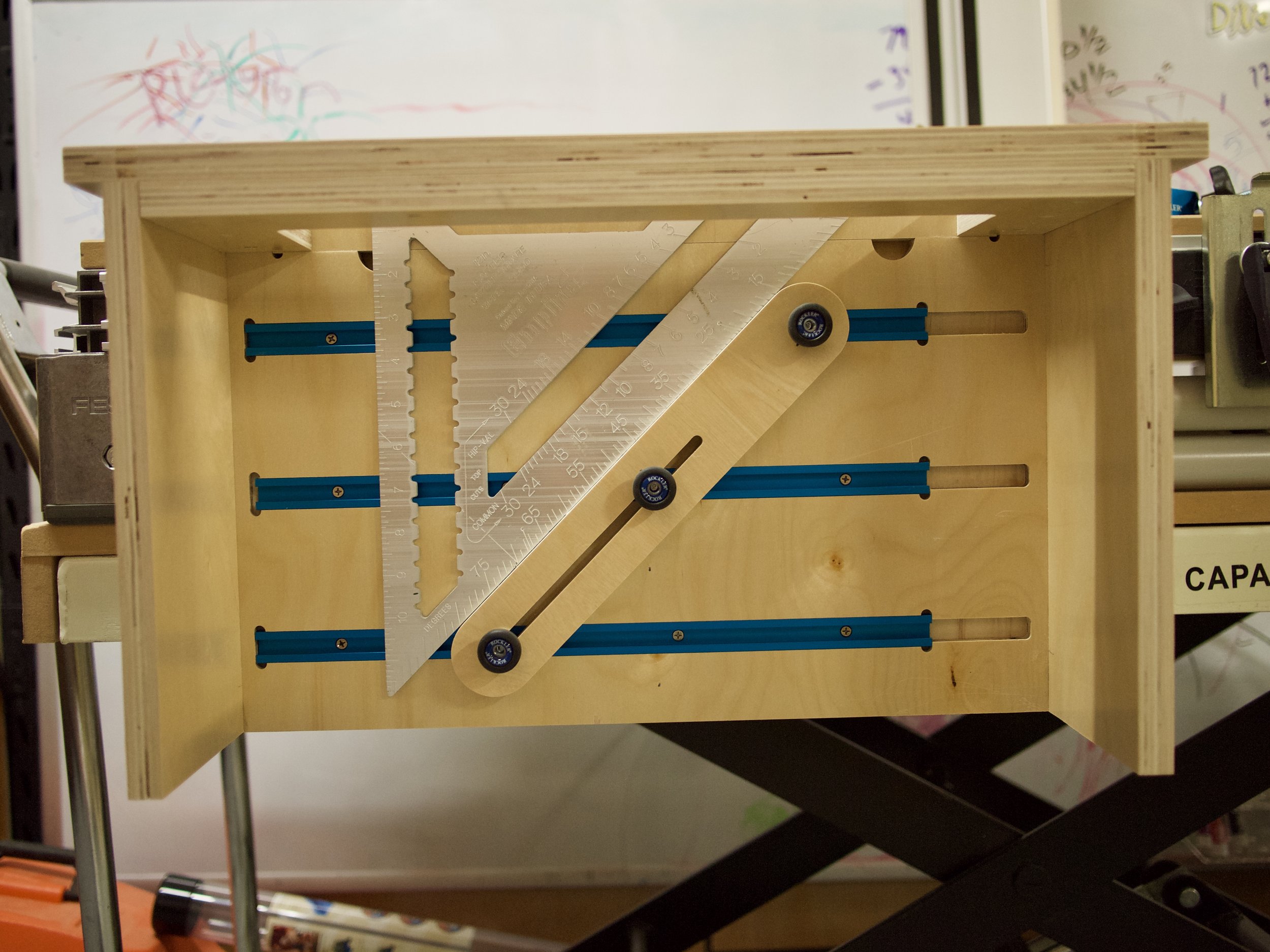
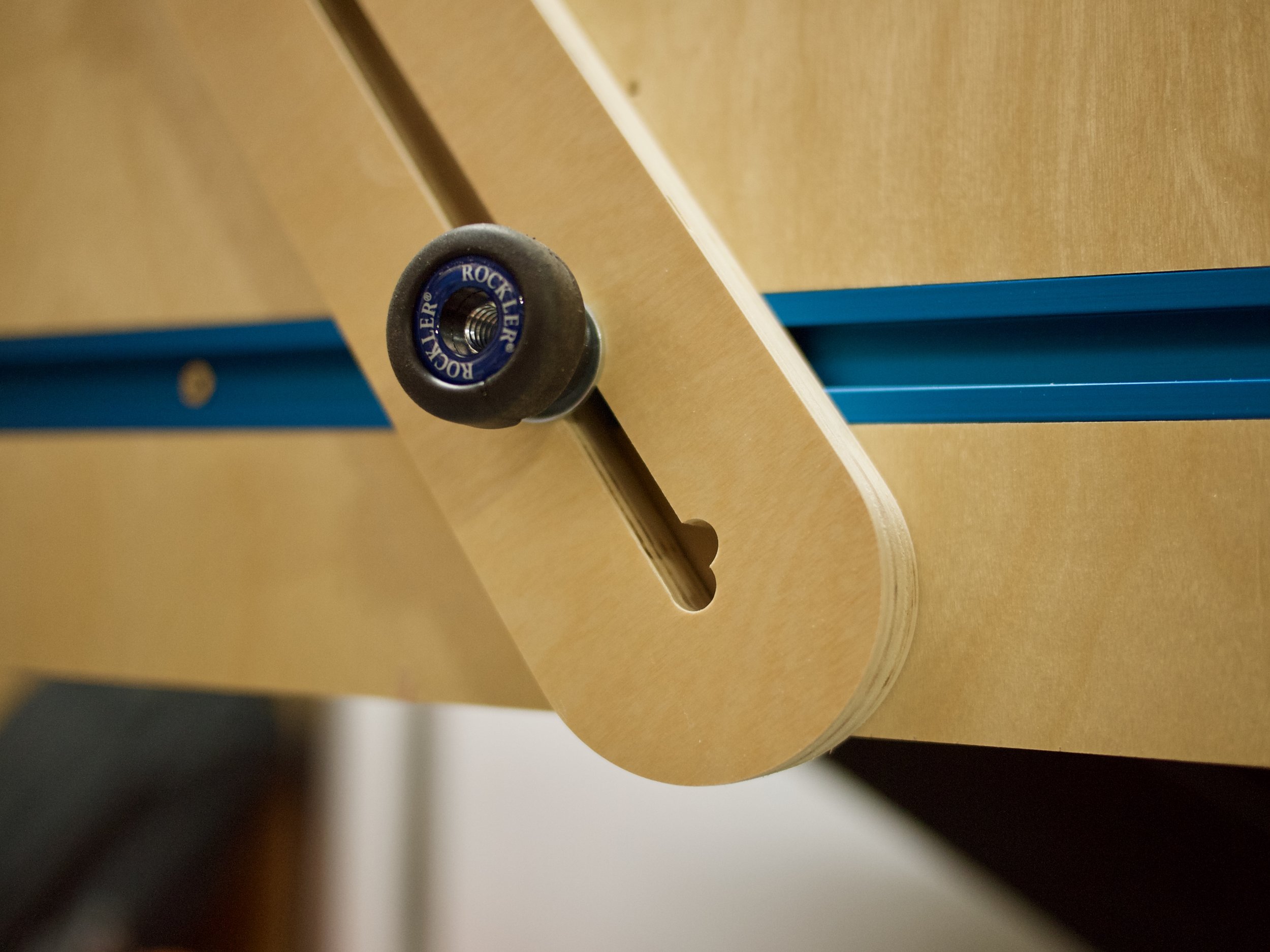
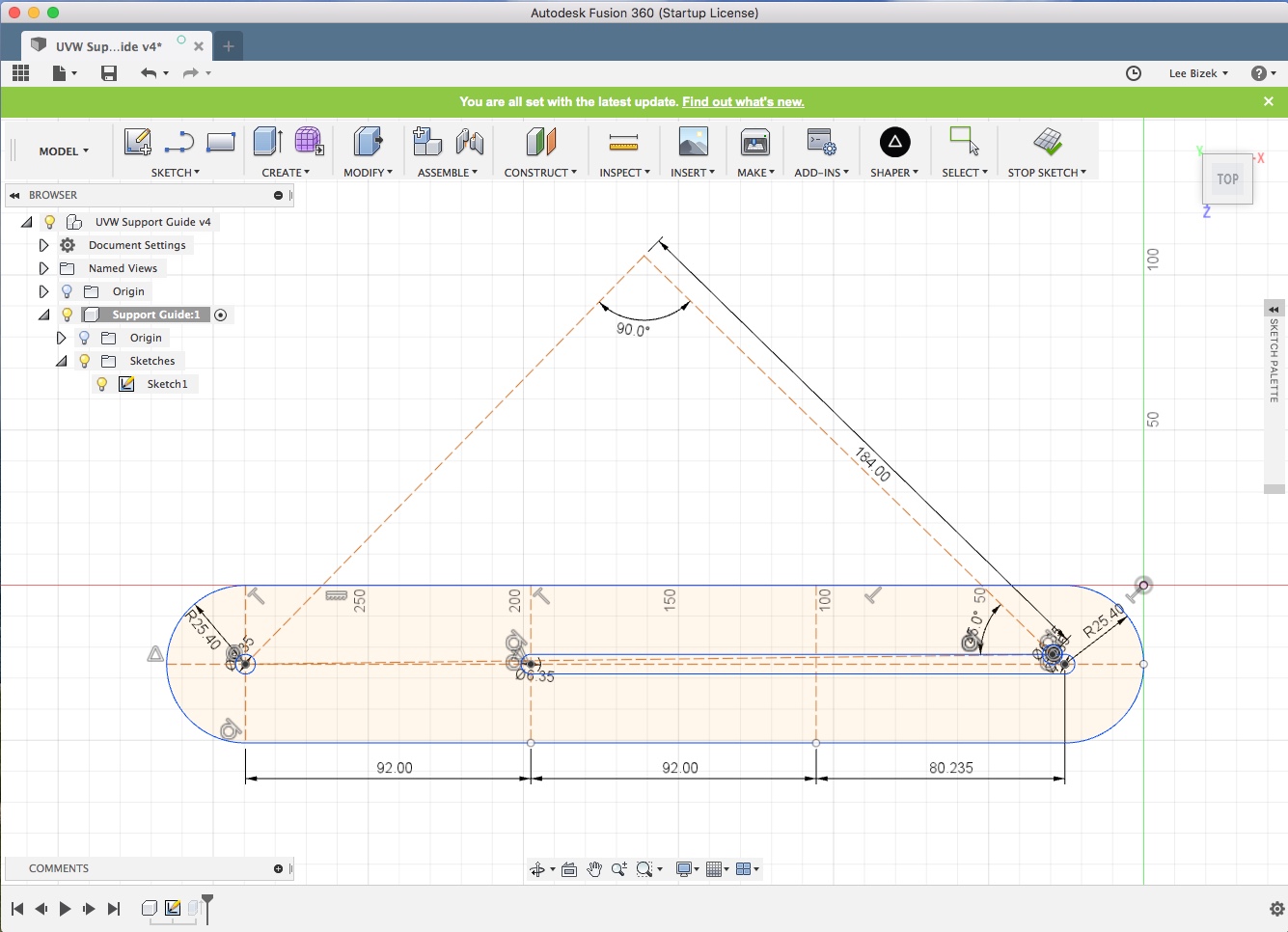
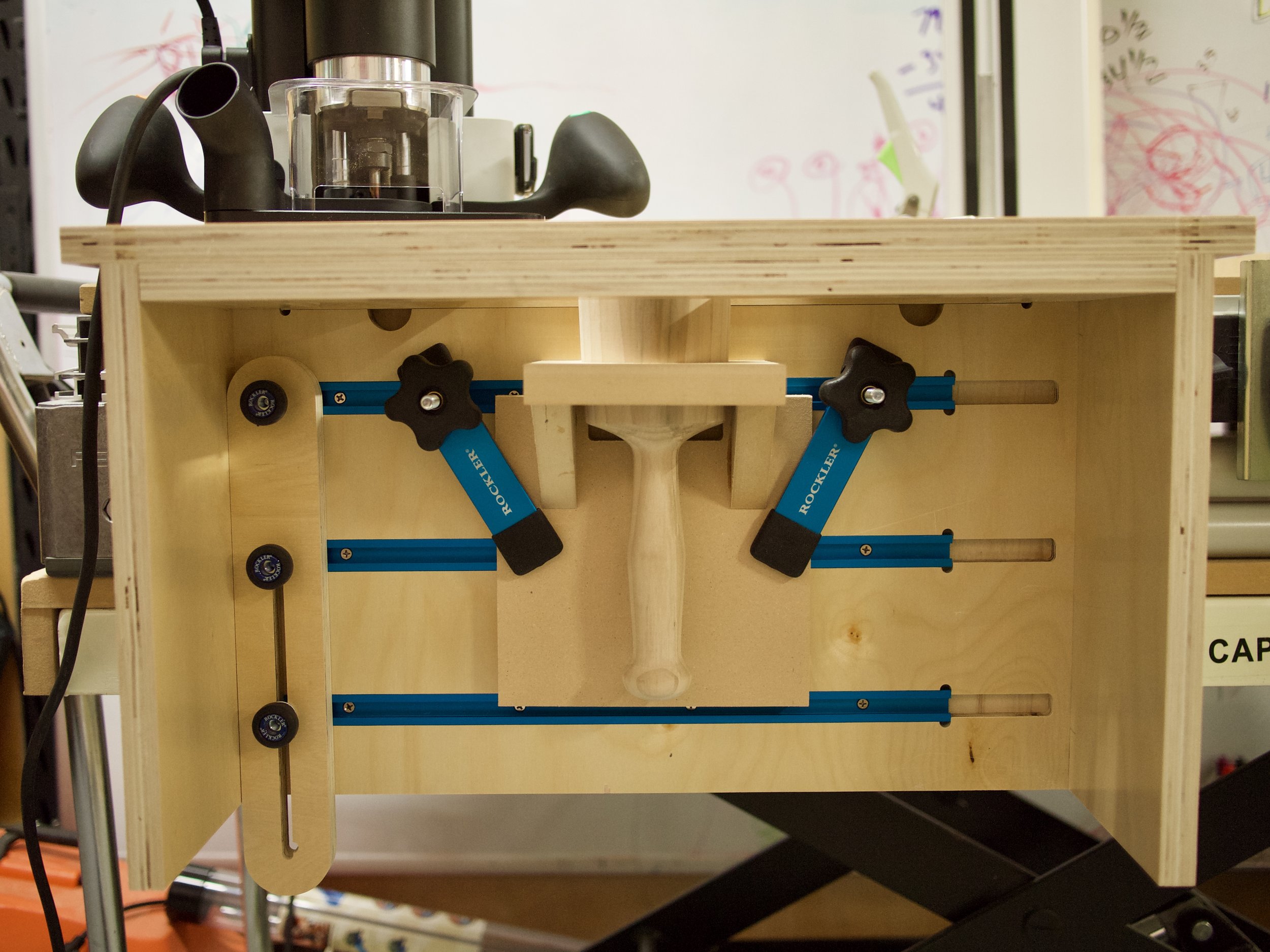
Final Touches
Of course, it wouldn't be the "Ultimate" Vertical Workstation without embellishing it with the Shaper Origin logos. :-) I used a Sharpie to color in the engraved logos.
Anyway, it was a great learning experience and I love how it all came together. It will be a great addition to the workshop.